کد مقاله | کد نشریه | سال انتشار | مقاله انگلیسی | نسخه تمام متن |
---|---|---|---|---|
830142 | 1470351 | 2013 | 12 صفحه PDF | دانلود رایگان |
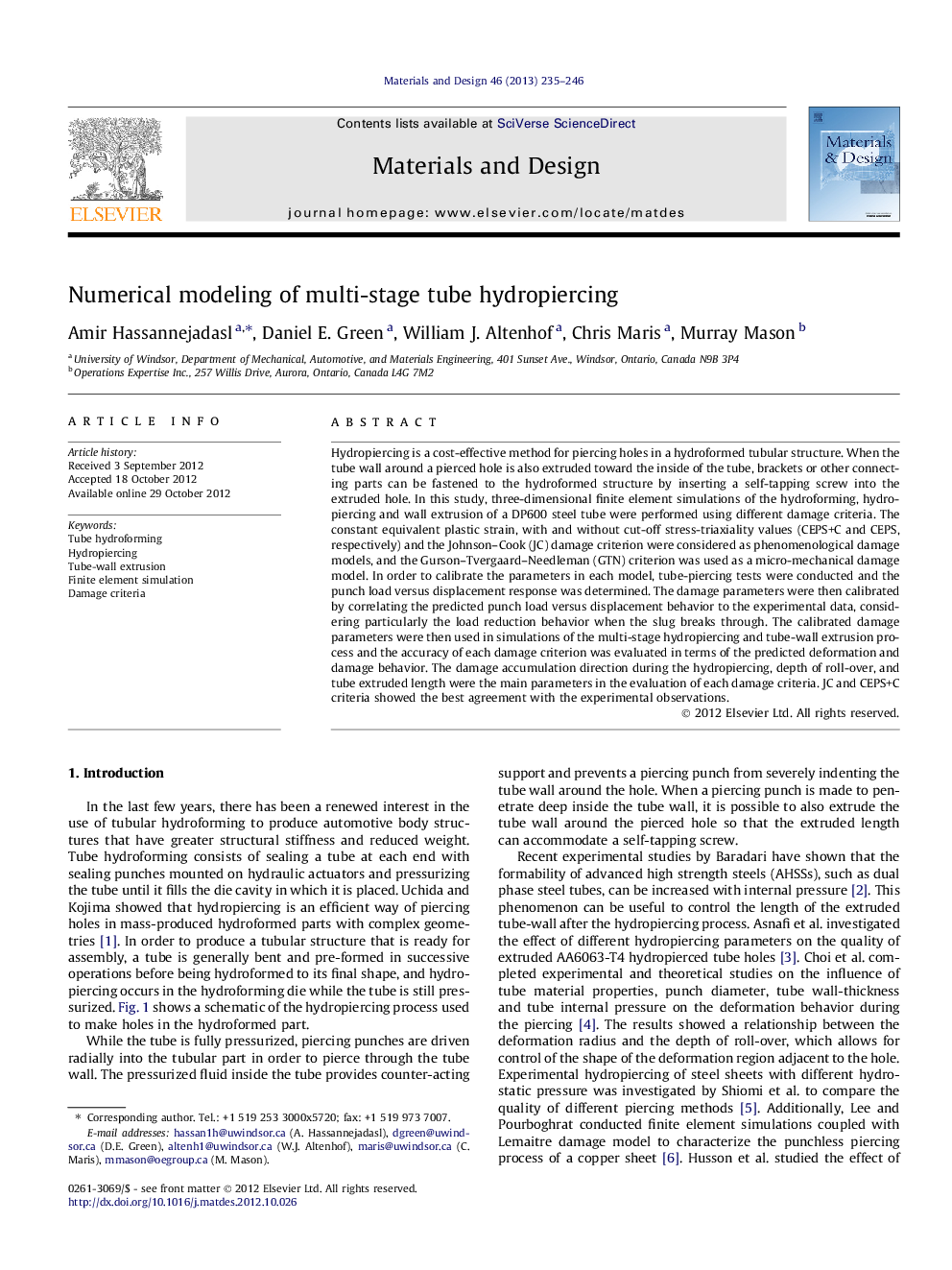
Hydropiercing is a cost-effective method for piercing holes in a hydroformed tubular structure. When the tube wall around a pierced hole is also extruded toward the inside of the tube, brackets or other connecting parts can be fastened to the hydroformed structure by inserting a self-tapping screw into the extruded hole. In this study, three-dimensional finite element simulations of the hydroforming, hydropiercing and wall extrusion of a DP600 steel tube were performed using different damage criteria. The constant equivalent plastic strain, with and without cut-off stress-triaxiality values (CEPS+C and CEPS, respectively) and the Johnson–Cook (JC) damage criterion were considered as phenomenological damage models, and the Gurson–Tvergaard–Needleman (GTN) criterion was used as a micro-mechanical damage model. In order to calibrate the parameters in each model, tube-piercing tests were conducted and the punch load versus displacement response was determined. The damage parameters were then calibrated by correlating the predicted punch load versus displacement behavior to the experimental data, considering particularly the load reduction behavior when the slug breaks through. The calibrated damage parameters were then used in simulations of the multi-stage hydropiercing and tube-wall extrusion process and the accuracy of each damage criterion was evaluated in terms of the predicted deformation and damage behavior. The damage accumulation direction during the hydropiercing, depth of roll-over, and tube extruded length were the main parameters in the evaluation of each damage criteria. JC and CEPS+C criteria showed the best agreement with the experimental observations.
Figure optionsDownload as PowerPoint slideHighlights
► Finite element simulations of a multi-stage hydropiercing were performed.
► Damage parameters were calibrated based on the experimental punch load-displacement.
► Damage accumulation direction, roll-over depth, and extruded length were evaluated.
► CEPS+C and JC damage models predicted the correct material damage behaviour.
Journal: Materials & Design - Volume 46, April 2013, Pages 235–246