کد مقاله | کد نشریه | سال انتشار | مقاله انگلیسی | نسخه تمام متن |
---|---|---|---|---|
765874 | 1462901 | 2012 | 8 صفحه PDF | دانلود رایگان |
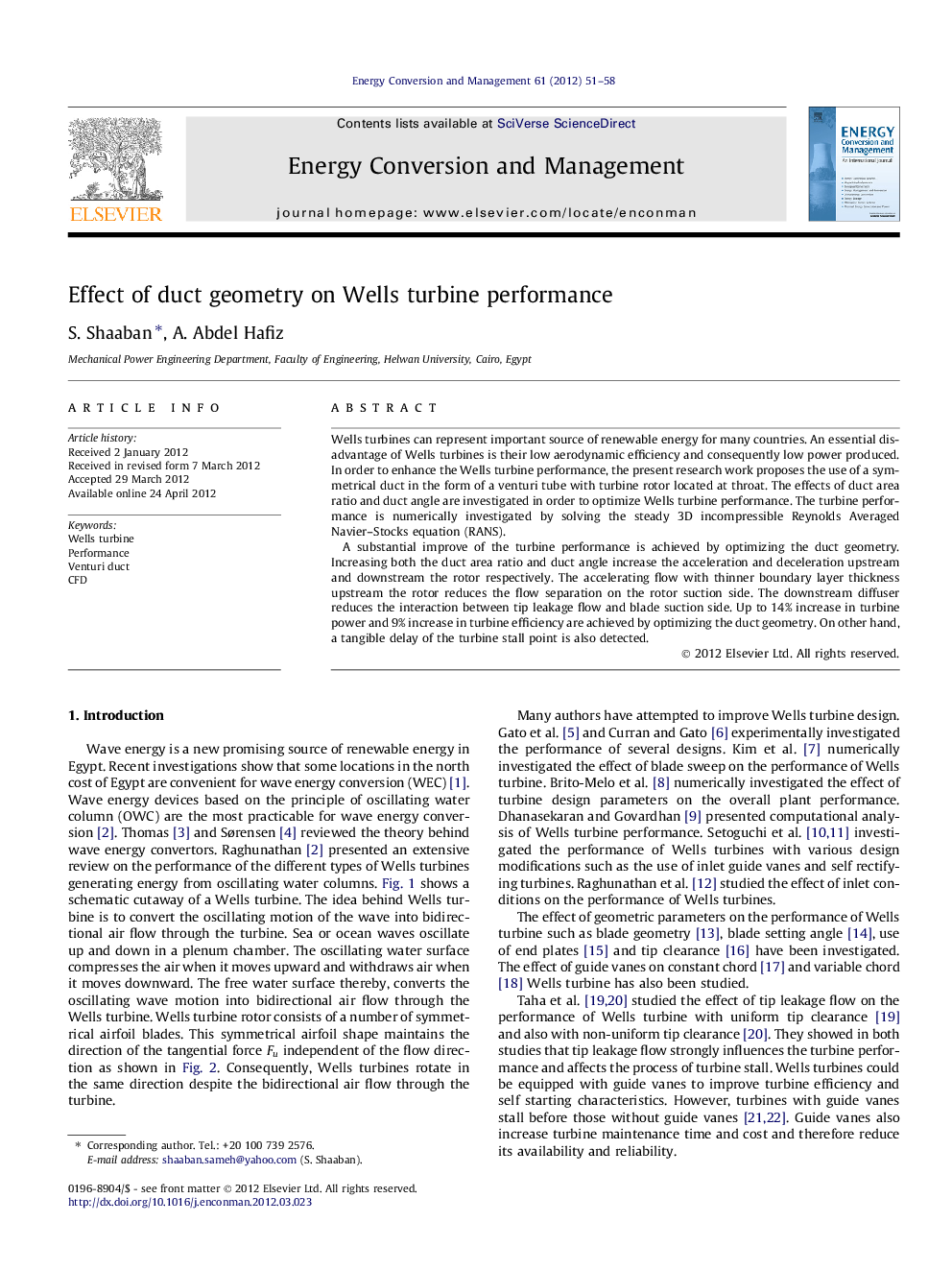
Wells turbines can represent important source of renewable energy for many countries. An essential disadvantage of Wells turbines is their low aerodynamic efficiency and consequently low power produced. In order to enhance the Wells turbine performance, the present research work proposes the use of a symmetrical duct in the form of a venturi tube with turbine rotor located at throat. The effects of duct area ratio and duct angle are investigated in order to optimize Wells turbine performance. The turbine performance is numerically investigated by solving the steady 3D incompressible Reynolds Averaged Navier–Stocks equation (RANS).A substantial improve of the turbine performance is achieved by optimizing the duct geometry. Increasing both the duct area ratio and duct angle increase the acceleration and deceleration upstream and downstream the rotor respectively. The accelerating flow with thinner boundary layer thickness upstream the rotor reduces the flow separation on the rotor suction side. The downstream diffuser reduces the interaction between tip leakage flow and blade suction side. Up to 14% increase in turbine power and 9% increase in turbine efficiency are achieved by optimizing the duct geometry. On other hand, a tangible delay of the turbine stall point is also detected.
► A Wells turbine duct design in the form of venturi duct is proposed and investigated.
► Optimum duct geometry is identified.
► Up to 14% increase of the turbine power can be achieved using the optimized duct geometry.
► Up to 9% improve of the turbine efficiency is attained by optimizing the turbine duct geometry.
► The optimized duct geometry results in tangible delay of the turbine stalling point.
Journal: Energy Conversion and Management - Volume 61, September 2012, Pages 51–58