کد مقاله | کد نشریه | سال انتشار | مقاله انگلیسی | نسخه تمام متن |
---|---|---|---|---|
1697033 | 1012031 | 2013 | 8 صفحه PDF | دانلود رایگان |
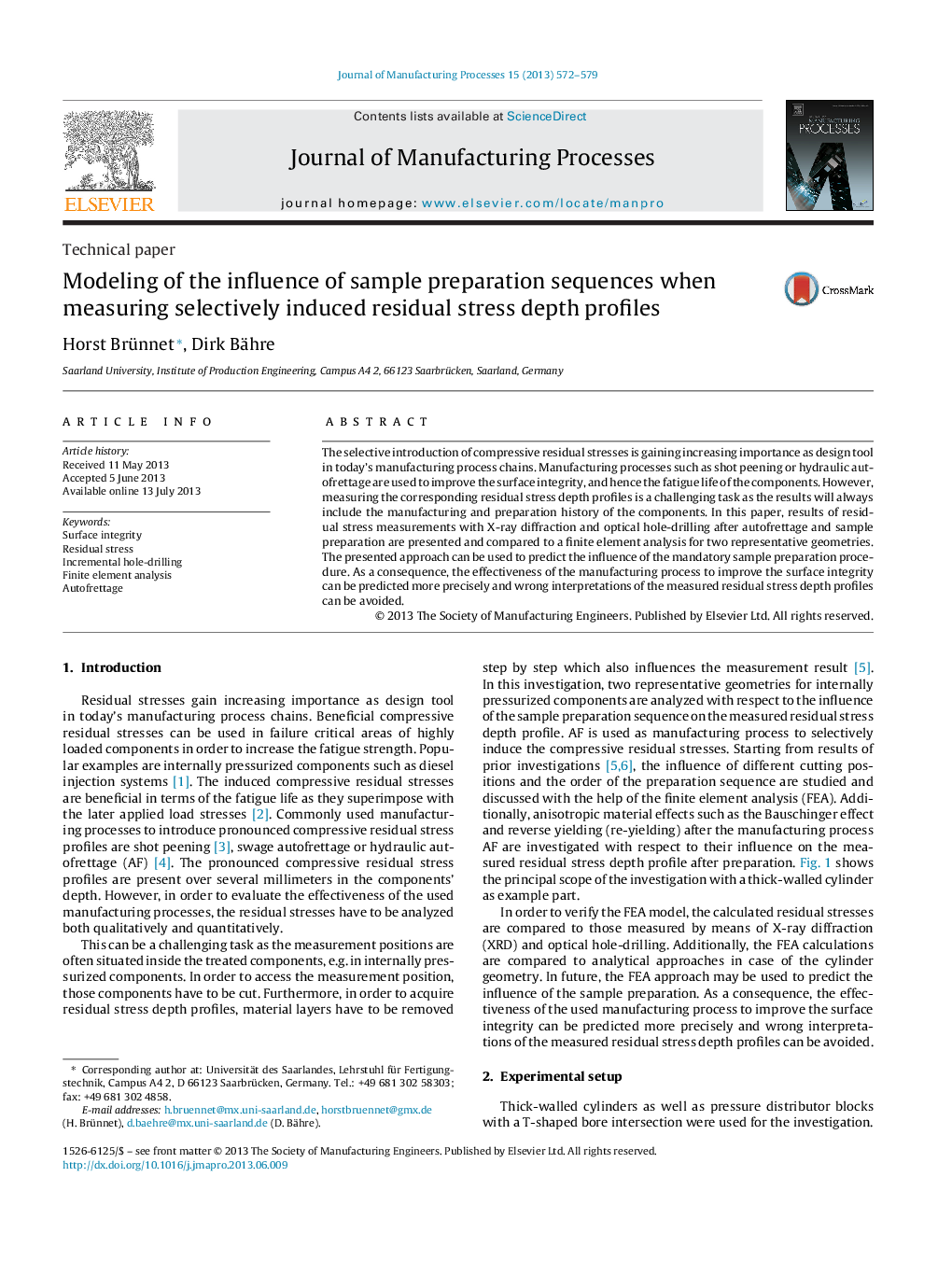
The selective introduction of compressive residual stresses is gaining increasing importance as design tool in today's manufacturing process chains. Manufacturing processes such as shot peening or hydraulic autofrettage are used to improve the surface integrity, and hence the fatigue life of the components. However, measuring the corresponding residual stress depth profiles is a challenging task as the results will always include the manufacturing and preparation history of the components. In this paper, results of residual stress measurements with X-ray diffraction and optical hole-drilling after autofrettage and sample preparation are presented and compared to a finite element analysis for two representative geometries. The presented approach can be used to predict the influence of the mandatory sample preparation procedure. As a consequence, the effectiveness of the manufacturing process to improve the surface integrity can be predicted more precisely and wrong interpretations of the measured residual stress depth profiles can be avoided.
Journal: Journal of Manufacturing Processes - Volume 15, Issue 4, October 2013, Pages 572–579