کد مقاله | کد نشریه | سال انتشار | مقاله انگلیسی | نسخه تمام متن |
---|---|---|---|---|
775352 | 1463778 | 2013 | 15 صفحه PDF | دانلود رایگان |
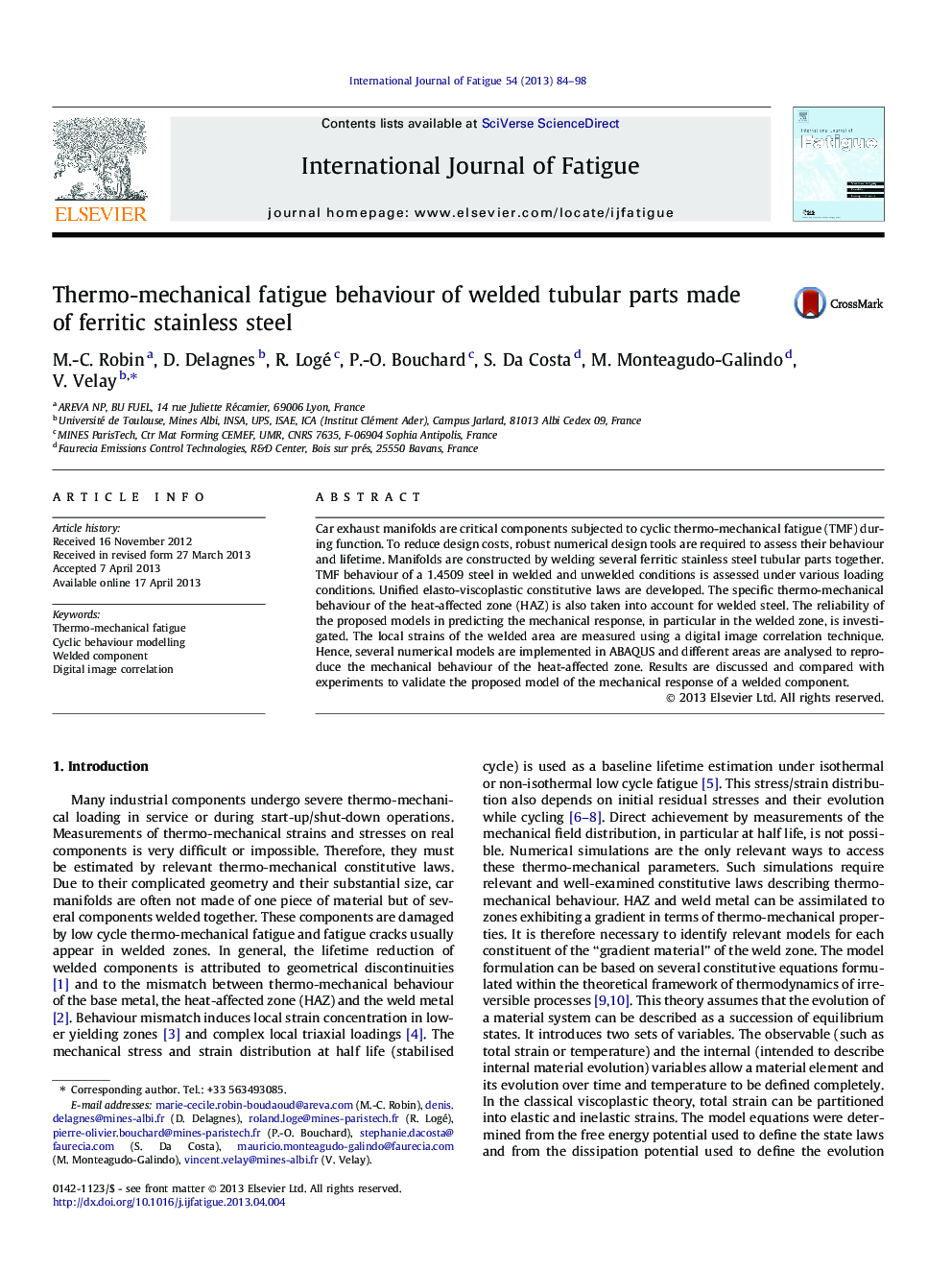
• Alternative methodology for modelling the mechanical response of welded zones.
• Specimen with microstructures similar to the tubular parts of the manifold component.
• Identification of relevant models for each constituent of the “gradient material”.
• Cyclic behaviour modelling (at different T) of the welded sample using FE simulation.
• Validation of the model response in the different area using DIC technique.
Car exhaust manifolds are critical components subjected to cyclic thermo-mechanical fatigue (TMF) during function. To reduce design costs, robust numerical design tools are required to assess their behaviour and lifetime. Manifolds are constructed by welding several ferritic stainless steel tubular parts together. TMF behaviour of a 1.4509 steel in welded and unwelded conditions is assessed under various loading conditions. Unified elasto-viscoplastic constitutive laws are developed. The specific thermo-mechanical behaviour of the heat-affected zone (HAZ) is also taken into account for welded steel. The reliability of the proposed models in predicting the mechanical response, in particular in the welded zone, is investigated. The local strains of the welded area are measured using a digital image correlation technique. Hence, several numerical models are implemented in ABAQUS and different areas are analysed to reproduce the mechanical behaviour of the heat-affected zone. Results are discussed and compared with experiments to validate the proposed model of the mechanical response of a welded component.
Journal: International Journal of Fatigue - Volume 54, September 2013, Pages 84–98