کد مقاله | کد نشریه | سال انتشار | مقاله انگلیسی | نسخه تمام متن |
---|---|---|---|---|
730075 | 892950 | 2013 | 12 صفحه PDF | دانلود رایگان |
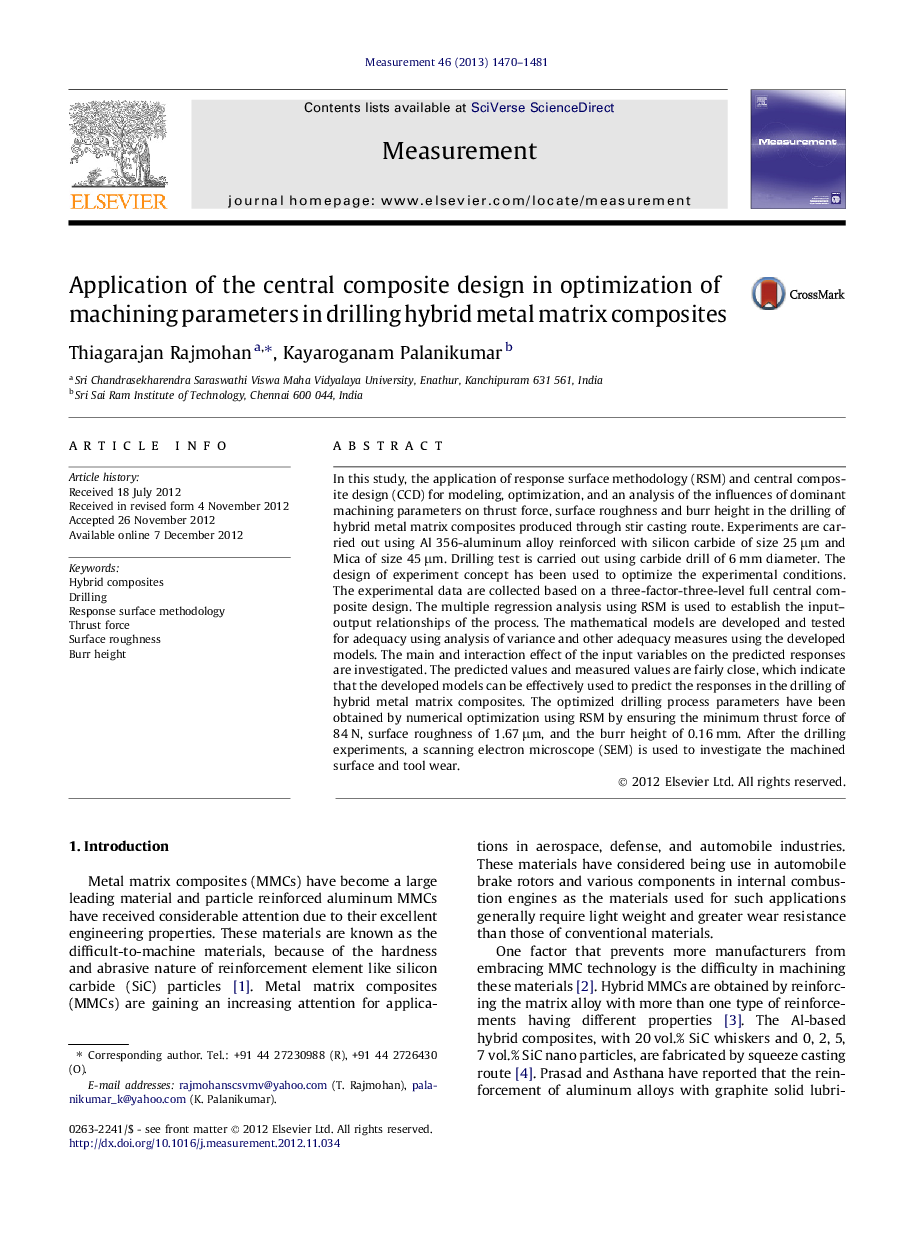
In this study, the application of response surface methodology (RSM) and central composite design (CCD) for modeling, optimization, and an analysis of the influences of dominant machining parameters on thrust force, surface roughness and burr height in the drilling of hybrid metal matrix composites produced through stir casting route. Experiments are carried out using Al 356-aluminum alloy reinforced with silicon carbide of size 25 μm and Mica of size 45 μm. Drilling test is carried out using carbide drill of 6 mm diameter. The design of experiment concept has been used to optimize the experimental conditions. The experimental data are collected based on a three-factor-three-level full central composite design. The multiple regression analysis using RSM is used to establish the input–output relationships of the process. The mathematical models are developed and tested for adequacy using analysis of variance and other adequacy measures using the developed models. The main and interaction effect of the input variables on the predicted responses are investigated. The predicted values and measured values are fairly close, which indicate that the developed models can be effectively used to predict the responses in the drilling of hybrid metal matrix composites. The optimized drilling process parameters have been obtained by numerical optimization using RSM by ensuring the minimum thrust force of 84 N, surface roughness of 1.67 μm, and the burr height of 0.16 mm. After the drilling experiments, a scanning electron microscope (SEM) is used to investigate the machined surface and tool wear.
Figure optionsDownload as PowerPoint slideHighlights
► The experimental data were collected based on three-level full central composite design.
► RSM was conducted to establish input–output relationships of the process.
► The mathematical models were developed and tested for adequacy using ANOVA.
► The optimized drilling process parameters obtained by numerical optimization using RSM.
► Scanning electron microscope (SEM) was used to investigate the machined surface and tool wear.
Journal: Measurement - Volume 46, Issue 4, May 2013, Pages 1470–1481