کد مقاله | کد نشریه | سال انتشار | مقاله انگلیسی | نسخه تمام متن |
---|---|---|---|---|
5480187 | 1522105 | 2017 | 12 صفحه PDF | دانلود رایگان |
عنوان انگلیسی مقاله ISI
Recovery of Zn (II), Mn (II), Cd (II) and Ni (II) from the unsorted spent batteries using solvent extraction, electrodeposition and precipitation methods
دانلود مقاله + سفارش ترجمه
دانلود مقاله ISI انگلیسی
رایگان برای ایرانیان
کلمات کلیدی
موضوعات مرتبط
مهندسی و علوم پایه
مهندسی انرژی
انرژی های تجدید پذیر، توسعه پایدار و محیط زیست
پیش نمایش صفحه اول مقاله
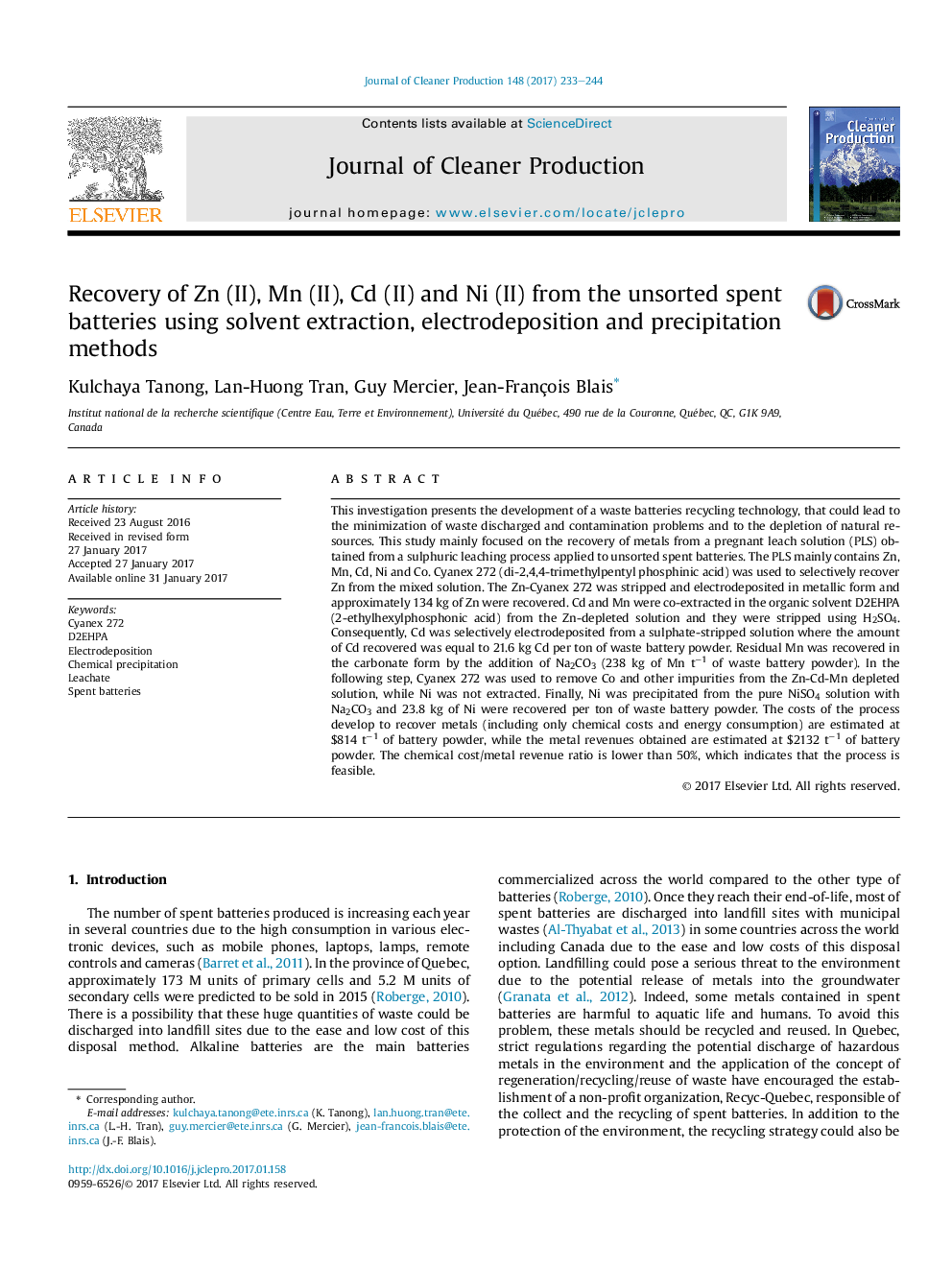
چکیده انگلیسی
This investigation presents the development of a waste batteries recycling technology, that could lead to the minimization of waste discharged and contamination problems and to the depletion of natural resources. This study mainly focused on the recovery of metals from a pregnant leach solution (PLS) obtained from a sulphuric leaching process applied to unsorted spent batteries. The PLS mainly contains Zn, Mn, Cd, Ni and Co. Cyanex 272 (di-2,4,4-trimethylpentyl phosphinic acid) was used to selectively recover Zn from the mixed solution. The Zn-Cyanex 272 was stripped and electrodeposited in metallic form and approximately 134Â kg of Zn were recovered. Cd and Mn were co-extracted in the organic solvent D2EHPA (2-ethylhexylphosphonic acid) from the Zn-depleted solution and they were stripped using H2SO4. Consequently, Cd was selectively electrodeposited from a sulphate-stripped solution where the amount of Cd recovered was equal to 21.6Â kg Cd per ton of waste battery powder. Residual Mn was recovered in the carbonate form by the addition of Na2CO3 (238Â kg of Mn tâ1 of waste battery powder). In the following step, Cyanex 272 was used to remove Co and other impurities from the Zn-Cd-Mn depleted solution, while Ni was not extracted. Finally, Ni was precipitated from the pure NiSO4 solution with Na2CO3 and 23.8Â kg of Ni were recovered per ton of waste battery powder. The costs of the process develop to recover metals (including only chemical costs and energy consumption) are estimated at $814Â tâ1 of battery powder, while the metal revenues obtained are estimated at $2132Â tâ1 of battery powder. The chemical cost/metal revenue ratio is lower than 50%, which indicates that the process is feasible.
ناشر
Database: Elsevier - ScienceDirect (ساینس دایرکت)
Journal: Journal of Cleaner Production - Volume 148, 1 April 2017, Pages 233-244
Journal: Journal of Cleaner Production - Volume 148, 1 April 2017, Pages 233-244
نویسندگان
Kulchaya Tanong, Lan-Huong Tran, Guy Mercier, Jean-François Blais,