کد مقاله | کد نشریه | سال انتشار | مقاله انگلیسی | نسخه تمام متن |
---|---|---|---|---|
237180 | 465697 | 2012 | 8 صفحه PDF | دانلود رایگان |
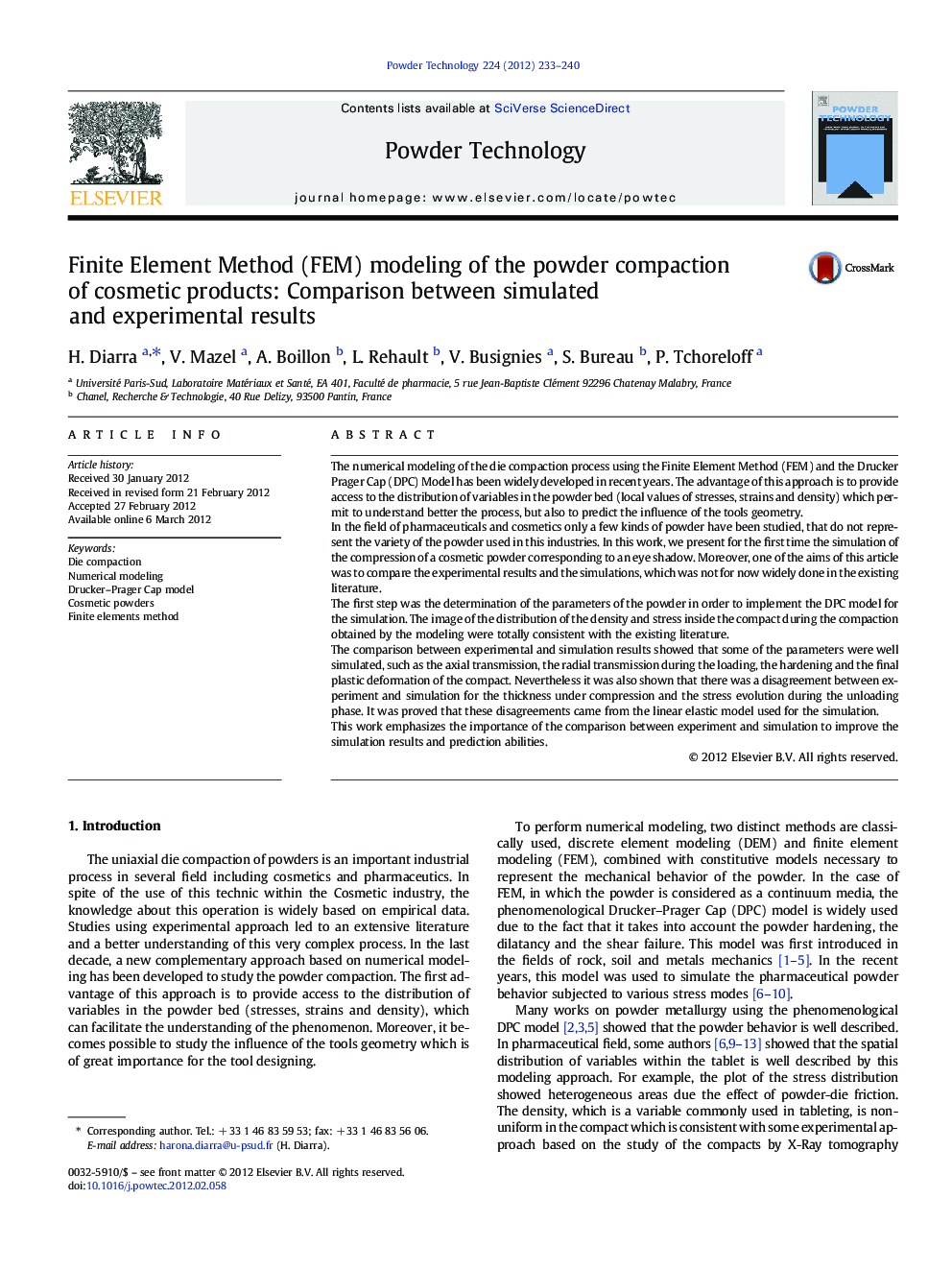
The numerical modeling of the die compaction process using the Finite Element Method (FEM) and the Drucker Prager Cap (DPC) Model has been widely developed in recent years. The advantage of this approach is to provide access to the distribution of variables in the powder bed (local values of stresses, strains and density) which permit to understand better the process, but also to predict the influence of the tools geometry.In the field of pharmaceuticals and cosmetics only a few kinds of powder have been studied, that do not represent the variety of the powder used in this industries. In this work, we present for the first time the simulation of the compression of a cosmetic powder corresponding to an eye shadow. Moreover, one of the aims of this article was to compare the experimental results and the simulations, which was not for now widely done in the existing literature.The first step was the determination of the parameters of the powder in order to implement the DPC model for the simulation. The image of the distribution of the density and stress inside the compact during the compaction obtained by the modeling were totally consistent with the existing literature.The comparison between experimental and simulation results showed that some of the parameters were well simulated, such as the axial transmission, the radial transmission during the loading, the hardening and the final plastic deformation of the compact. Nevertheless it was also shown that there was a disagreement between experiment and simulation for the thickness under compression and the stress evolution during the unloading phase. It was proved that these disagreements came from the linear elastic model used for the simulation.This work emphasizes the importance of the comparison between experiment and simulation to improve the simulation results and prediction abilities.
Figure optionsDownload as PowerPoint slideHighlights
► Simulation model was performed to describe die compaction process on cosmetic powder.
► Comparisons between experimental curves and finite element method curves were done.
► Axial and radial transmission curves and compression path were plotted.
► We showed that the powder hardening and the final deformation are well simulated.
► Due to the use of a linear elasticity, elastic recovery is not very well predicted.
Journal: Powder Technology - Volume 224, July 2012, Pages 233–240