کد مقاله | کد نشریه | سال انتشار | مقاله انگلیسی | نسخه تمام متن |
---|---|---|---|---|
5017842 | 1466727 | 2017 | 25 صفحه PDF | دانلود رایگان |
عنوان انگلیسی مقاله ISI
40Â kJ magnetic pulse welding system for expansion welding of aluminium 6061 tube
دانلود مقاله + سفارش ترجمه
دانلود مقاله ISI انگلیسی
رایگان برای ایرانیان
موضوعات مرتبط
مهندسی و علوم پایه
سایر رشته های مهندسی
مهندسی صنعتی و تولید
پیش نمایش صفحه اول مقاله
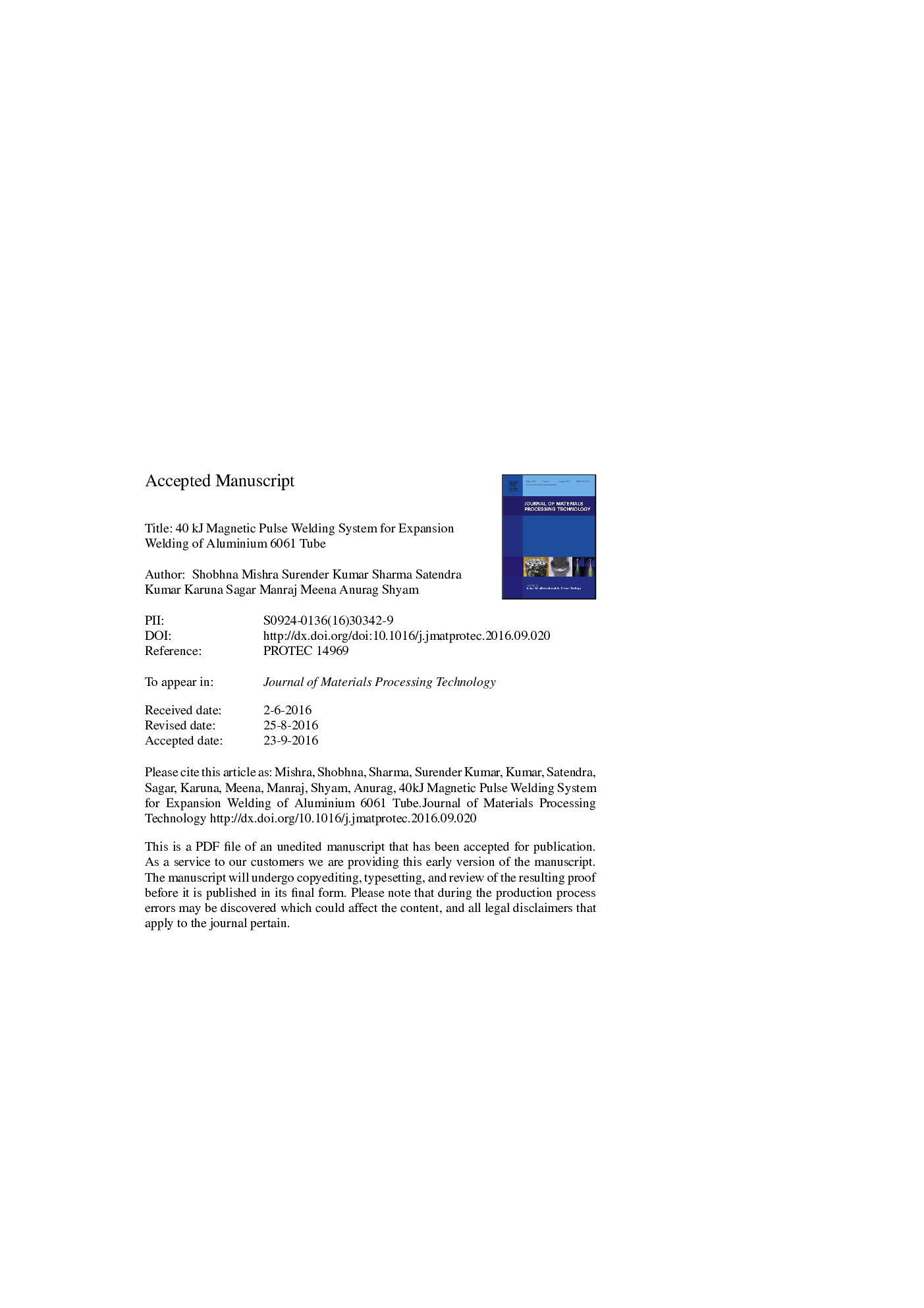
چکیده انگلیسی
The use of aluminium alloys has increased significantly in industries, so this trend has spurred the development of new joining methods for aluminium alloys. A 40 kJ Magnetic Pulse Welding (MPW) system was designed and developed to carry out the Electro-Magnetic (EM) expansion welding of aluminium 6061 alloy tube. The system consists of 15 kV, 356 μF capacitor bank, spark-gap switch and an EM expansion welding coil. The short circuit frequency of the MPW system is 20 kHz; it had delivered the maximum current of 166 kA, magnetic field of 31 T in the 1.5 μH coil and has achieved the maximum impact velocity of 660 m/s for 65 mm diameter, 1.5 mm thick tube. The EM expansion coils were designed and fabricated using circular and rectangular cross section copper wires. For the same discharge current, coils fabricated with rectangular cross section copper wires were found mechanically stronger and developed about 1.3 times higher fields than the coils fabricated of circular cross section copper wires. Simulation and experimental studies have been done to analyse the effect of factors like system frequency, peak current, magnetic field profile and geometry of work piece on the quality of weld obtained in the process. Expansion welding of Al 6061 tube of 25 mm to 65 mm diameter, 1.5 mm and 2 mm thickness and stand-off distance 2 mm to 3 mm was carried out. A stand-off distance of 2.5 mm was found to be the optimal value for a 65 mm diameter, 1.5 mm tube at a discharge current of 166 kA, which resulted into a good and strong metallurgical bond between the work pieces at the interface. Thicker tubes require comparatively more energy to deform significantly and to get accelerated to required velocity in comparison to thinner tubes. The characterization of the weld joint was done by drop, pull out, peel-off tests and microscopic image of the weld joint was also analysed to confirm the wavy morphology of the weld interface.
ناشر
Database: Elsevier - ScienceDirect (ساینس دایرکت)
Journal: Journal of Materials Processing Technology - Volume 240, February 2017, Pages 168-175
Journal: Journal of Materials Processing Technology - Volume 240, February 2017, Pages 168-175
نویسندگان
Shobhna Mishra, Surender Kumar Sharma, Satendra Kumar, Karuna Sagar, Manraj Meena, Anurag Shyam,