کد مقاله | کد نشریه | سال انتشار | مقاله انگلیسی | نسخه تمام متن |
---|---|---|---|---|
237672 | 465718 | 2010 | 17 صفحه PDF | دانلود رایگان |
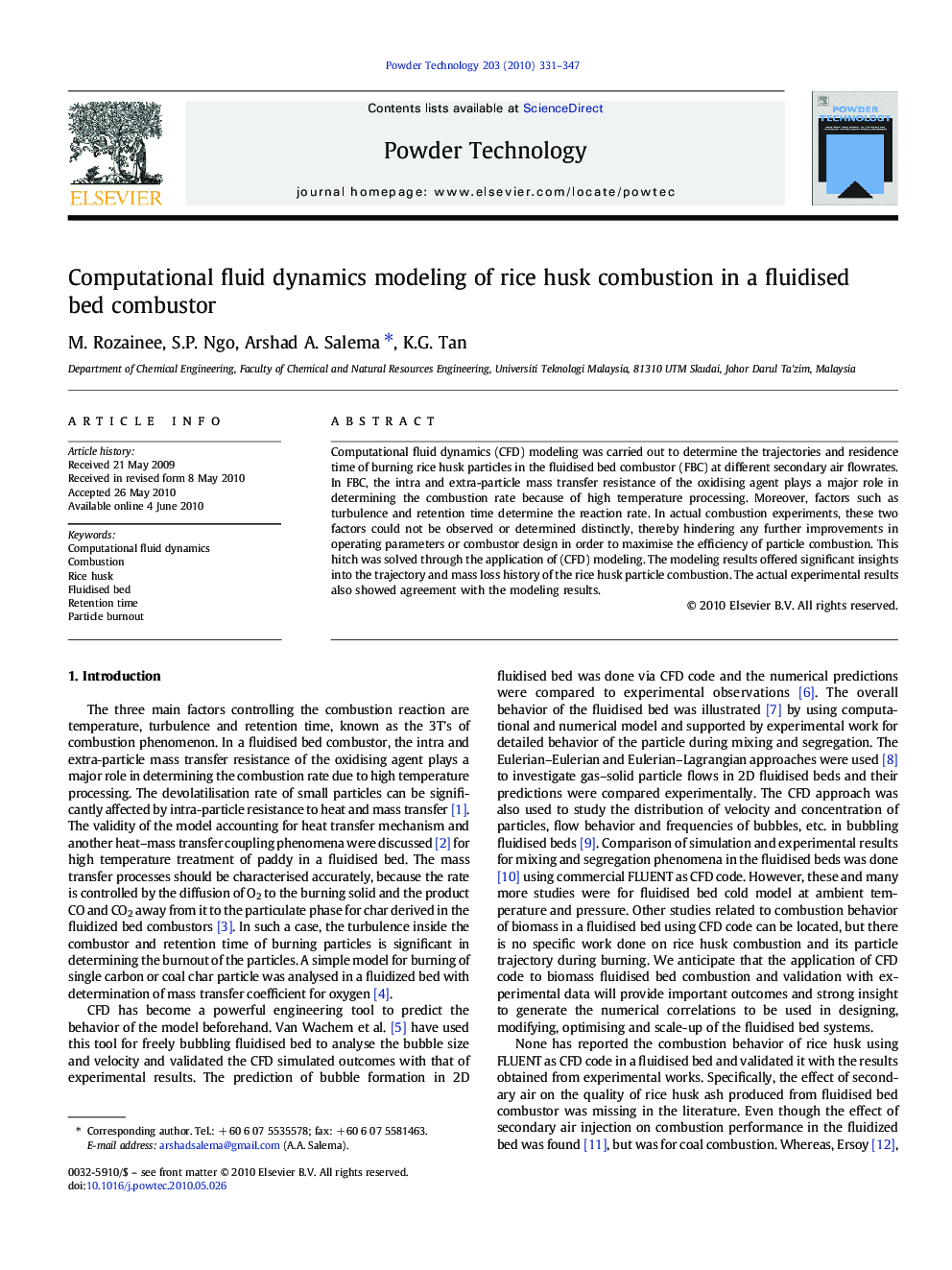
Computational fluid dynamics (CFD) modeling was carried out to determine the trajectories and residence time of burning rice husk particles in the fluidised bed combustor (FBC) at different secondary air flowrates. In FBC, the intra and extra-particle mass transfer resistance of the oxidising agent plays a major role in determining the combustion rate because of high temperature processing. Moreover, factors such as turbulence and retention time determine the reaction rate. In actual combustion experiments, these two factors could not be observed or determined distinctly, thereby hindering any further improvements in operating parameters or combustor design in order to maximise the efficiency of particle combustion. This hitch was solved through the application of (CFD) modeling. The modeling results offered significant insights into the trajectory and mass loss history of the rice husk particle combustion. The actual experimental results also showed agreement with the modeling results.
Graphical AbstractIn actual combustion, the factors such as turbulence and retention time could not be determined distinctly, thereby hindering any improvement efforts to maximise the burning rate of biomass particles in the fluidised bed combustor. The CFD modeling offers significant insights into the trajectory and mass loss history of the burning rice husk particles, which otherwise is not possible experimentally.Figure optionsDownload as PowerPoint slide
Journal: Powder Technology - Volume 203, Issue 2, 10 November 2010, Pages 331–347