کد مقاله | کد نشریه | سال انتشار | مقاله انگلیسی | نسخه تمام متن |
---|---|---|---|---|
4986002 | 1454792 | 2017 | 9 صفحه PDF | دانلود رایگان |
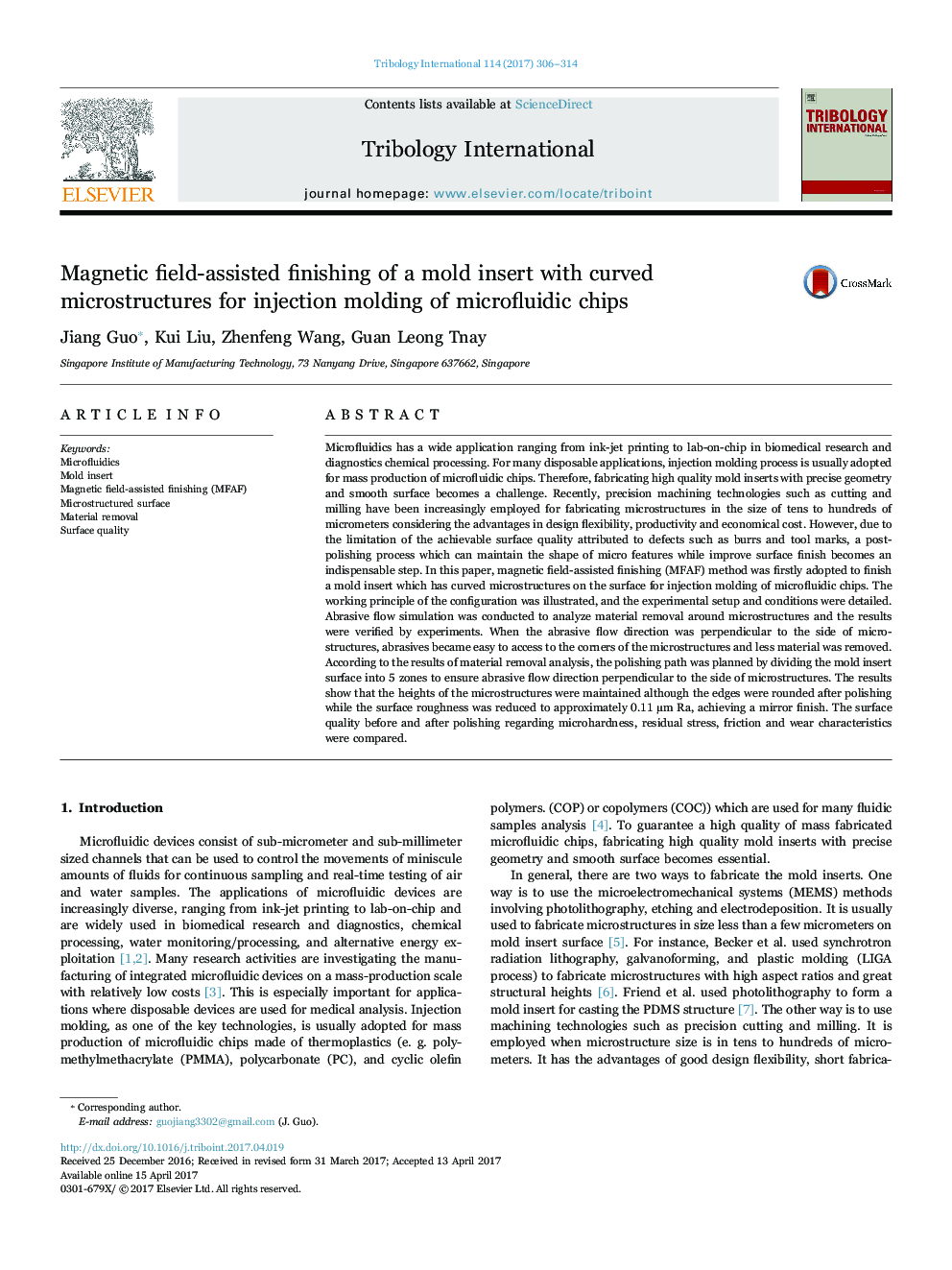
- Magnetic field-assisted finishing (MFAF) was firstly adopted to finish curved microstructures.
- Abrasive flow simulation was presented to analyze material removal around microstructures.
- Results demonstrate the height of the microstructures was maintained although the edge became round after polishing.
- The surface roughness was reduced to approximately 0.1 μm Ra, achieving a mirror finish.
- The surface quality before and after polishing regarding microhardness, residual stress, friction and wear characteristics were compared.
Microfluidics has a wide application ranging from ink-jet printing to lab-on-chip in biomedical research and diagnostics chemical processing. For many disposable applications, injection molding process is usually adopted for mass production of microfluidic chips. Therefore, fabricating high quality mold inserts with precise geometry and smooth surface becomes a challenge. Recently, precision machining technologies such as cutting and milling have been increasingly employed for fabricating microstructures in the size of tens to hundreds of micrometers considering the advantages in design flexibility, productivity and economical cost. However, due to the limitation of the achievable surface quality attributed to defects such as burrs and tool marks, a post-polishing process which can maintain the shape of micro features while improve surface finish becomes an indispensable step. In this paper, magnetic field-assisted finishing (MFAF) method was firstly adopted to finish a mold insert which has curved microstructures on the surface for injection molding of microfluidic chips. The working principle of the configuration was illustrated, and the experimental setup and conditions were detailed. Abrasive flow simulation was conducted to analyze material removal around microstructures and the results were verified by experiments. When the abrasive flow direction was perpendicular to the side of microstructures, abrasives became easy to access to the corners of the microstructures and less material was removed. According to the results of material removal analysis, the polishing path was planned by dividing the mold insert surface into 5 zones to ensure abrasive flow direction perpendicular to the side of microstructures. The results show that the heights of the microstructures were maintained although the edges were rounded after polishing while the surface roughness was reduced to approximately 0.11 µm Ra, achieving a mirror finish. The surface quality before and after polishing regarding microhardness, residual stress, friction and wear characteristics were compared.
335
Journal: Tribology International - Volume 114, October 2017, Pages 306-314