کد مقاله | کد نشریه | سال انتشار | مقاله انگلیسی | نسخه تمام متن |
---|---|---|---|---|
858037 | 1470745 | 2014 | 6 صفحه PDF | دانلود رایگان |
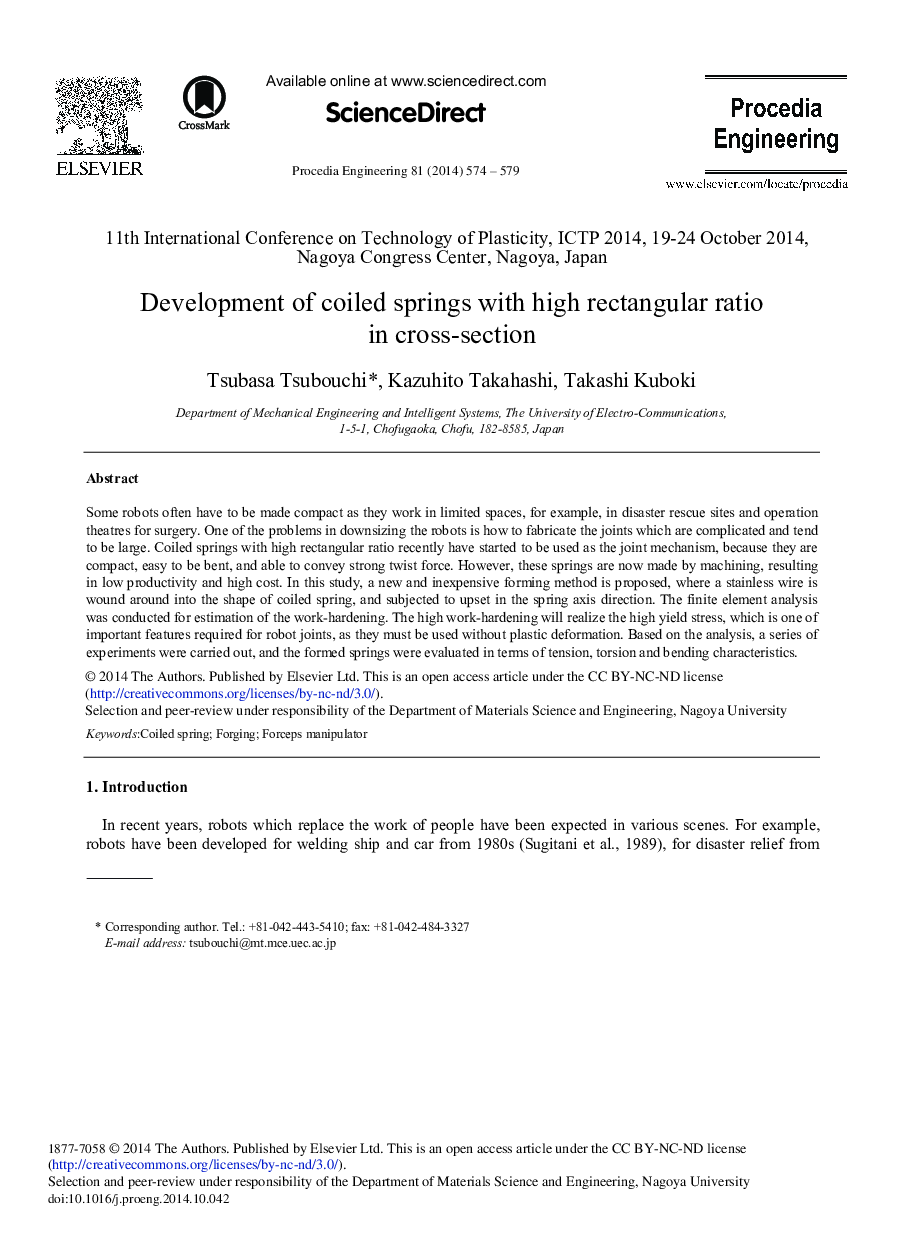
Some robots often have to be made compact as they work in limited spaces, for example, in disaster rescue sites and operation theatres for surgery. One of the problems in downsizing the robots is how to fabricate the joints which are complicated and tend to be large. Coiled springs with high rectangular ratio recently have started to be used as the joint mechanism, because they are compact, easy to be bent, and able to convey strong twist force. However, these springs are now made by machining, resulting in low productivity and high cost. In this study, a new and inexpensive forming method is proposed, where a stainless wire is wound around into the shape of coiled spring, and subjected to upset in the spring axis direction. The finite element analysis was conducted for estimation of the work-hardening. The high work-hardening will realize the high yield stress, which is one of important features required for robot joints, as they must be used without plastic deformation. Based on the analysis, a series of experiments were carried out, and the formed springs were evaluated in terms of tension, torsion and bending characteristics.
Journal: Procedia Engineering - Volume 81, 2014, Pages 574-579