کد مقاله | کد نشریه | سال انتشار | مقاله انگلیسی | نسخه تمام متن |
---|---|---|---|---|
802096 | 904349 | 2011 | 12 صفحه PDF | دانلود رایگان |
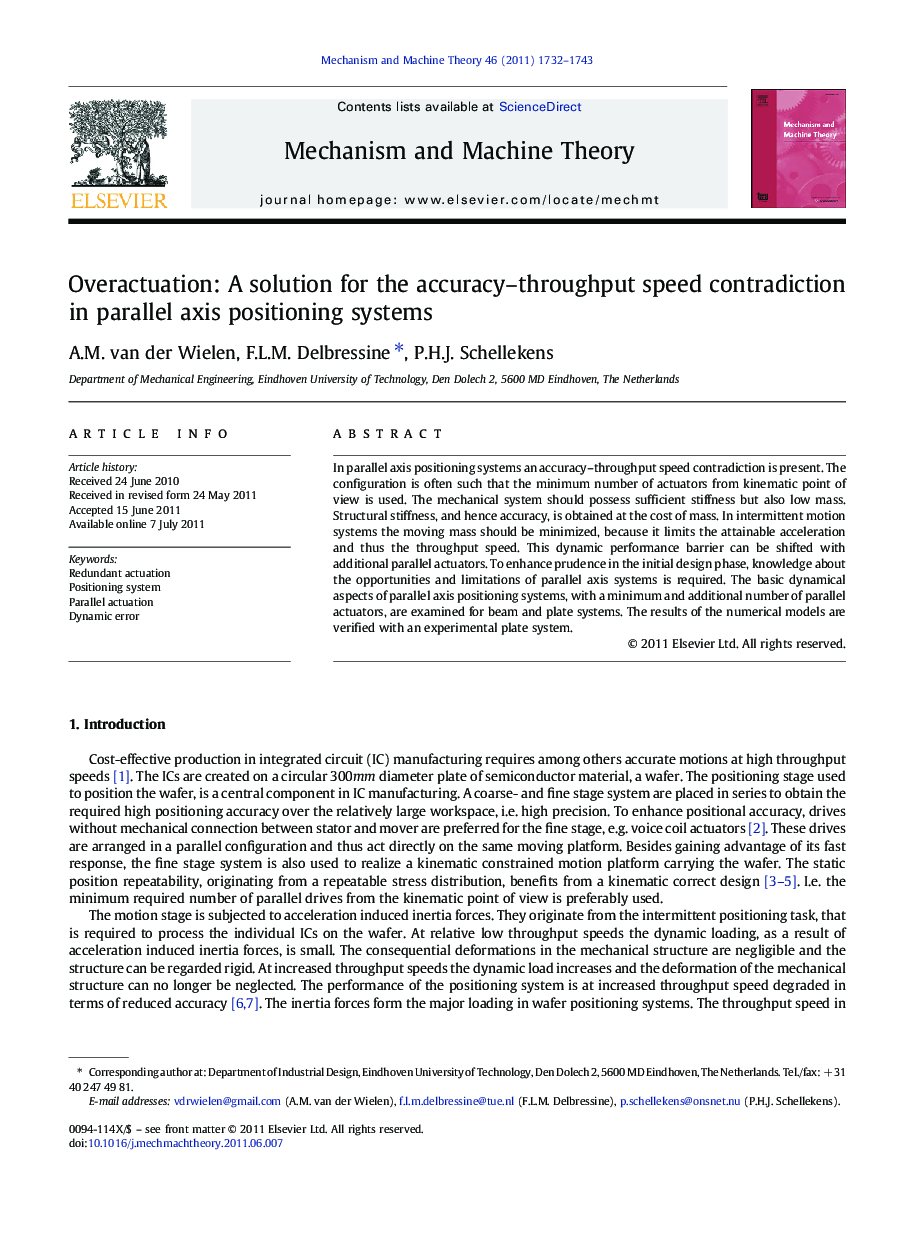
In parallel axis positioning systems an accuracy–throughput speed contradiction is present. The configuration is often such that the minimum number of actuators from kinematic point of view is used. The mechanical system should possess sufficient stiffness but also low mass. Structural stiffness, and hence accuracy, is obtained at the cost of mass. In intermittent motion systems the moving mass should be minimized, because it limits the attainable acceleration and thus the throughput speed. This dynamic performance barrier can be shifted with additional parallel actuators. To enhance prudence in the initial design phase, knowledge about the opportunities and limitations of parallel axis systems is required. The basic dynamical aspects of parallel axis positioning systems, with a minimum and additional number of parallel actuators, are examined for beam and plate systems. The results of the numerical models are verified with an experimental plate system.
► Better understanding of the dynamics of parallel axis positioning systems.
► Reduced residual vibration amplitude after a positioning task and a reduced time between consecutive positioning tasks.
► The current accuracy–throughput speed limitation can be shifted economically.
Journal: Mechanism and Machine Theory - Volume 46, Issue 11, November 2011, Pages 1732–1743