کد مقاله | کد نشریه | سال انتشار | مقاله انگلیسی | نسخه تمام متن |
---|---|---|---|---|
546803 | 871943 | 2014 | 10 صفحه PDF | دانلود رایگان |
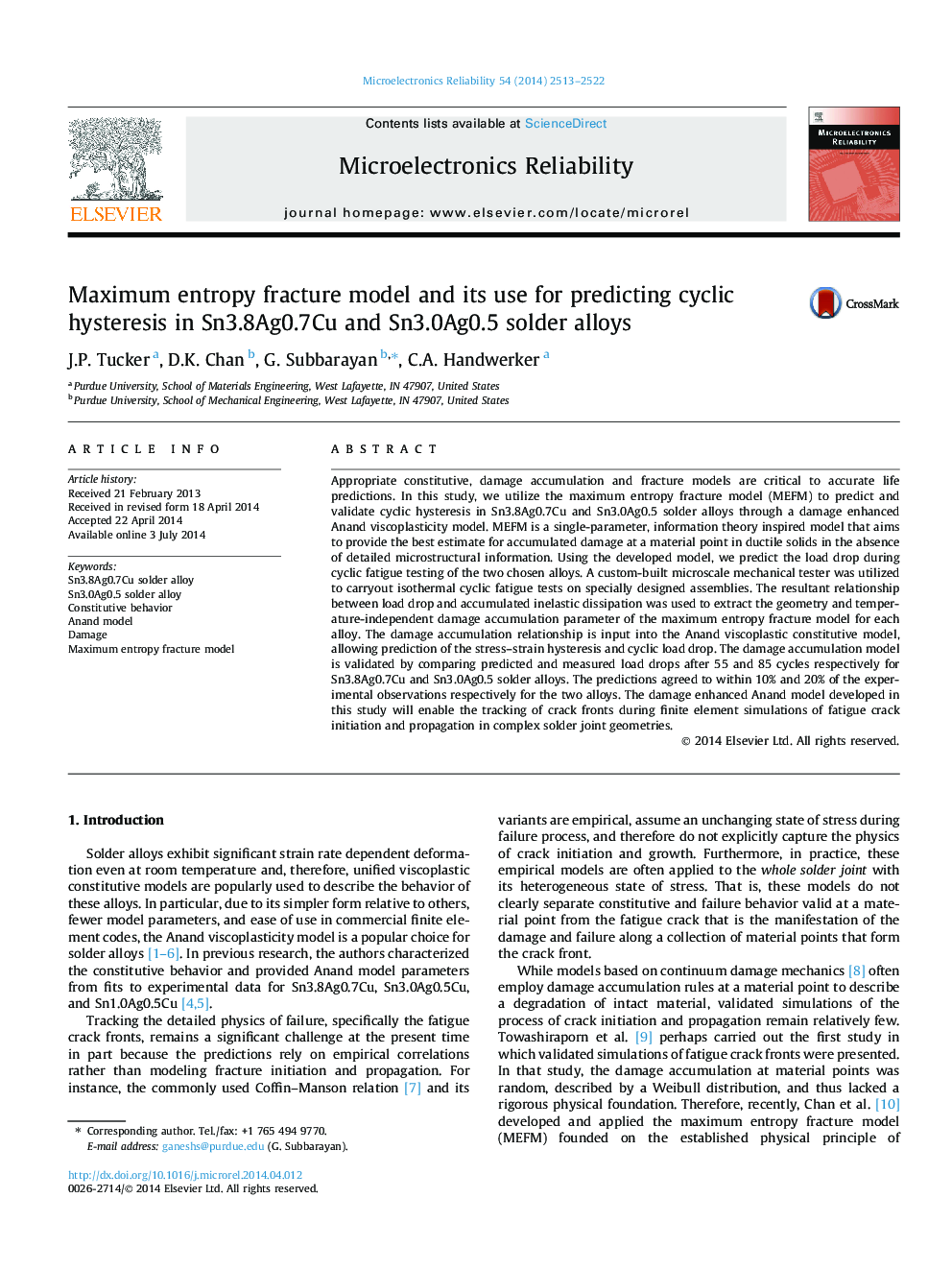
• A model for damage accumulation at a point in solder joints based on maximum entropy principle.
• Augmented Anand viscoplastic constitutive model with damage.
• Validated on Sn3.8Ag0.7Cu alloy and Sn3.0Ag0.5Cu alloy.
Appropriate constitutive, damage accumulation and fracture models are critical to accurate life predictions. In this study, we utilize the maximum entropy fracture model (MEFM) to predict and validate cyclic hysteresis in Sn3.8Ag0.7Cu and Sn3.0Ag0.5 solder alloys through a damage enhanced Anand viscoplasticity model. MEFM is a single-parameter, information theory inspired model that aims to provide the best estimate for accumulated damage at a material point in ductile solids in the absence of detailed microstructural information. Using the developed model, we predict the load drop during cyclic fatigue testing of the two chosen alloys. A custom-built microscale mechanical tester was utilized to carryout isothermal cyclic fatigue tests on specially designed assemblies. The resultant relationship between load drop and accumulated inelastic dissipation was used to extract the geometry and temperature-independent damage accumulation parameter of the maximum entropy fracture model for each alloy. The damage accumulation relationship is input into the Anand viscoplastic constitutive model, allowing prediction of the stress–strain hysteresis and cyclic load drop. The damage accumulation model is validated by comparing predicted and measured load drops after 55 and 85 cycles respectively for Sn3.8Ag0.7Cu and Sn3.0Ag0.5 solder alloys. The predictions agreed to within 10% and 20% of the experimental observations respectively for the two alloys. The damage enhanced Anand model developed in this study will enable the tracking of crack fronts during finite element simulations of fatigue crack initiation and propagation in complex solder joint geometries.
Journal: Microelectronics Reliability - Volume 54, Issue 11, November 2014, Pages 2513–2522