کد مقاله | کد نشریه | سال انتشار | مقاله انگلیسی | نسخه تمام متن |
---|---|---|---|---|
864683 | 909628 | 2010 | 8 صفحه PDF | دانلود رایگان |
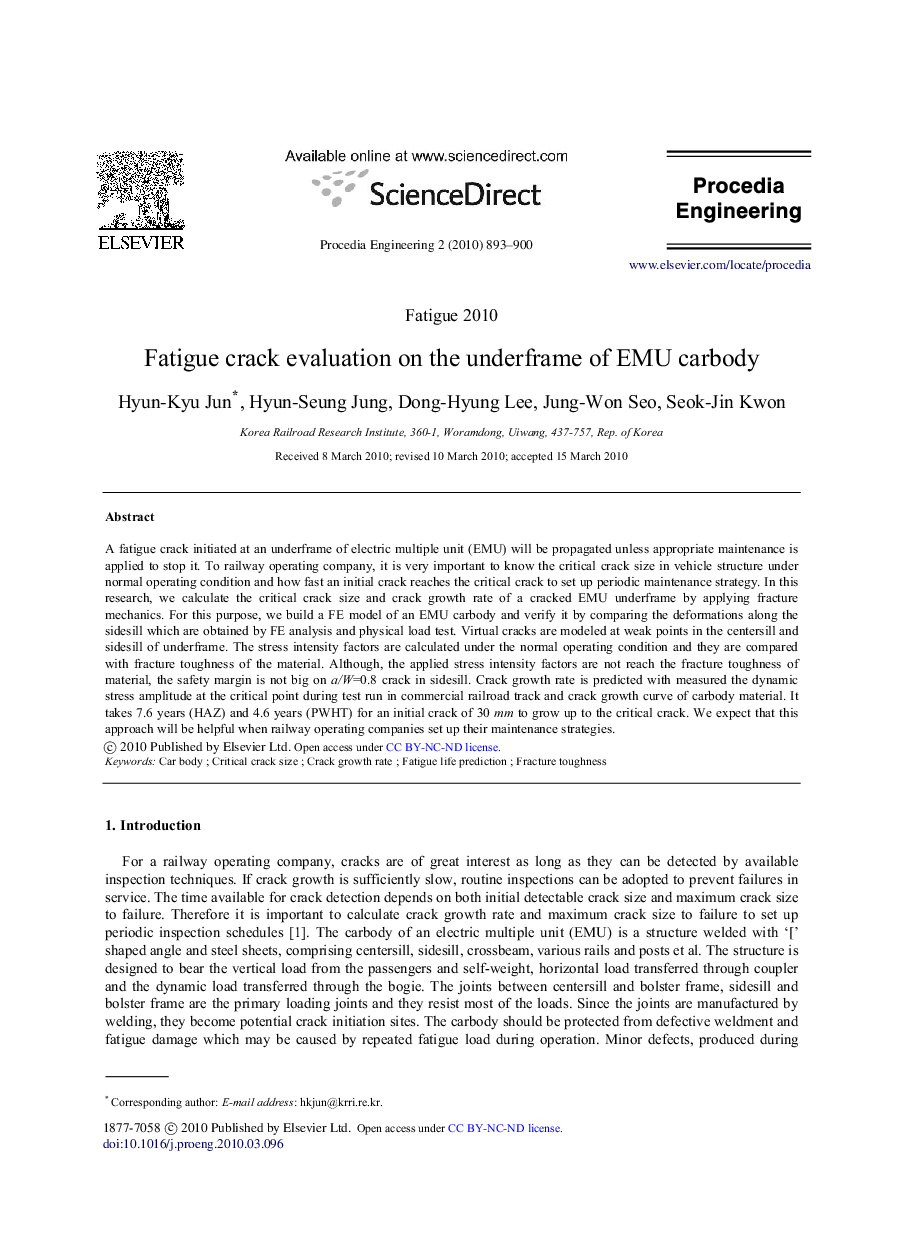
A fatigue crack initiated at an underframe of electric multiple unit (EMU) will be propagated unless appropriate maintenance is applied to stop it. To railway operating company, it is very important to know the critical crack size in vehicle structure under normal operating condition and how fast an initial crack reaches the critical crack to set up periodic maintenance strategy. In this research, we calculate the critical crack size and crack growth rate of a cracked EMU underframe by applying fracture mechanics. For this purpose, we build a FE model of an EMU carbody and verify it by comparing the deformations along the sidesill which are obtained by FE analysis and physical load test. Virtual cracks are modeled at weak points in the centersill and sidesill of underframe. The stress intensity factors are calculated under the normal operating condition and they are compared with fracture toughness of the material. Although, the applied stress intensity factors are not reach the fracture toughness of material, the safety margin is not big on a/W=0.8 crack in sidesill. Crack growth rate is predicted with measured the dynamic stress amplitude at the critical point during test run in commercial railroad track and crack growth curve of carbody material. It takes 7.6 years (HAZ) and 4.6 years (PWHT) for an initial crack of 30 mm to grow up to the critical crack. We expect that this approach will be helpful when railway operating companies set up their maintenance strategies.
Journal: Procedia Engineering - Volume 2, Issue 1, April 2010, Pages 893-900