کد مقاله | کد نشریه | سال انتشار | مقاله انگلیسی | نسخه تمام متن |
---|---|---|---|---|
237387 | 465704 | 2012 | 7 صفحه PDF | دانلود رایگان |
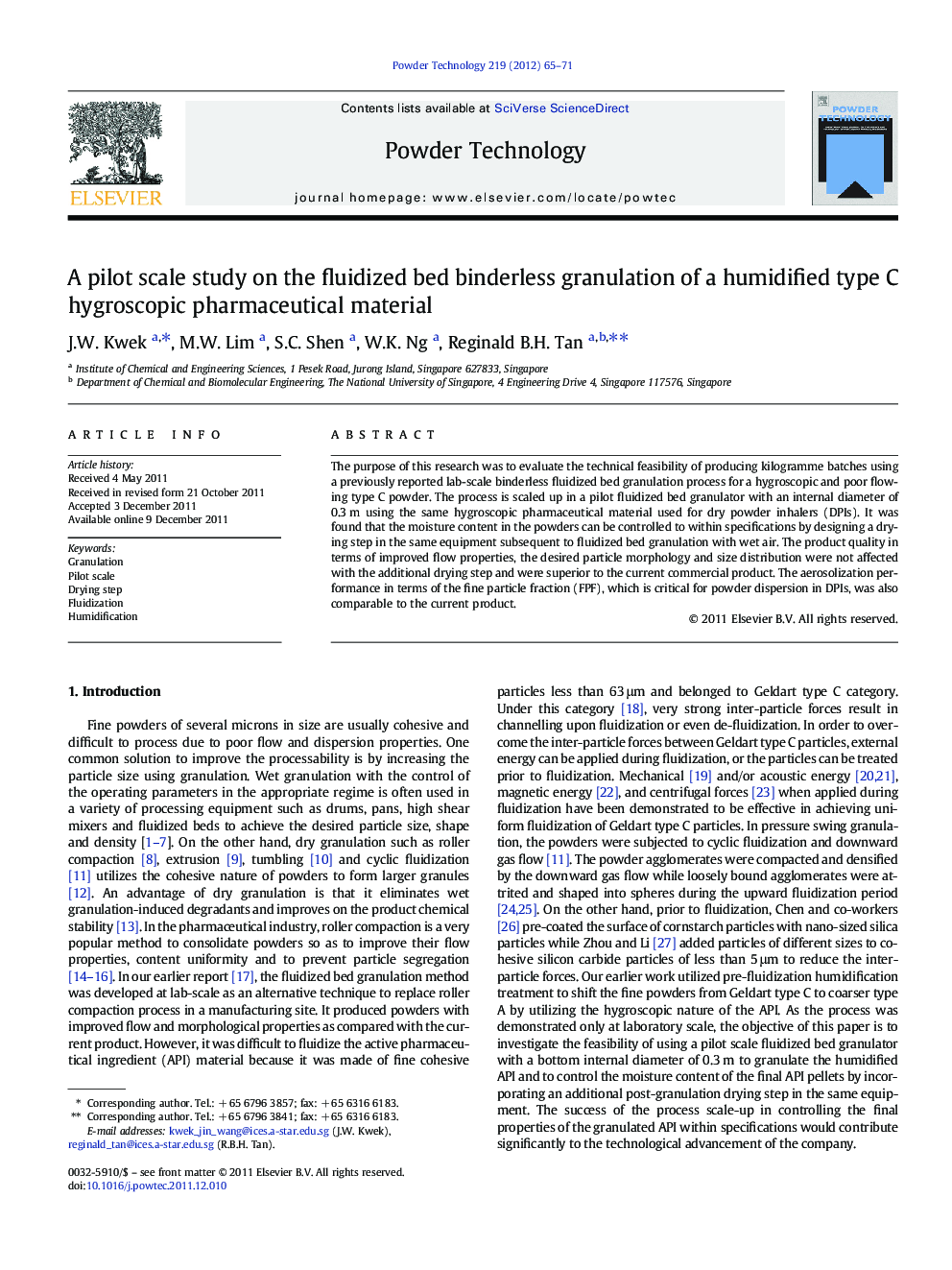
The purpose of this research was to evaluate the technical feasibility of producing kilogramme batches using a previously reported lab-scale binderless fluidized bed granulation process for a hygroscopic and poor flowing type C powder. The process is scaled up in a pilot fluidized bed granulator with an internal diameter of 0.3 m using the same hygroscopic pharmaceutical material used for dry powder inhalers (DPIs). It was found that the moisture content in the powders can be controlled to within specifications by designing a drying step in the same equipment subsequent to fluidized bed granulation with wet air. The product quality in terms of improved flow properties, the desired particle morphology and size distribution were not affected with the additional drying step and were superior to the current commercial product. The aerosolization performance in terms of the fine particle fraction (FPF), which is critical for powder dispersion in DPIs, was also comparable to the current product.
This paper discussed about the success of a pilot plant scale-up study of the binderless fluidized bed granulation to replace the current industrial roller compacting process of a cohesive Geldart type C pharmaceutical powder. After fluidization, the material had improved flow and aerosolized performance with good control of the moisture content via the incorporation of a drying step.Figure optionsDownload as PowerPoint slideHighlights
► A pilot-scale binderless fluidized bed granulation process.
► More compact and spherical granules after fluidization.
► Improved flow and aerosolization performance in fluidized granules.
► Control of moisture content through incorporation of drying step.
Journal: Powder Technology - Volume 219, March 2012, Pages 65–71