کد مقاله | کد نشریه | سال انتشار | مقاله انگلیسی | نسخه تمام متن |
---|---|---|---|---|
1663585 | 1008473 | 2006 | 11 صفحه PDF | دانلود رایگان |
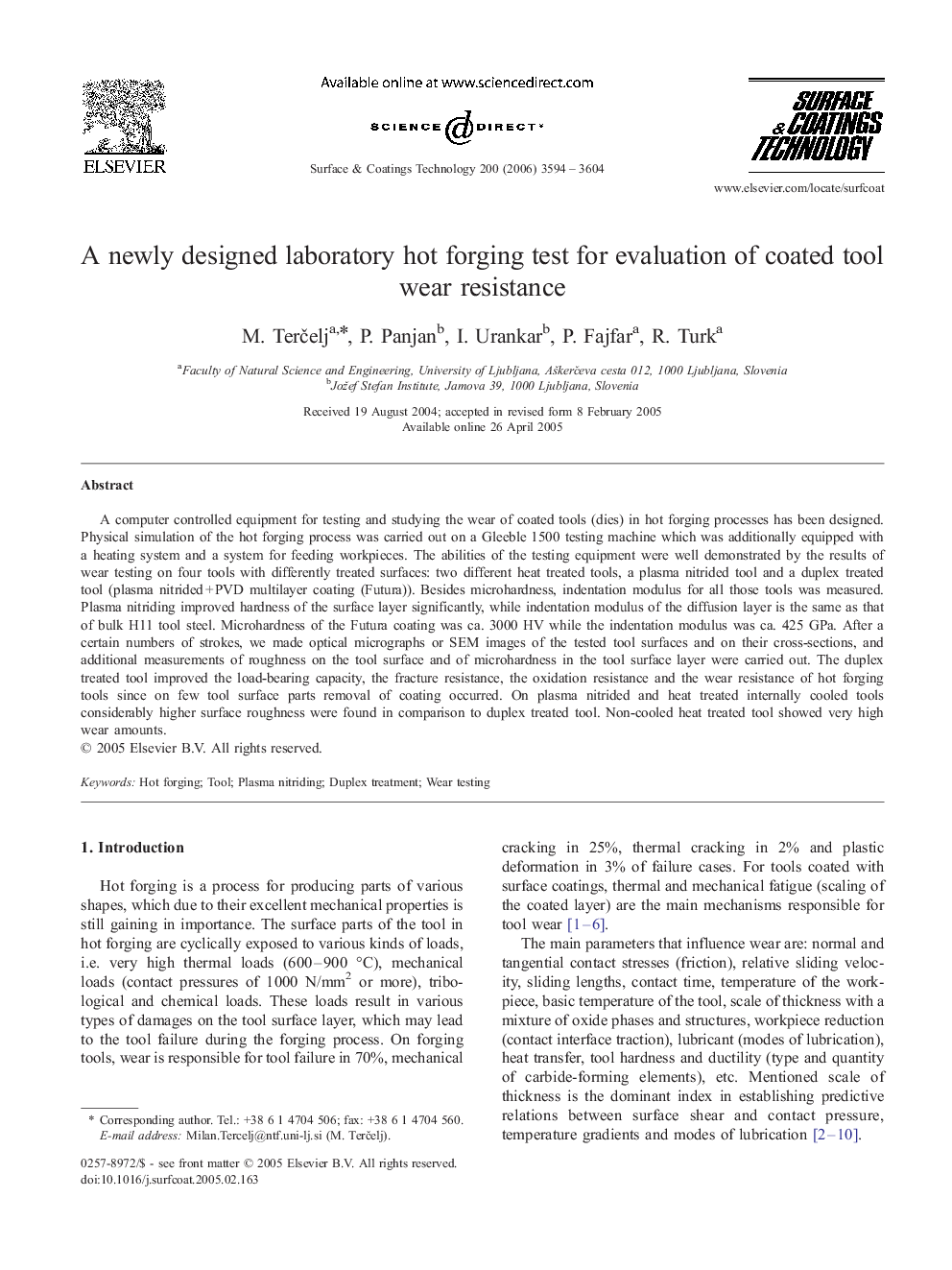
A computer controlled equipment for testing and studying the wear of coated tools (dies) in hot forging processes has been designed. Physical simulation of the hot forging process was carried out on a Gleeble 1500 testing machine which was additionally equipped with a heating system and a system for feeding workpieces. The abilities of the testing equipment were well demonstrated by the results of wear testing on four tools with differently treated surfaces: two different heat treated tools, a plasma nitrided tool and a duplex treated tool (plasma nitrided + PVD multilayer coating (Futura)). Besides microhardness, indentation modulus for all those tools was measured. Plasma nitriding improved hardness of the surface layer significantly, while indentation modulus of the diffusion layer is the same as that of bulk H11 tool steel. Microhardness of the Futura coating was ca. 3000 HV while the indentation modulus was ca. 425 GPa. After a certain numbers of strokes, we made optical micrographs or SEM images of the tested tool surfaces and on their cross-sections, and additional measurements of roughness on the tool surface and of microhardness in the tool surface layer were carried out. The duplex treated tool improved the load-bearing capacity, the fracture resistance, the oxidation resistance and the wear resistance of hot forging tools since on few tool surface parts removal of coating occurred. On plasma nitrided and heat treated internally cooled tools considerably higher surface roughness were found in comparison to duplex treated tool. Non-cooled heat treated tool showed very high wear amounts.
Journal: Surface and Coatings Technology - Volume 200, Issue 11, 15 March 2006, Pages 3594–3604