کد مقاله | کد نشریه | سال انتشار | مقاله انگلیسی | نسخه تمام متن |
---|---|---|---|---|
236703 | 465682 | 2013 | 19 صفحه PDF | دانلود رایگان |
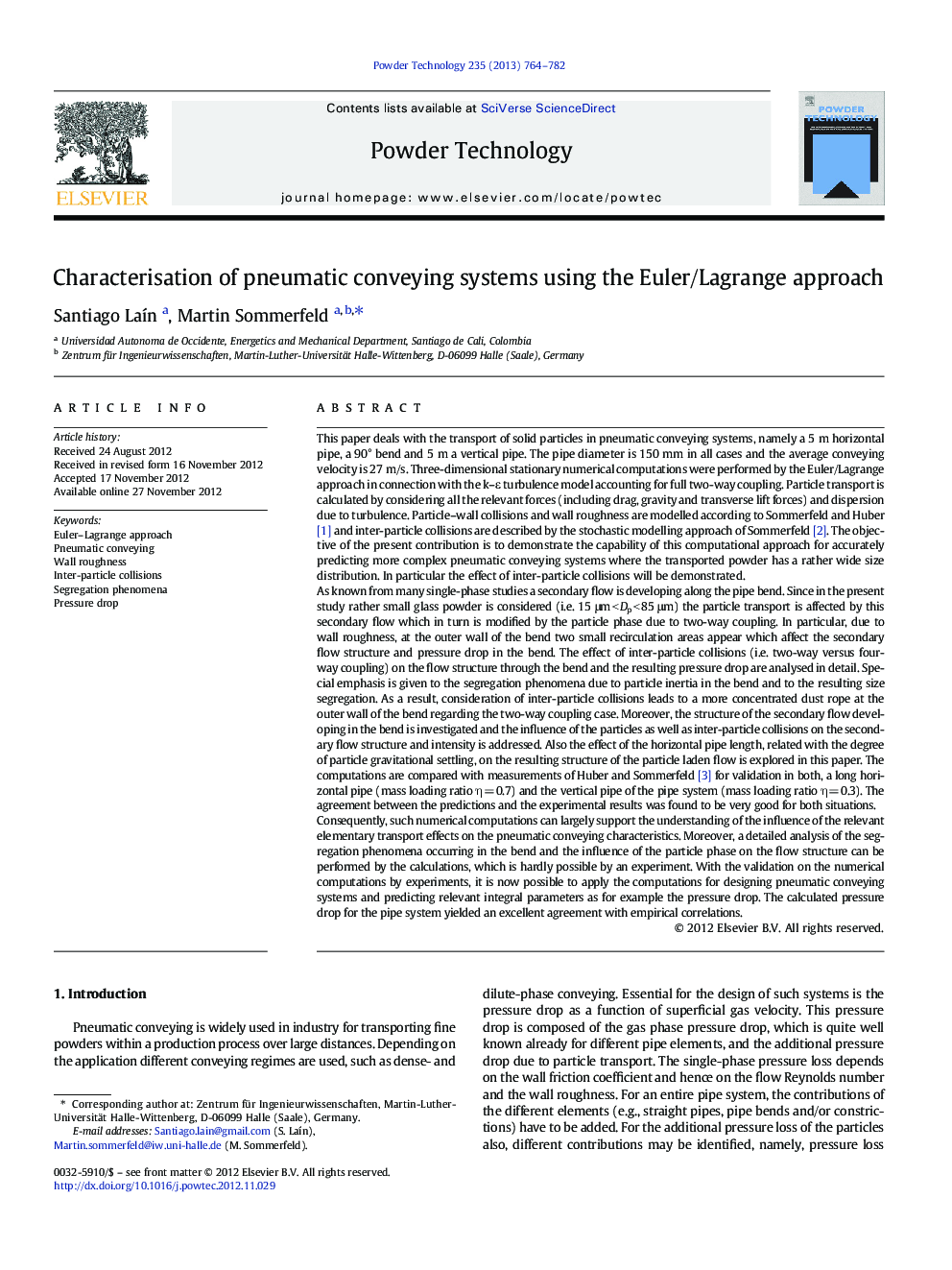
This paper deals with the transport of solid particles in pneumatic conveying systems, namely a 5 m horizontal pipe, a 90° bend and 5 m a vertical pipe. The pipe diameter is 150 mm in all cases and the average conveying velocity is 27 m/s. Three-dimensional stationary numerical computations were performed by the Euler/Lagrange approach in connection with the k–ε turbulence model accounting for full two-way coupling. Particle transport is calculated by considering all the relevant forces (including drag, gravity and transverse lift forces) and dispersion due to turbulence. Particle–wall collisions and wall roughness are modelled according to Sommerfeld and Huber [1] and inter-particle collisions are described by the stochastic modelling approach of Sommerfeld [2]. The objective of the present contribution is to demonstrate the capability of this computational approach for accurately predicting more complex pneumatic conveying systems where the transported powder has a rather wide size distribution. In particular the effect of inter-particle collisions will be demonstrated.As known from many single-phase studies a secondary flow is developing along the pipe bend. Since in the present study rather small glass powder is considered (i.e. 15 μm < Dp < 85 μm) the particle transport is affected by this secondary flow which in turn is modified by the particle phase due to two-way coupling. In particular, due to wall roughness, at the outer wall of the bend two small recirculation areas appear which affect the secondary flow structure and pressure drop in the bend. The effect of inter-particle collisions (i.e. two-way versus four-way coupling) on the flow structure through the bend and the resulting pressure drop are analysed in detail. Special emphasis is given to the segregation phenomena due to particle inertia in the bend and to the resulting size segregation. As a result, consideration of inter-particle collisions leads to a more concentrated dust rope at the outer wall of the bend regarding the two-way coupling case. Moreover, the structure of the secondary flow developing in the bend is investigated and the influence of the particles as well as inter-particle collisions on the secondary flow structure and intensity is addressed. Also the effect of the horizontal pipe length, related with the degree of particle gravitational settling, on the resulting structure of the particle laden flow is explored in this paper. The computations are compared with measurements of Huber and Sommerfeld [3] for validation in both, a long horizontal pipe (mass loading ratio η = 0.7) and the vertical pipe of the pipe system (mass loading ratio η = 0.3). The agreement between the predictions and the experimental results was found to be very good for both situations.Consequently, such numerical computations can largely support the understanding of the influence of the relevant elementary transport effects on the pneumatic conveying characteristics. Moreover, a detailed analysis of the segregation phenomena occurring in the bend and the influence of the particle phase on the flow structure can be performed by the calculations, which is hardly possible by an experiment. With the validation on the numerical computations by experiments, it is now possible to apply the computations for designing pneumatic conveying systems and predicting relevant integral parameters as for example the pressure drop. The calculated pressure drop for the pipe system yielded an excellent agreement with empirical correlations.
The transport of solid particles in pneumatic conveying systems, namely a 5 m horizontal pipe, a 90° bend and 5 m a vertical pipe, is analyzed by means of the Euler-Lagrange approach. Influence of momentum coupling and collisions (inter-particle and particle-rough wall) on two-phase flow structure in the system is studied.Figure optionsDownload as PowerPoint slideHighlights
► Prediction of dilute-phase pneumatic conveying systems by Euler/Lagrange approach.
► Good agreement with measurements for horizontal and vertical conveying pipes.
► Influence of momentum coupling & collisions on two-phase flow structure in the system.
► Analysis of the secondary flow modification by the particles.
► Prediction of pressure drop showing good agreement with empirical correlations.
Journal: Powder Technology - Volume 235, February 2013, Pages 764–782