کد مقاله | کد نشریه | سال انتشار | مقاله انگلیسی | نسخه تمام متن |
---|---|---|---|---|
58199 | 47144 | 2007 | 5 صفحه PDF | دانلود رایگان |
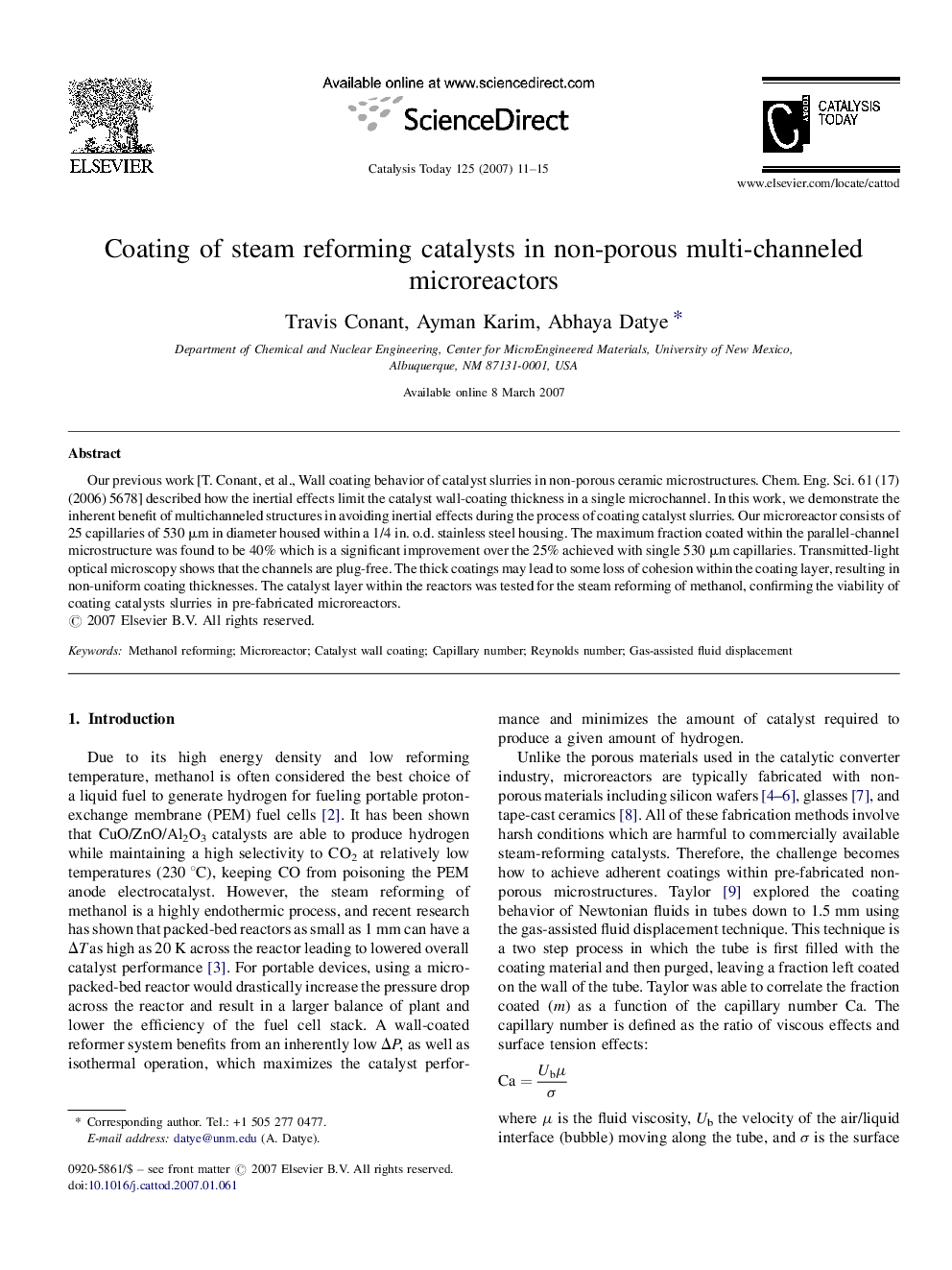
Our previous work [T. Conant, et al., Wall coating behavior of catalyst slurries in non-porous ceramic microstructures. Chem. Eng. Sci. 61 (17) (2006) 5678] described how the inertial effects limit the catalyst wall-coating thickness in a single microchannel. In this work, we demonstrate the inherent benefit of multichanneled structures in avoiding inertial effects during the process of coating catalyst slurries. Our microreactor consists of 25 capillaries of 530 μm in diameter housed within a 1/4 in. o.d. stainless steel housing. The maximum fraction coated within the parallel-channel microstructure was found to be 40% which is a significant improvement over the 25% achieved with single 530 μm capillaries. Transmitted-light optical microscopy shows that the channels are plug-free. The thick coatings may lead to some loss of cohesion within the coating layer, resulting in non-uniform coating thicknesses. The catalyst layer within the reactors was tested for the steam reforming of methanol, confirming the viability of coating catalysts slurries in pre-fabricated microreactors.
Journal: Catalysis Today - Volume 125, Issues 1–2, 15 July 2007, Pages 11–15