کد مقاله | کد نشریه | سال انتشار | مقاله انگلیسی | نسخه تمام متن |
---|---|---|---|---|
1600514 | 1515889 | 2012 | 7 صفحه PDF | دانلود رایگان |
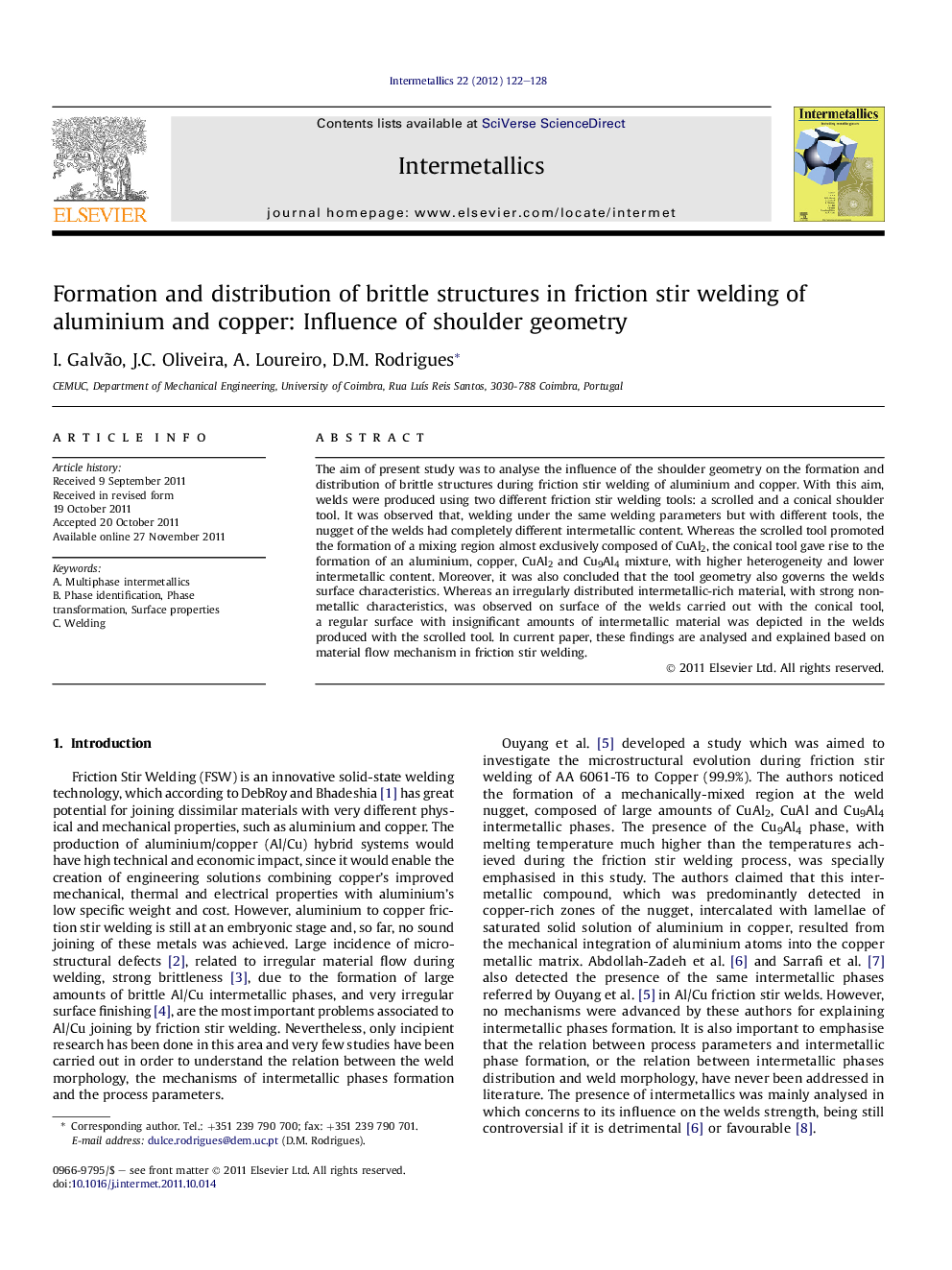
The aim of present study was to analyse the influence of the shoulder geometry on the formation and distribution of brittle structures during friction stir welding of aluminium and copper. With this aim, welds were produced using two different friction stir welding tools: a scrolled and a conical shoulder tool. It was observed that, welding under the same welding parameters but with different tools, the nugget of the welds had completely different intermetallic content. Whereas the scrolled tool promoted the formation of a mixing region almost exclusively composed of CuAl2, the conical tool gave rise to the formation of an aluminium, copper, CuAl2 and Cu9Al4 mixture, with higher heterogeneity and lower intermetallic content. Moreover, it was also concluded that the tool geometry also governs the welds surface characteristics. Whereas an irregularly distributed intermetallic-rich material, with strong non-metallic characteristics, was observed on surface of the welds carried out with the conical tool, a regular surface with insignificant amounts of intermetallic material was depicted in the welds produced with the scrolled tool. In current paper, these findings are analysed and explained based on material flow mechanism in friction stir welding.
Figure optionsDownload as PowerPoint slideHighlights
► Intermetallic phase formation is governed by material flow mechanisms during FSW.
► Tool geometry strongly influences the intermetallic nature and distribution.
► The quantity and distribution of the intermetallics determine weld characteristics.
Journal: Intermetallics - Volume 22, March 2012, Pages 122–128