کد مقاله | کد نشریه | سال انتشار | مقاله انگلیسی | نسخه تمام متن |
---|---|---|---|---|
756676 | 1462733 | 2013 | 9 صفحه PDF | دانلود رایگان |
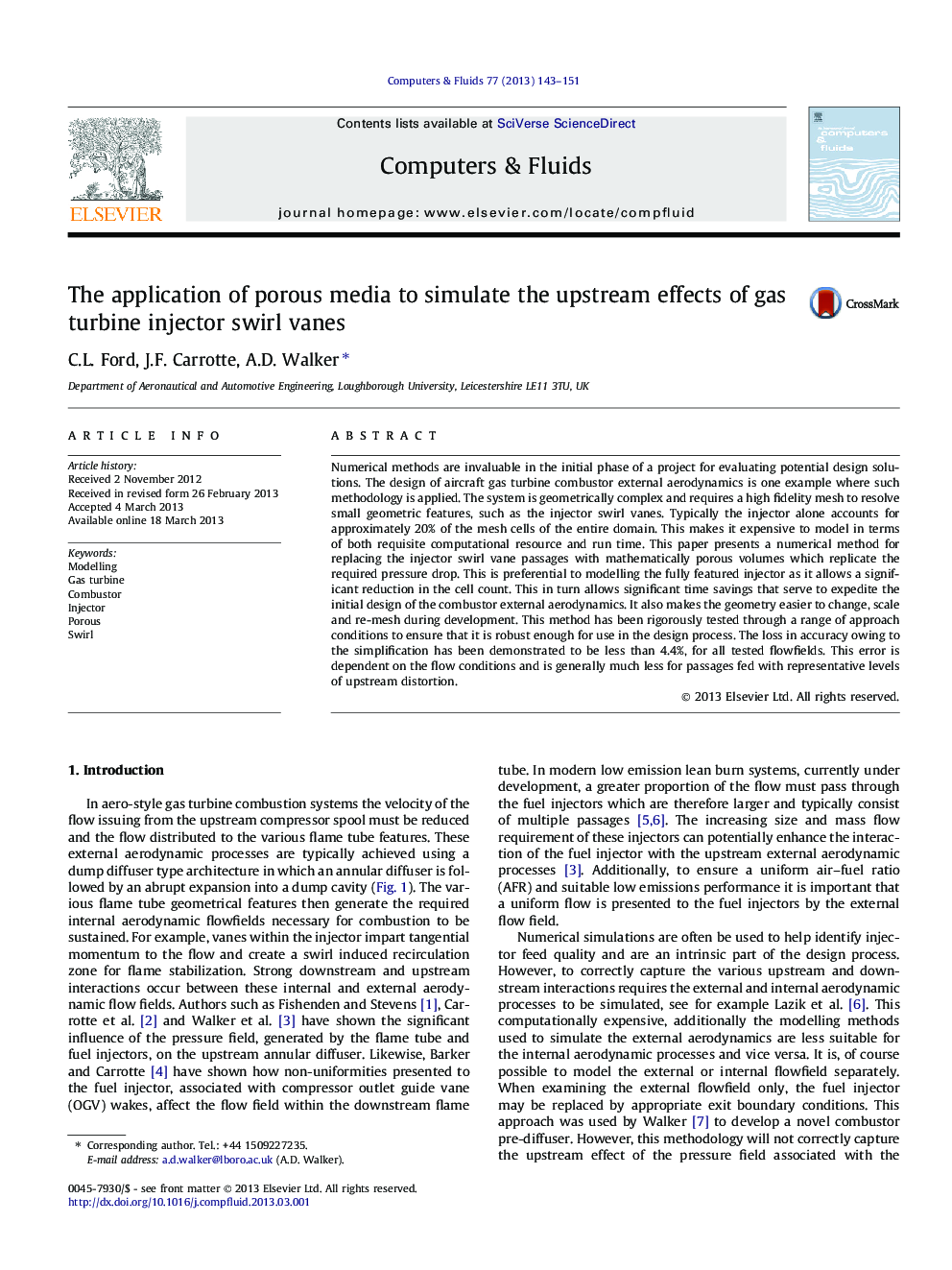
• A method of modelling injector pressure drop, replacing the swirl vanes is proposed.
• The method correctly models the injector near field velocity distribution.
• Comparison of the method with fully featured injector geometry shows good agreement.
• The methodology allows up to 70% saving in computational time.
Numerical methods are invaluable in the initial phase of a project for evaluating potential design solutions. The design of aircraft gas turbine combustor external aerodynamics is one example where such methodology is applied. The system is geometrically complex and requires a high fidelity mesh to resolve small geometric features, such as the injector swirl vanes. Typically the injector alone accounts for approximately 20% of the mesh cells of the entire domain. This makes it expensive to model in terms of both requisite computational resource and run time. This paper presents a numerical method for replacing the injector swirl vane passages with mathematically porous volumes which replicate the required pressure drop. This is preferential to modelling the fully featured injector as it allows a significant reduction in the cell count. This in turn allows significant time savings that serve to expedite the initial design of the combustor external aerodynamics. It also makes the geometry easier to change, scale and re-mesh during development. This method has been rigorously tested through a range of approach conditions to ensure that it is robust enough for use in the design process. The loss in accuracy owing to the simplification has been demonstrated to be less than 4.4%, for all tested flowfields. This error is dependent on the flow conditions and is generally much less for passages fed with representative levels of upstream distortion.
Journal: Computers & Fluids - Volume 77, 1 April 2013, Pages 143–151