کد مقاله | کد نشریه | سال انتشار | مقاله انگلیسی | نسخه تمام متن |
---|---|---|---|---|
615508 | 881449 | 2012 | 11 صفحه PDF | دانلود رایگان |
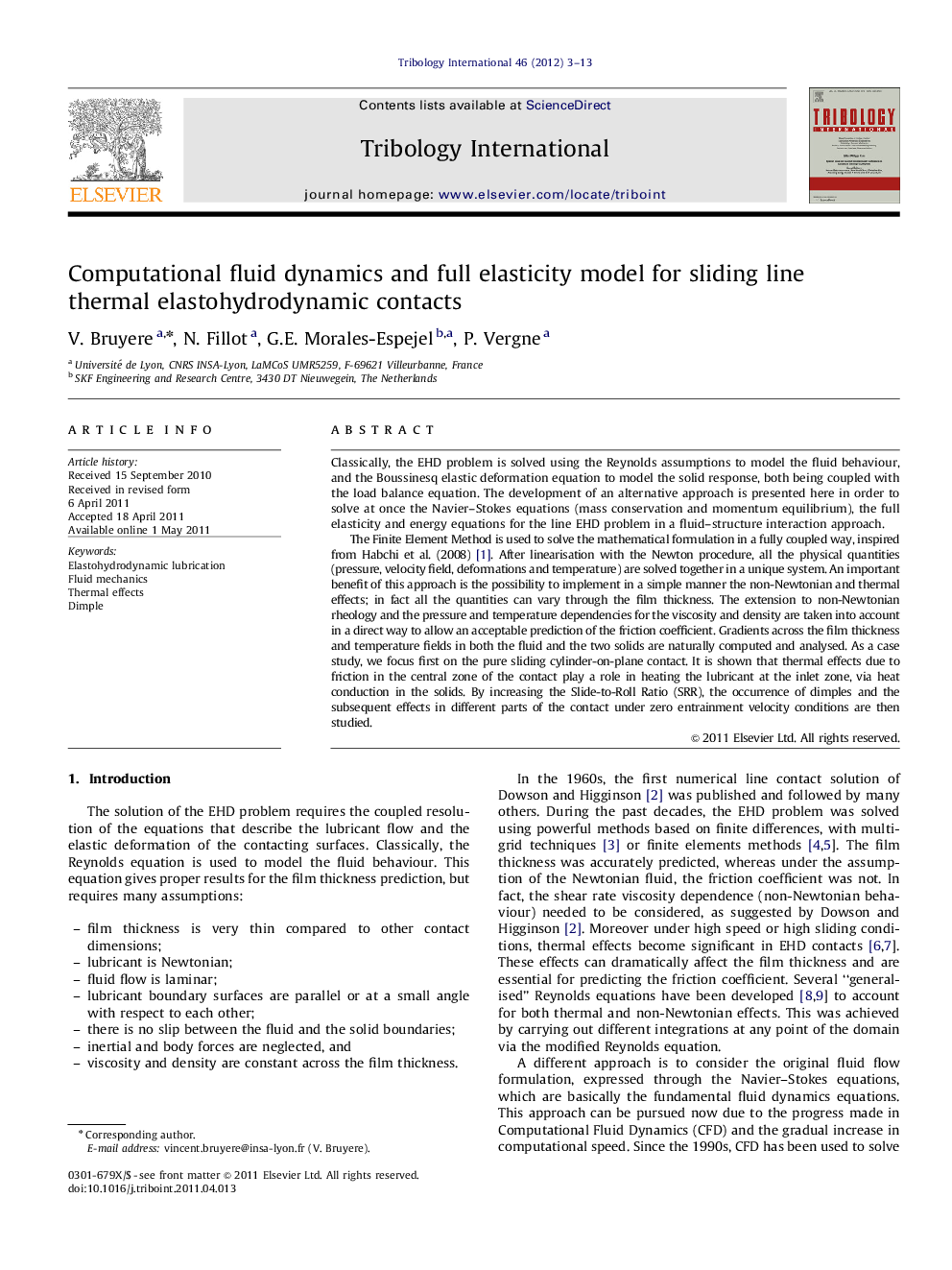
Classically, the EHD problem is solved using the Reynolds assumptions to model the fluid behaviour, and the Boussinesq elastic deformation equation to model the solid response, both being coupled with the load balance equation. The development of an alternative approach is presented here in order to solve at once the Navier–Stokes equations (mass conservation and momentum equilibrium), the full elasticity and energy equations for the line EHD problem in a fluid–structure interaction approach.The Finite Element Method is used to solve the mathematical formulation in a fully coupled way, inspired from Habchi et al. (2008) [1]. After linearisation with the Newton procedure, all the physical quantities (pressure, velocity field, deformations and temperature) are solved together in a unique system. An important benefit of this approach is the possibility to implement in a simple manner the non-Newtonian and thermal effects; in fact all the quantities can vary through the film thickness. The extension to non-Newtonian rheology and the pressure and temperature dependencies for the viscosity and density are taken into account in a direct way to allow an acceptable prediction of the friction coefficient. Gradients across the film thickness and temperature fields in both the fluid and the two solids are naturally computed and analysed. As a case study, we focus first on the pure sliding cylinder-on-plane contact. It is shown that thermal effects due to friction in the central zone of the contact play a role in heating the lubricant at the inlet zone, via heat conduction in the solids. By increasing the Slide-to-Roll Ratio (SRR), the occurrence of dimples and the subsequent effects in different parts of the contact under zero entrainment velocity conditions are then studied.
► Fluid thickness dimension is added to TEHD contacts using the Navier–Stokes equations.
► Highly sliding non-Newtonian and thermal cases are computed and studied.
► Local minimum in friction is explained by conduction effect in stationary solid.
► Viscosity wedge theory explains dimple formation and shape.
► This general approach can qualitatively explain intriguing experimental results.
Journal: Tribology International - Volume 46, Issue 1, February 2012, Pages 3–13