کد مقاله | کد نشریه | سال انتشار | مقاله انگلیسی | نسخه تمام متن |
---|---|---|---|---|
727308 | 1461514 | 2015 | 11 صفحه PDF | دانلود رایگان |
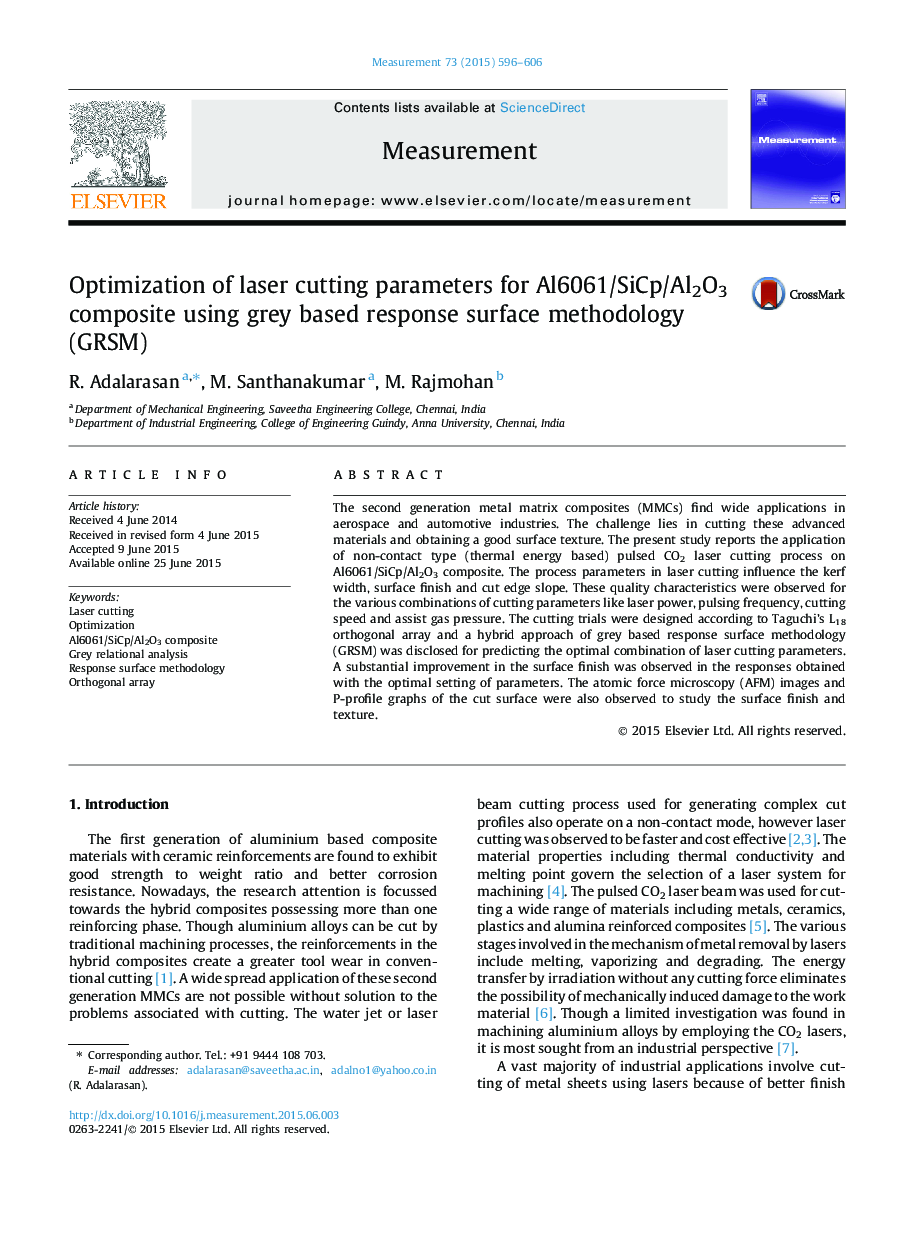
• Taguchi’s orthogonal array for designing the pulsed CO2 laser cutting trials.
• Reduced experimental trials (L18 array) than central composite design.
• Grey based response surface methodology (GRSM) for optimization.
• Uncertainty handling ability of grey theory combined with modelling power of RSM.
• Research findings offer guidelines for cutting Al6061/SiC/Al2O3 composite.
The second generation metal matrix composites (MMCs) find wide applications in aerospace and automotive industries. The challenge lies in cutting these advanced materials and obtaining a good surface texture. The present study reports the application of non-contact type (thermal energy based) pulsed CO2 laser cutting process on Al6061/SiCp/Al2O3 composite. The process parameters in laser cutting influence the kerf width, surface finish and cut edge slope. These quality characteristics were observed for the various combinations of cutting parameters like laser power, pulsing frequency, cutting speed and assist gas pressure. The cutting trials were designed according to Taguchi’s L18 orthogonal array and a hybrid approach of grey based response surface methodology (GRSM) was disclosed for predicting the optimal combination of laser cutting parameters. A substantial improvement in the surface finish was observed in the responses obtained with the optimal setting of parameters. The atomic force microscopy (AFM) images and P-profile graphs of the cut surface were also observed to study the surface finish and texture.
Journal: Measurement - Volume 73, September 2015, Pages 596–606