کد مقاله | کد نشریه | سال انتشار | مقاله انگلیسی | نسخه تمام متن |
---|---|---|---|---|
236814 | 465686 | 2013 | 9 صفحه PDF | دانلود رایگان |
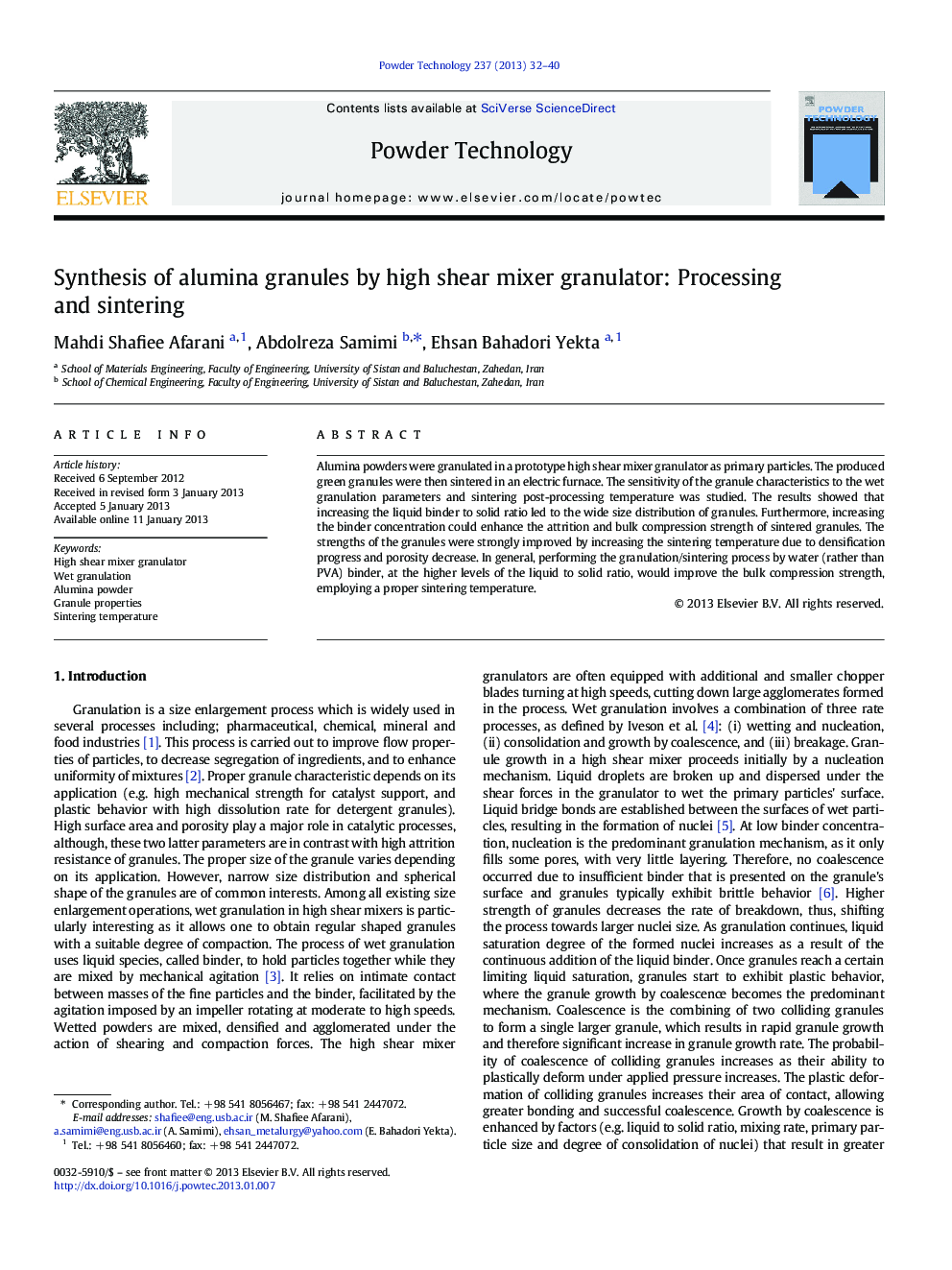
Alumina powders were granulated in a prototype high shear mixer granulator as primary particles. The produced green granules were then sintered in an electric furnace. The sensitivity of the granule characteristics to the wet granulation parameters and sintering post-processing temperature was studied. The results showed that increasing the liquid binder to solid ratio led to the wide size distribution of granules. Furthermore, increasing the binder concentration could enhance the attrition and bulk compression strength of sintered granules. The strengths of the granules were strongly improved by increasing the sintering temperature due to densification progress and porosity decrease. In general, performing the granulation/sintering process by water (rather than PVA) binder, at the higher levels of the liquid to solid ratio, would improve the bulk compression strength, employing a proper sintering temperature.
The effect of different compaction route and silica addition, as well as sintering temperature on samples’ microstructure, porosity, shrinkage, surface area, flexural/compressive strengths, and heat conductivity was investigated.Figure optionsDownload as PowerPoint slideHighlights
► Alumina powder was granulated and sintered in high shear mixer and electric furnace.
► Effect of granulation/sintering factors on granule properties was studied.
► Strength of granule was improved by increasing temperature due to porosity decrease.
► Water binder at proper L/S and sintering temperature improved the strength.
Journal: Powder Technology - Volume 237, March 2013, Pages 32–40