کد مقاله | کد نشریه | سال انتشار | مقاله انگلیسی | نسخه تمام متن |
---|---|---|---|---|
236393 | 465671 | 2013 | 7 صفحه PDF | دانلود رایگان |
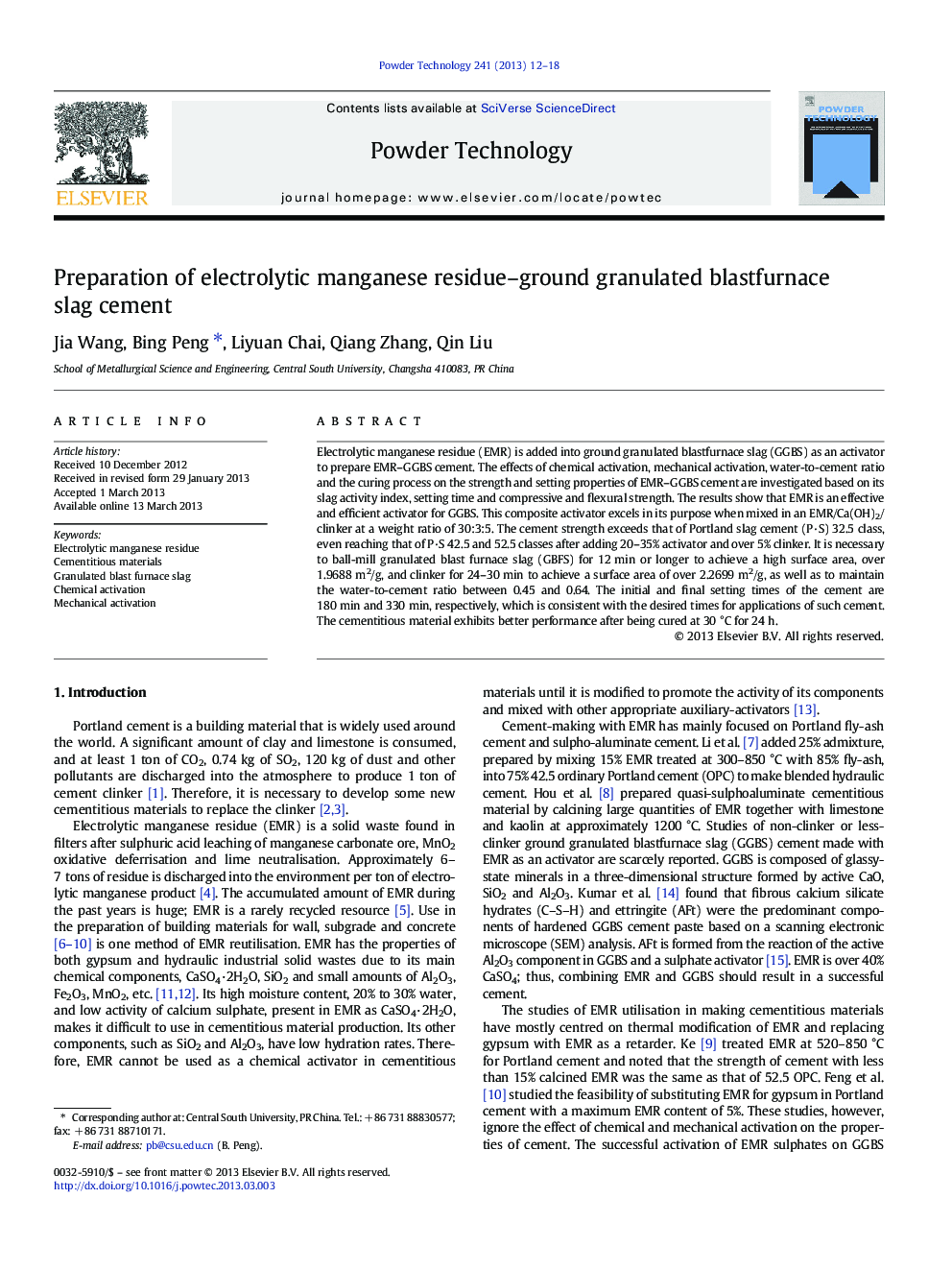
• EMR is added into GGBS as an activator to prepare EMR-GGBS cement.
• Chemical and mechanical activation are used to enhance the cement performance.
• EMR is the primary determinant of chemical activation on GGBS.
• Separate grinding shows better mechanical activation on cement than intergrinding.
• Preparation of EMR-GGBS cement is completed and process parameters are optimized.
Electrolytic manganese residue (EMR) is added into ground granulated blastfurnace slag (GGBS) as an activator to prepare EMR–GGBS cement. The effects of chemical activation, mechanical activation, water-to-cement ratio and the curing process on the strength and setting properties of EMR–GGBS cement are investigated based on its slag activity index, setting time and compressive and flexural strength. The results show that EMR is an effective and efficient activator for GGBS. This composite activator excels in its purpose when mixed in an EMR/Ca(OH)2/clinker at a weight ratio of 30:3:5. The cement strength exceeds that of Portland slag cement (P·S) 32.5 class, even reaching that of P·S 42.5 and 52.5 classes after adding 20–35% activator and over 5% clinker. It is necessary to ball-mill granulated blast furnace slag (GBFS) for 12 min or longer to achieve a high surface area, over 1.9688 m2/g, and clinker for 24–30 min to achieve a surface area of over 2.2699 m2/g, as well as to maintain the water-to-cement ratio between 0.45 and 0.64. The initial and final setting times of the cement are 180 min and 330 min, respectively, which is consistent with the desired times for applications of such cement. The cementitious material exhibits better performance after being cured at 30 °C for 24 h.
Figure optionsDownload as PowerPoint slide
Journal: Powder Technology - Volume 241, June 2013, Pages 12–18