کد مقاله | کد نشریه | سال انتشار | مقاله انگلیسی | نسخه تمام متن |
---|---|---|---|---|
780640 | 1464484 | 2016 | 11 صفحه PDF | دانلود رایگان |
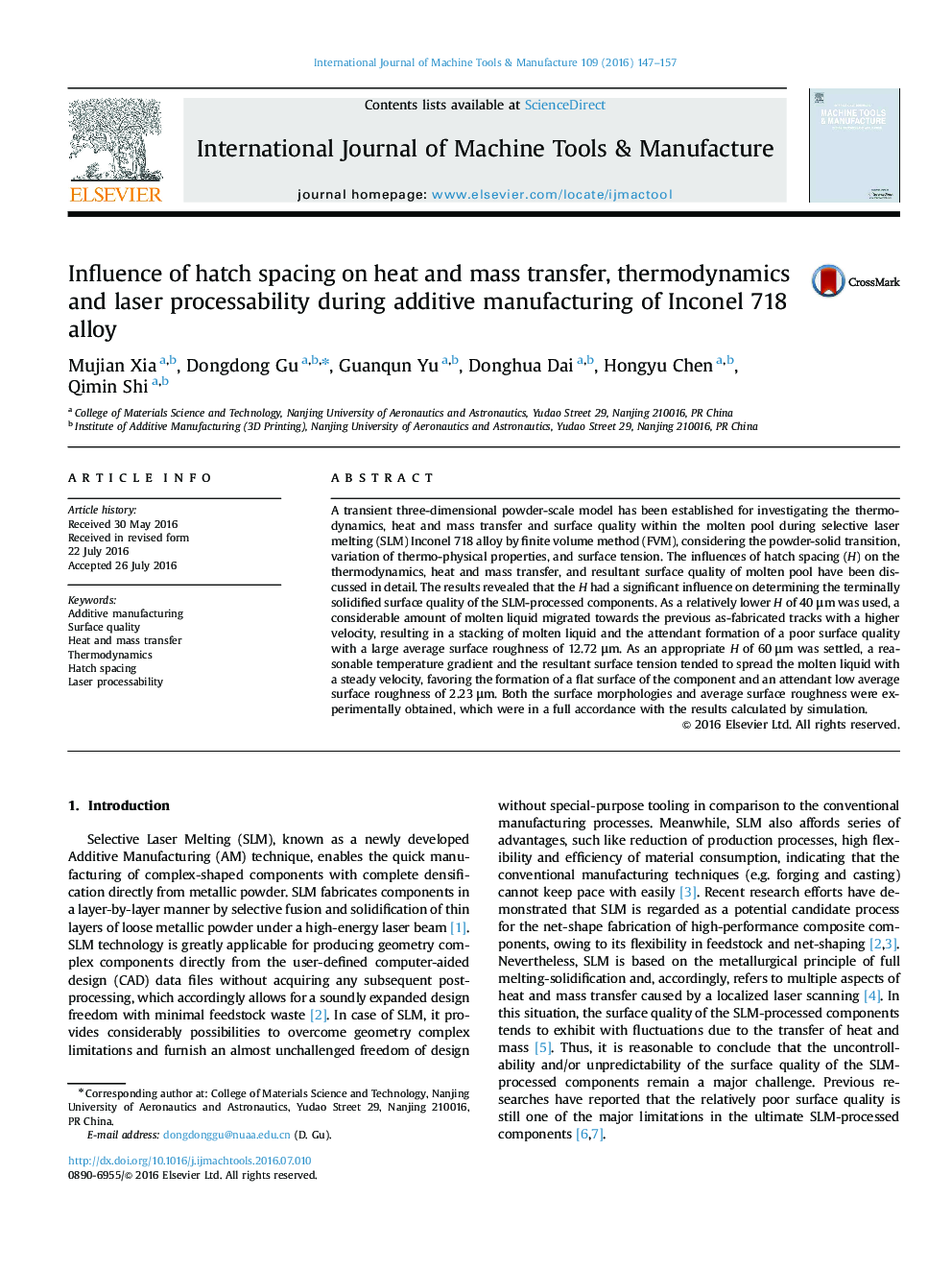
• A novel powder-scale model was developed to investigate the evolution of surface quality during additive manufacturing of Inconel 718 alloy.
• The thermodynamic behavior within the molten pool was analyzed.
• The evolution of surface quality under variable hatch spacing was evaluated.
• The corresponding experimental results were in a full accordance with those obtained from simulations.
A transient three-dimensional powder-scale model has been established for investigating the thermodynamics, heat and mass transfer and surface quality within the molten pool during selective laser melting (SLM) Inconel 718 alloy by finite volume method (FVM), considering the powder-solid transition, variation of thermo-physical properties, and surface tension. The influences of hatch spacing (H) on the thermodynamics, heat and mass transfer, and resultant surface quality of molten pool have been discussed in detail. The results revealed that the H had a significant influence on determining the terminally solidified surface quality of the SLM-processed components. As a relatively lower H of 40 μm was used, a considerable amount of molten liquid migrated towards the previous as-fabricated tracks with a higher velocity, resulting in a stacking of molten liquid and the attendant formation of a poor surface quality with a large average surface roughness of 12.72 μm. As an appropriate H of 60 μm was settled, a reasonable temperature gradient and the resultant surface tension tended to spread the molten liquid with a steady velocity, favoring the formation of a flat surface of the component and an attendant low average surface roughness of 2.23 μm. Both the surface morphologies and average surface roughness were experimentally obtained, which were in a full accordance with the results calculated by simulation.
Journal: International Journal of Machine Tools and Manufacture - Volume 109, October 2016, Pages 147–157