کد مقاله | کد نشریه | سال انتشار | مقاله انگلیسی | نسخه تمام متن |
---|---|---|---|---|
780561 | 1464539 | 2011 | 10 صفحه PDF | دانلود رایگان |
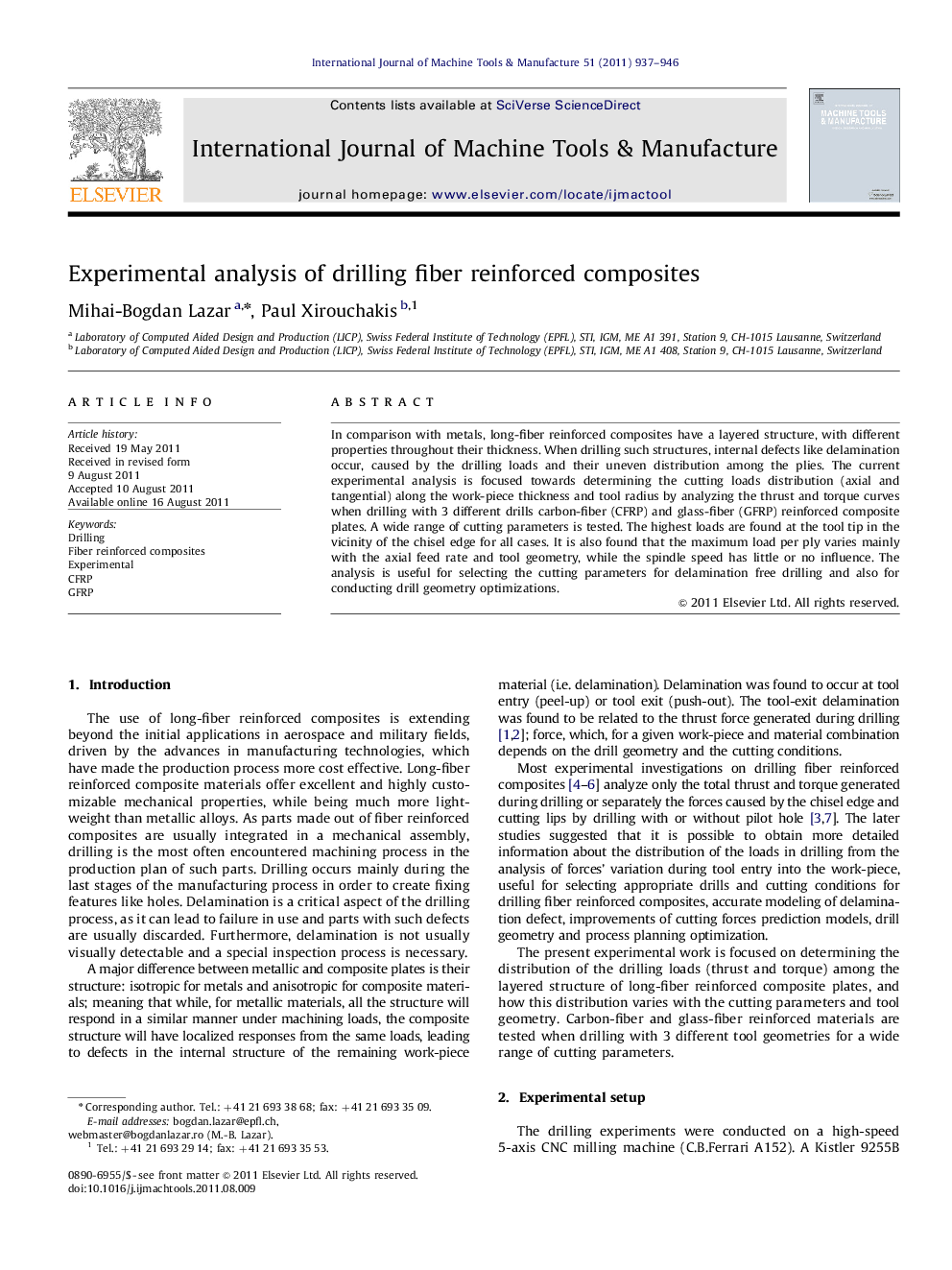
In comparison with metals, long-fiber reinforced composites have a layered structure, with different properties throughout their thickness. When drilling such structures, internal defects like delamination occur, caused by the drilling loads and their uneven distribution among the plies. The current experimental analysis is focused towards determining the cutting loads distribution (axial and tangential) along the work-piece thickness and tool radius by analyzing the thrust and torque curves when drilling with 3 different drills carbon-fiber (CFRP) and glass-fiber (GFRP) reinforced composite plates. A wide range of cutting parameters is tested. The highest loads are found at the tool tip in the vicinity of the chisel edge for all cases. It is also found that the maximum load per ply varies mainly with the axial feed rate and tool geometry, while the spindle speed has little or no influence. The analysis is useful for selecting the cutting parameters for delamination free drilling and also for conducting drill geometry optimizations.
► A more comprehensive experimental analysis of the drilling process of fiber reinforced laminates.
► Cutting forces distribution along drill radius and among work-piece’s plies is obtained.
► 3 different tool geometries, 2 different composite materials and a wide range of cutting parameters were tested.
► Influences of the cutting parameters and tool geometries over the maximum load per ply are noted
Journal: International Journal of Machine Tools and Manufacture - Volume 51, Issue 12, December 2011, Pages 937–946