کد مقاله | کد نشریه | سال انتشار | مقاله انگلیسی | نسخه تمام متن |
---|---|---|---|---|
239106 | 465796 | 2008 | 13 صفحه PDF | دانلود رایگان |
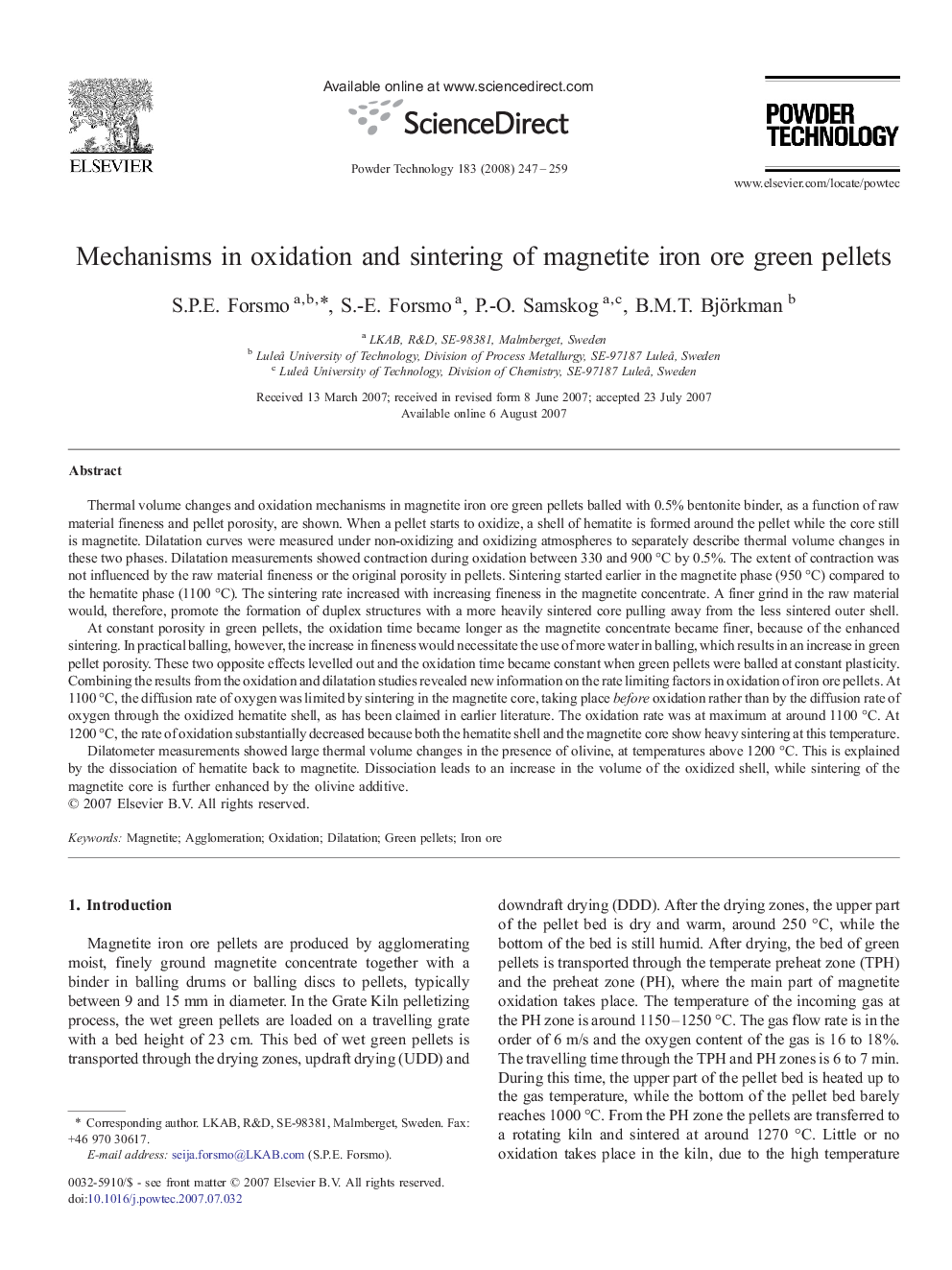
Thermal volume changes and oxidation mechanisms in magnetite iron ore green pellets balled with 0.5% bentonite binder, as a function of raw material fineness and pellet porosity, are shown. When a pellet starts to oxidize, a shell of hematite is formed around the pellet while the core still is magnetite. Dilatation curves were measured under non-oxidizing and oxidizing atmospheres to separately describe thermal volume changes in these two phases. Dilatation measurements showed contraction during oxidation between 330 and 900 °C by 0.5%. The extent of contraction was not influenced by the raw material fineness or the original porosity in pellets. Sintering started earlier in the magnetite phase (950 °C) compared to the hematite phase (1100 °C). The sintering rate increased with increasing fineness in the magnetite concentrate. A finer grind in the raw material would, therefore, promote the formation of duplex structures with a more heavily sintered core pulling away from the less sintered outer shell.At constant porosity in green pellets, the oxidation time became longer as the magnetite concentrate became finer, because of the enhanced sintering. In practical balling, however, the increase in fineness would necessitate the use of more water in balling, which results in an increase in green pellet porosity. These two opposite effects levelled out and the oxidation time became constant when green pellets were balled at constant plasticity. Combining the results from the oxidation and dilatation studies revealed new information on the rate limiting factors in oxidation of iron ore pellets. At 1100 °C, the diffusion rate of oxygen was limited by sintering in the magnetite core, taking place before oxidation rather than by the diffusion rate of oxygen through the oxidized hematite shell, as has been claimed in earlier literature. The oxidation rate was at maximum at around 1100 °C. At 1200 °C, the rate of oxidation substantially decreased because both the hematite shell and the magnetite core show heavy sintering at this temperature.Dilatometer measurements showed large thermal volume changes in the presence of olivine, at temperatures above 1200 °C. This is explained by the dissociation of hematite back to magnetite. Dissociation leads to an increase in the volume of the oxidized shell, while sintering of the magnetite core is further enhanced by the olivine additive.
Principal mechanisms during oxidation and sintering (dilatation) of magnetite iron ore green pellets were studied. Special attention was paid on variations in raw material fineness and green pellet porosity. Increasing fineness enhances the unwanted Duplex structures. The dilatation measurements showed opposite thermal volume changes in the oxidized hematite shell and in the magnetite core in the presence of the olivine additive.Figure optionsDownload as PowerPoint slide
Journal: Powder Technology - Volume 183, Issue 2, 9 April 2008, Pages 247–259