کد مقاله | کد نشریه | سال انتشار | مقاله انگلیسی | نسخه تمام متن |
---|---|---|---|---|
827858 | 1470276 | 2016 | 8 صفحه PDF | دانلود رایگان |
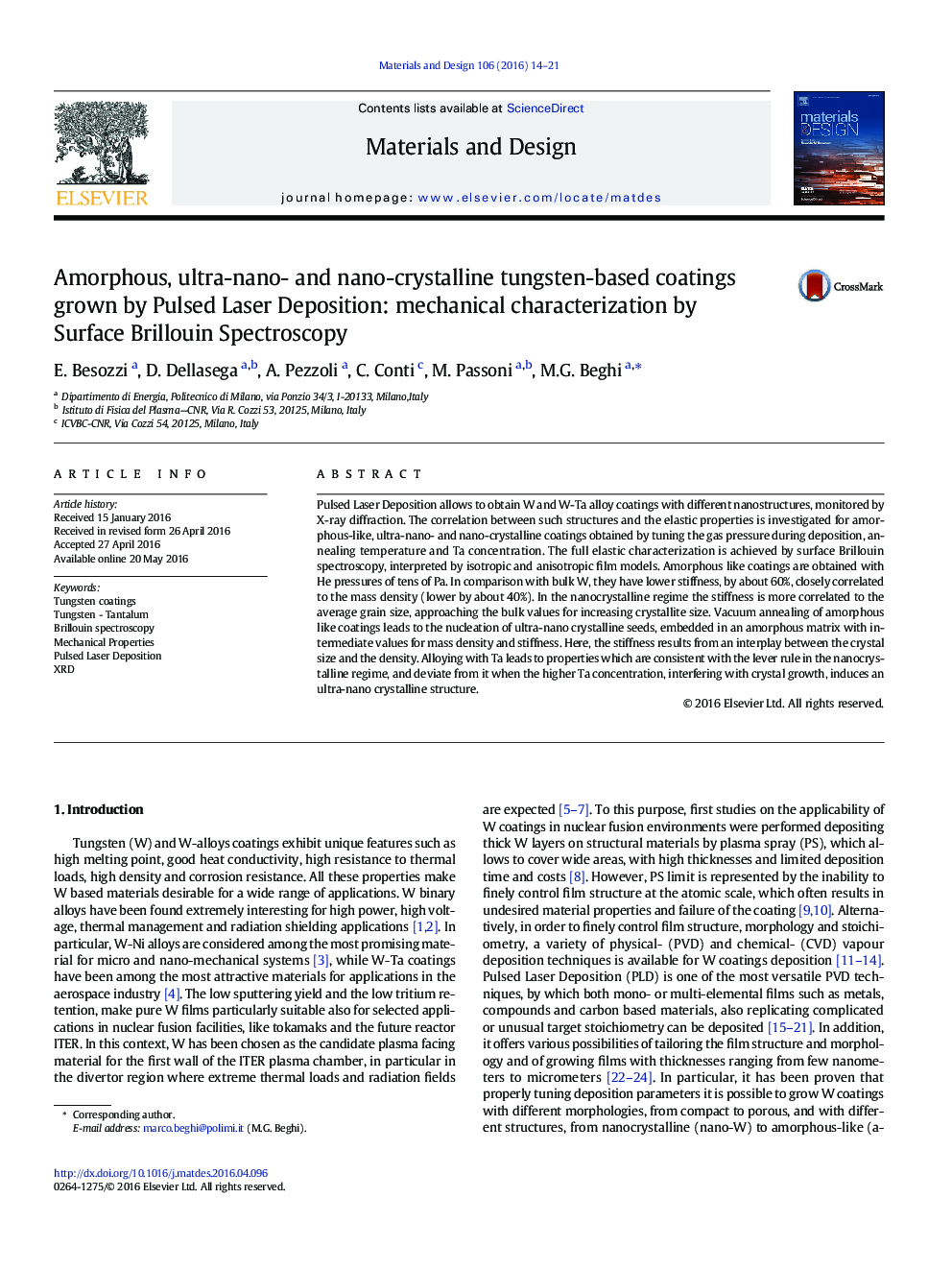
• Pulsed Laser Deposition of W coatings allows to tailor the structure at the nanoscale.
• Elastic properties are accessible predicting by isotropic and anisotropic models the dispersion relations measured by Brillouin spectroscopy.
• Amorphous-like structures have lower density and, upon annealing, evolve at temperatures of one half the W recrystallization one.
• Nanocrystalline structures have higher density and stiffness correlated to crystallites size.
• Significant Ta concentrations hinder crystallites growth promoting local ductility.
Pulsed Laser Deposition allows to obtain W and W-Ta alloy coatings with different nanostructures, monitored by X-ray diffraction. The correlation between such structures and the elastic properties is investigated for amorphous-like, ultra-nano- and nano-crystalline coatings obtained by tuning the gas pressure during deposition, annealing temperature and Ta concentration. The full elastic characterization is achieved by surface Brillouin spectroscopy, interpreted by isotropic and anisotropic film models. Amorphous like coatings are obtained with He pressures of tens of Pa. In comparison with bulk W, they have lower stiffness, by about 60%, closely correlated to the mass density (lower by about 40%). In the nanocrystalline regime the stiffness is more correlated to the average grain size, approaching the bulk values for increasing crystallite size. Vacuum annealing of amorphous like coatings leads to the nucleation of ultra-nano crystalline seeds, embedded in an amorphous matrix with intermediate values for mass density and stiffness. Here, the stiffness results from an interplay between the crystal size and the density. Alloying with Ta leads to properties which are consistent with the lever rule in the nanocrystalline regime, and deviate from it when the higher Ta concentration, interfering with crystal growth, induces an ultra-nano crystalline structure.
Figure optionsDownload as PowerPoint slide
Journal: Materials & Design - Volume 106, 15 September 2016, Pages 14–21