کد مقاله | کد نشریه | سال انتشار | مقاله انگلیسی | نسخه تمام متن |
---|---|---|---|---|
804543 | 904958 | 2013 | 10 صفحه PDF | دانلود رایگان |
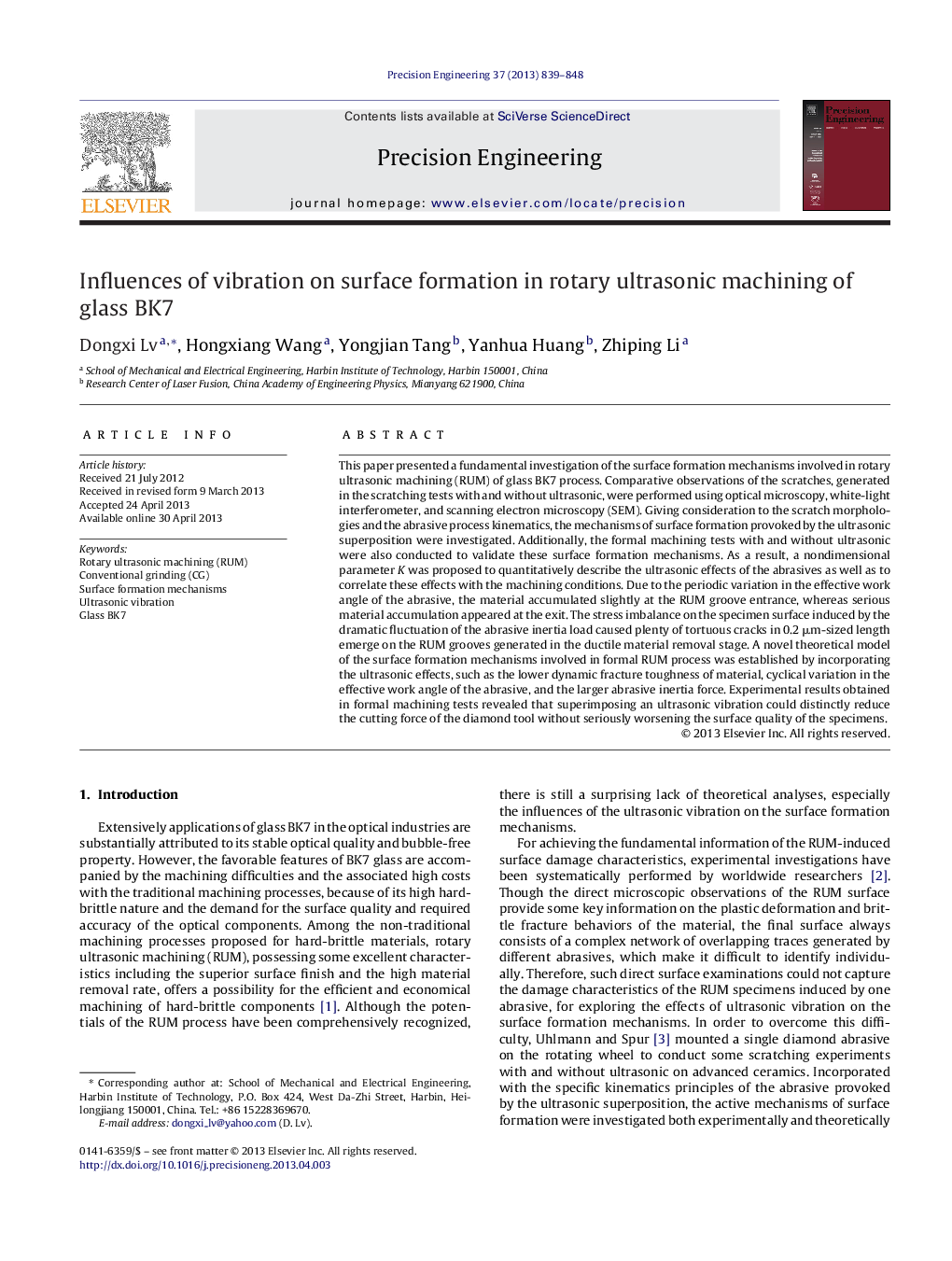
• A parameter K was defined to describe the ultrasonic effects of the abrasive.
• Periodic variation of the abrasive effective work angle affected the surface formation process.
• Tortuous cracks were distinguished on RUM grooves produced in ductile material removal stage.
• We developed a fresh model of surface formation mechanisms.
• The propagations of the incipient cracks led to significantly reduction of the cutting force.
This paper presented a fundamental investigation of the surface formation mechanisms involved in rotary ultrasonic machining (RUM) of glass BK7 process. Comparative observations of the scratches, generated in the scratching tests with and without ultrasonic, were performed using optical microscopy, white-light interferometer, and scanning electron microscopy (SEM). Giving consideration to the scratch morphologies and the abrasive process kinematics, the mechanisms of surface formation provoked by the ultrasonic superposition were investigated. Additionally, the formal machining tests with and without ultrasonic were also conducted to validate these surface formation mechanisms. As a result, a nondimensional parameter K was proposed to quantitatively describe the ultrasonic effects of the abrasives as well as to correlate these effects with the machining conditions. Due to the periodic variation in the effective work angle of the abrasive, the material accumulated slightly at the RUM groove entrance, whereas serious material accumulation appeared at the exit. The stress imbalance on the specimen surface induced by the dramatic fluctuation of the abrasive inertia load caused plenty of tortuous cracks in 0.2 μm-sized length emerge on the RUM grooves generated in the ductile material removal stage. A novel theoretical model of the surface formation mechanisms involved in formal RUM process was established by incorporating the ultrasonic effects, such as the lower dynamic fracture toughness of material, cyclical variation in the effective work angle of the abrasive, and the larger abrasive inertia force. Experimental results obtained in formal machining tests revealed that superimposing an ultrasonic vibration could distinctly reduce the cutting force of the diamond tool without seriously worsening the surface quality of the specimens.
Journal: Precision Engineering - Volume 37, Issue 4, October 2013, Pages 839–848