کد مقاله | کد نشریه | سال انتشار | مقاله انگلیسی | نسخه تمام متن |
---|---|---|---|---|
783618 | 1465001 | 2014 | 7 صفحه PDF | دانلود رایگان |
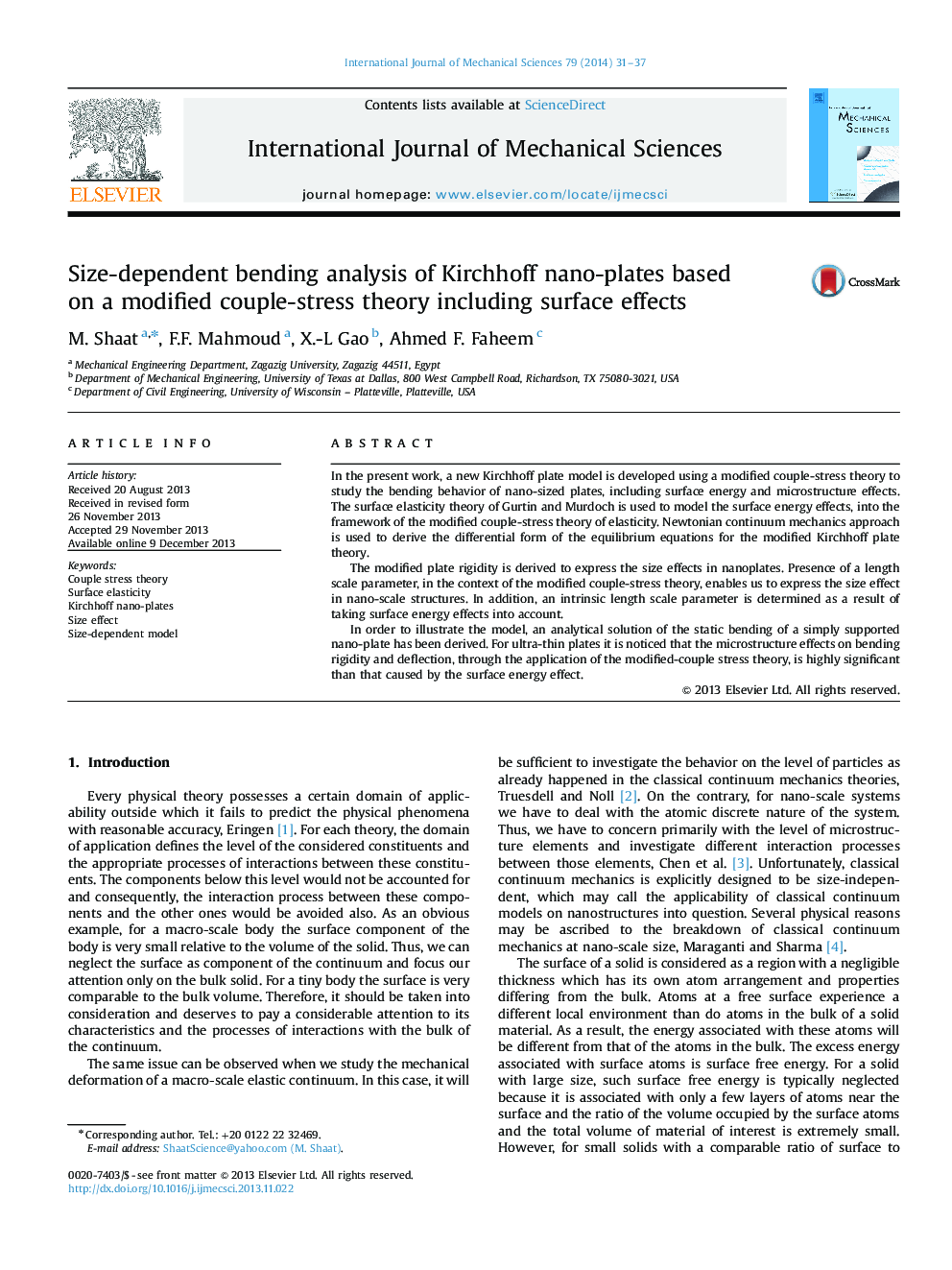
• A new Kirchhoff nanoplate model is developed using a modified couple-stress theory, including surface energy and microstructure effects.
• The surface elasticity theory is used to model the surface effects, into the framework of the modified couple-stress theory.
• Newtonian continuum mechanics approach is used to derive the differential governing equations for the modified Kirchhoff plate theory.
• Length scale parameters, in the context of the couple-stress and surface elasticity, are derived expressing size effects in structures.
• An analytical solution of the static bending of a simply supported nanoplate has been derived.
In the present work, a new Kirchhoff plate model is developed using a modified couple-stress theory to study the bending behavior of nano-sized plates, including surface energy and microstructure effects. The surface elasticity theory of Gurtin and Murdoch is used to model the surface energy effects, into the framework of the modified couple-stress theory of elasticity. Newtonian continuum mechanics approach is used to derive the differential form of the equilibrium equations for the modified Kirchhoff plate theory.The modified plate rigidity is derived to express the size effects in nanoplates. Presence of a length scale parameter, in the context of the modified couple-stress theory, enables us to express the size effect in nano-scale structures. In addition, an intrinsic length scale parameter is determined as a result of taking surface energy effects into account.In order to illustrate the model, an analytical solution of the static bending of a simply supported nano-plate has been derived. For ultra-thin plates it is noticed that the microstructure effects on bending rigidity and deflection, through the application of the modified-couple stress theory, is highly significant than that caused by the surface energy effect.
Journal: International Journal of Mechanical Sciences - Volume 79, February 2014, Pages 31–37