کد مقاله | کد نشریه | سال انتشار | مقاله انگلیسی | نسخه تمام متن |
---|---|---|---|---|
780710 | 1464550 | 2010 | 18 صفحه PDF | دانلود رایگان |
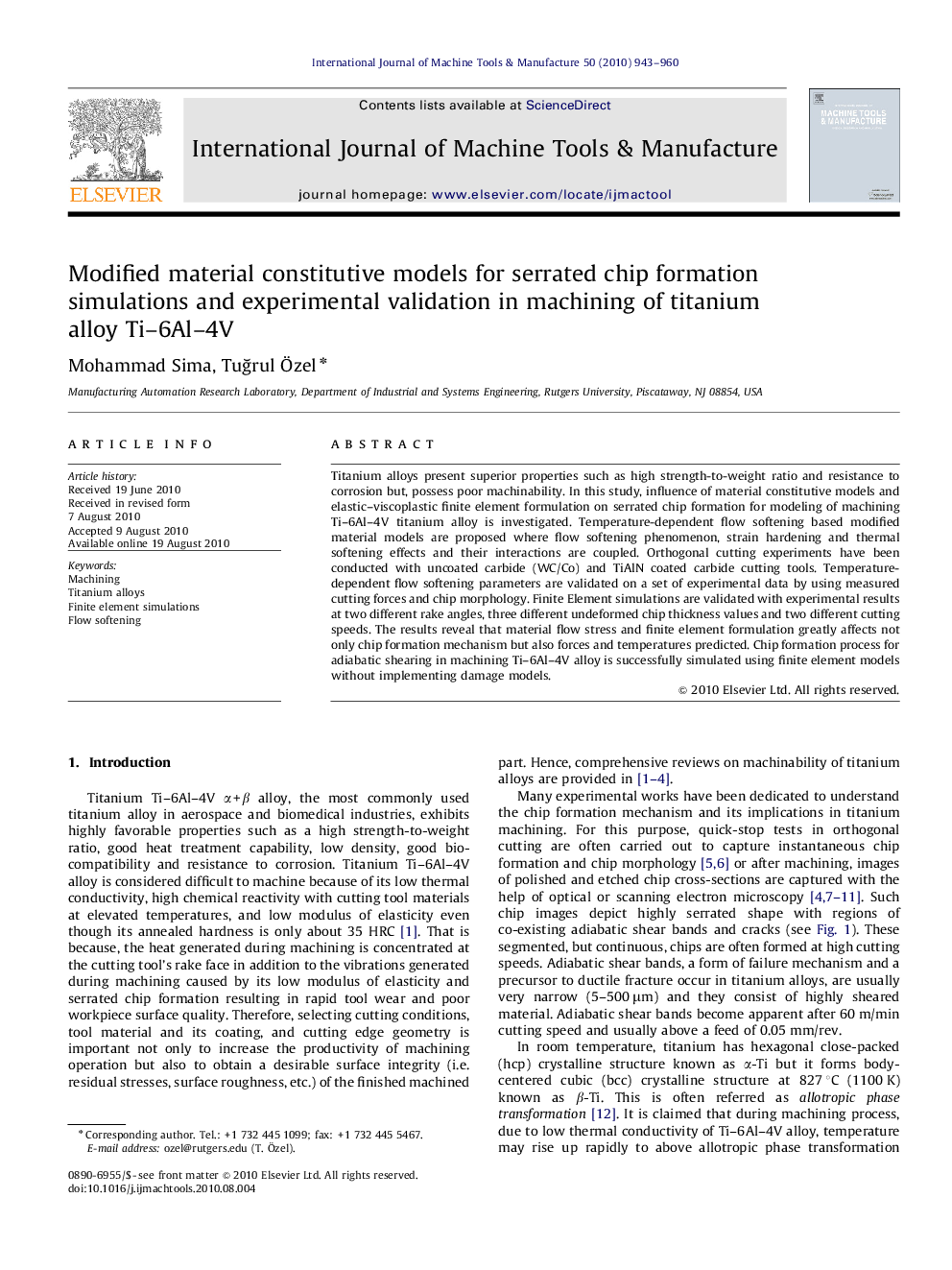
Titanium alloys present superior properties such as high strength-to-weight ratio and resistance to corrosion but, possess poor machinability. In this study, influence of material constitutive models and elastic–viscoplastic finite element formulation on serrated chip formation for modeling of machining Ti–6Al–4V titanium alloy is investigated. Temperature-dependent flow softening based modified material models are proposed where flow softening phenomenon, strain hardening and thermal softening effects and their interactions are coupled. Orthogonal cutting experiments have been conducted with uncoated carbide (WC/Co) and TiAlN coated carbide cutting tools. Temperature-dependent flow softening parameters are validated on a set of experimental data by using measured cutting forces and chip morphology. Finite Element simulations are validated with experimental results at two different rake angles, three different undeformed chip thickness values and two different cutting speeds. The results reveal that material flow stress and finite element formulation greatly affects not only chip formation mechanism but also forces and temperatures predicted. Chip formation process for adiabatic shearing in machining Ti–6Al–4V alloy is successfully simulated using finite element models without implementing damage models.
Journal: International Journal of Machine Tools and Manufacture - Volume 50, Issue 11, November 2010, Pages 943–960