کد مقاله | کد نشریه | سال انتشار | مقاله انگلیسی | نسخه تمام متن |
---|---|---|---|---|
548951 | 872300 | 2015 | 7 صفحه PDF | دانلود رایگان |
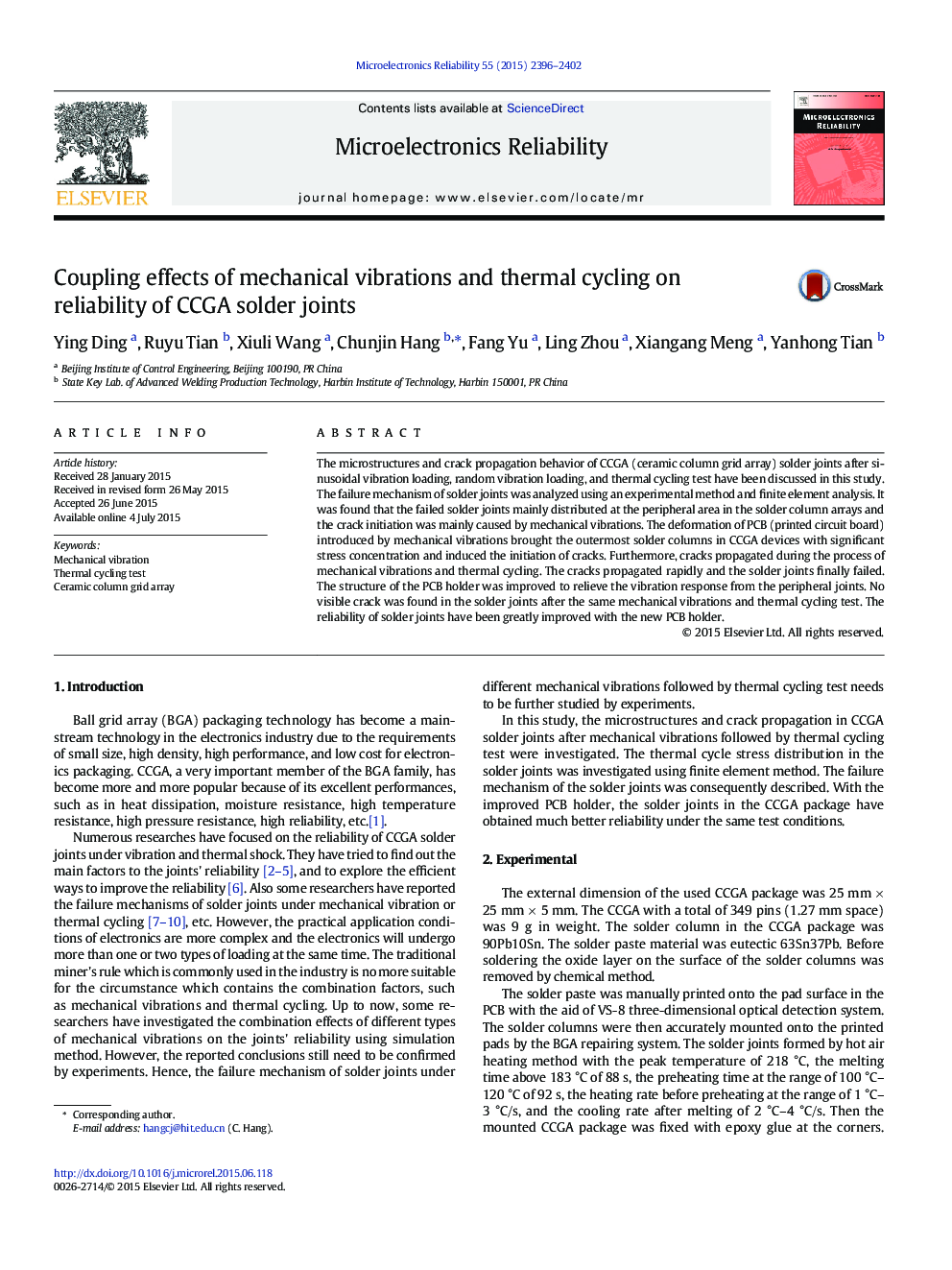
• Crack initiation was attributed to mechanical vibrations.
• Thermal stress would encourage crack propagation.
• The reinforced PCB holder is very helpful for vibration response relief.
The microstructures and crack propagation behavior of CCGA (ceramic column grid array) solder joints after sinusoidal vibration loading, random vibration loading, and thermal cycling test have been discussed in this study. The failure mechanism of solder joints was analyzed using an experimental method and finite element analysis. It was found that the failed solder joints mainly distributed at the peripheral area in the solder column arrays and the crack initiation was mainly caused by mechanical vibrations. The deformation of PCB (printed circuit board) introduced by mechanical vibrations brought the outermost solder columns in CCGA devices with significant stress concentration and induced the initiation of cracks. Furthermore, cracks propagated during the process of mechanical vibrations and thermal cycling. The cracks propagated rapidly and the solder joints finally failed. The structure of the PCB holder was improved to relieve the vibration response from the peripheral joints. No visible crack was found in the solder joints after the same mechanical vibrations and thermal cycling test. The reliability of solder joints have been greatly improved with the new PCB holder.
Journal: Microelectronics Reliability - Volume 55, Issue 11, November 2015, Pages 2396–2402