کد مقاله | کد نشریه | سال انتشار | مقاله انگلیسی | نسخه تمام متن |
---|---|---|---|---|
764299 | 1462906 | 2012 | 8 صفحه PDF | دانلود رایگان |
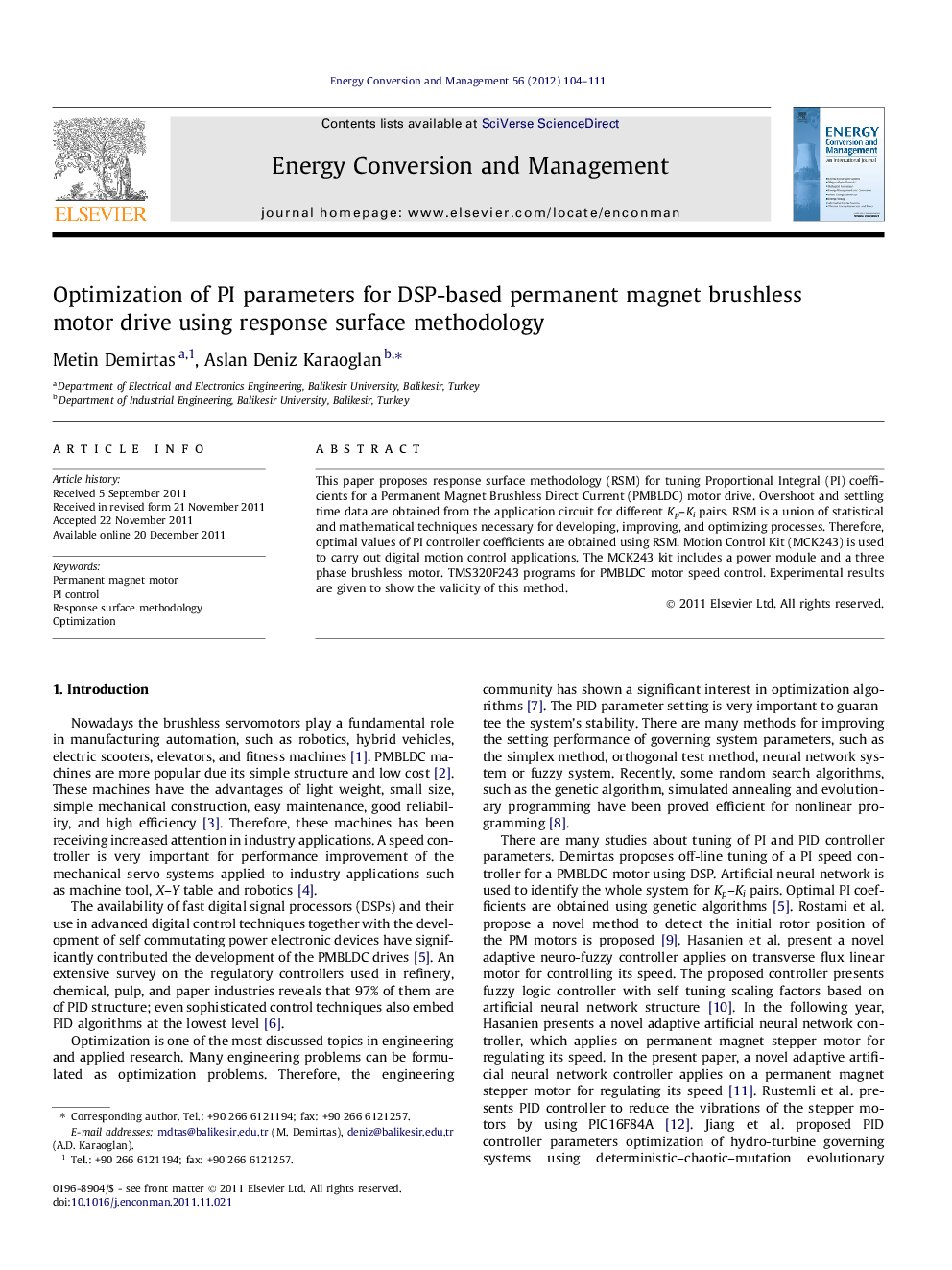
This paper proposes response surface methodology (RSM) for tuning Proportional Integral (PI) coefficients for a Permanent Magnet Brushless Direct Current (PMBLDC) motor drive. Overshoot and settling time data are obtained from the application circuit for different Kp–Ki pairs. RSM is a union of statistical and mathematical techniques necessary for developing, improving, and optimizing processes. Therefore, optimal values of PI controller coefficients are obtained using RSM. Motion Control Kit (MCK243) is used to carry out digital motion control applications. The MCK243 kit includes a power module and a three phase brushless motor. TMS320F243 programs for PMBLDC motor speed control. Experimental results are given to show the validity of this method.
► We used response surface methodology (RSM) for optimization of PI parameters.
► When we reviewed the literature, we observed that RSM is not used for this purpose.
► The originality of this work is that applying RSM to the electrical machine drives.
► RSM provided the mathematical relationships between M0, Ts, and process parameters Kp, Ki.
► We determined the optimal combinations of input parameters with only 13 experiments.
Journal: Energy Conversion and Management - Volume 56, April 2012, Pages 104–111