کد مقاله | کد نشریه | سال انتشار | مقاله انگلیسی | نسخه تمام متن |
---|---|---|---|---|
301250 | 512500 | 2012 | 10 صفحه PDF | دانلود رایگان |
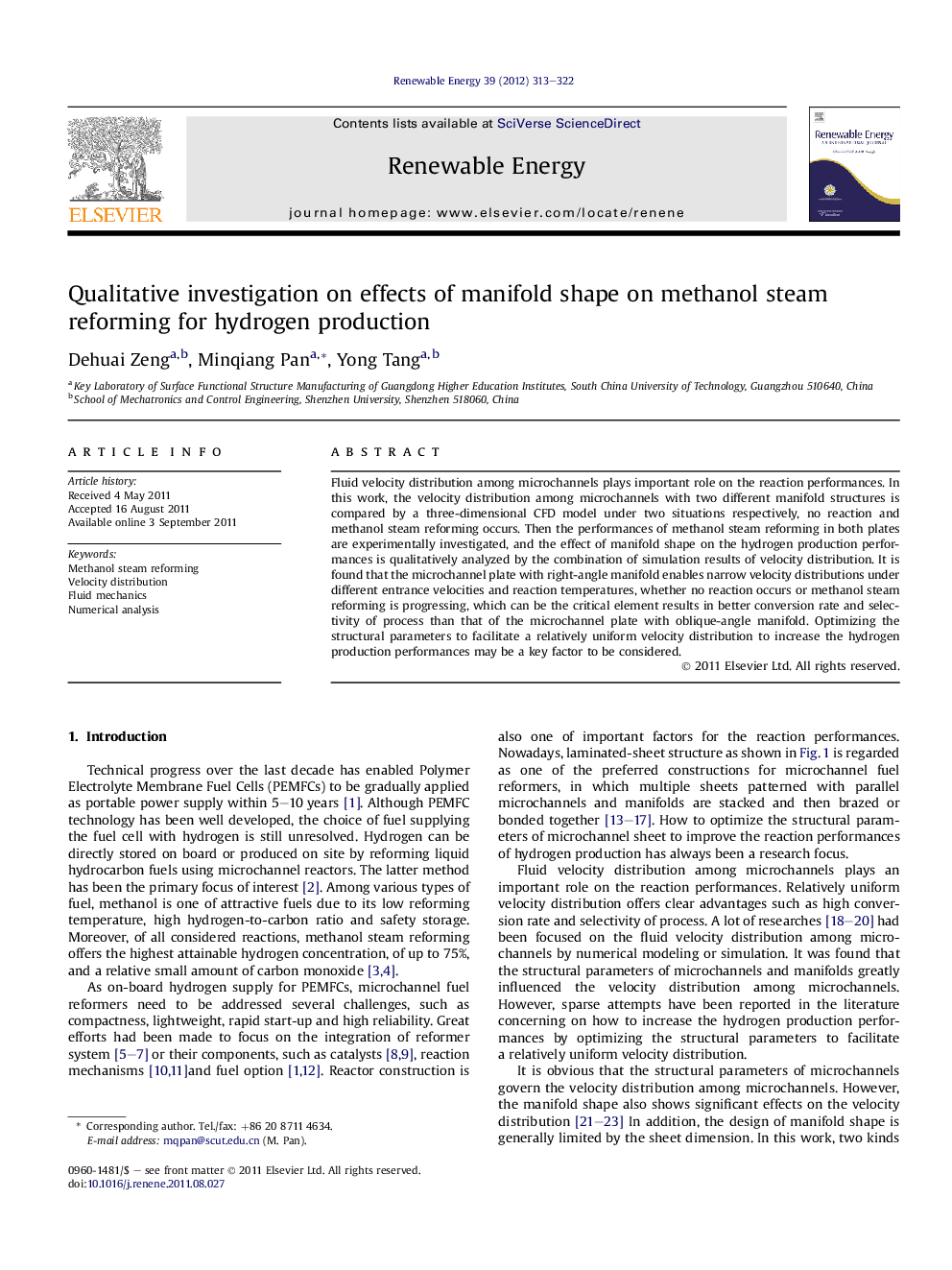
Fluid velocity distribution among microchannels plays important role on the reaction performances. In this work, the velocity distribution among microchannels with two different manifold structures is compared by a three-dimensional CFD model under two situations respectively, no reaction and methanol steam reforming occurs. Then the performances of methanol steam reforming in both plates are experimentally investigated, and the effect of manifold shape on the hydrogen production performances is qualitatively analyzed by the combination of simulation results of velocity distribution. It is found that the microchannel plate with right-angle manifold enables narrow velocity distributions under different entrance velocities and reaction temperatures, whether no reaction occurs or methanol steam reforming is progressing, which can be the critical element results in better conversion rate and selectivity of process than that of the microchannel plate with oblique-angle manifold. Optimizing the structural parameters to facilitate a relatively uniform velocity distribution to increase the hydrogen production performances may be a key factor to be considered.
► We analyzed the fluid velocity distribution by a three-dimensional CFD model.
► We investigated the effects of velocity distribution on methanol steam reforming.
► Microchannel plate with right-angle manifold enables narrow velocity distributions.
► Uniform velocity distributions could result in better reaction performances.
Journal: Renewable Energy - Volume 39, Issue 1, March 2012, Pages 313–322