کد مقاله | کد نشریه | سال انتشار | مقاله انگلیسی | نسخه تمام متن |
---|---|---|---|---|
777760 | 1463795 | 2012 | 13 صفحه PDF | دانلود رایگان |
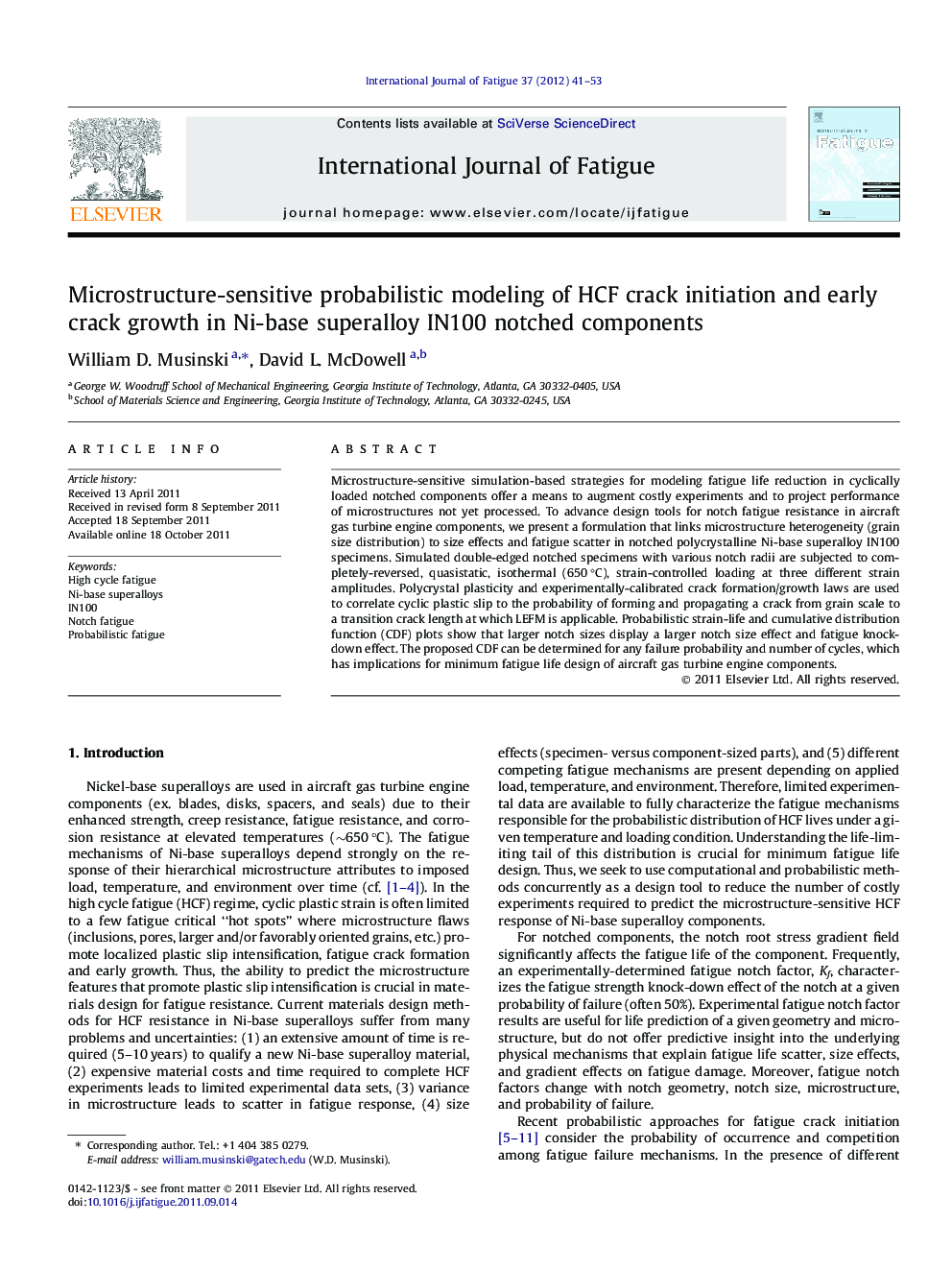
Microstructure-sensitive simulation-based strategies for modeling fatigue life reduction in cyclically loaded notched components offer a means to augment costly experiments and to project performance of microstructures not yet processed. To advance design tools for notch fatigue resistance in aircraft gas turbine engine components, we present a formulation that links microstructure heterogeneity (grain size distribution) to size effects and fatigue scatter in notched polycrystalline Ni-base superalloy IN100 specimens. Simulated double-edged notched specimens with various notch radii are subjected to completely-reversed, quasistatic, isothermal (650 °C), strain-controlled loading at three different strain amplitudes. Polycrystal plasticity and experimentally-calibrated crack formation/growth laws are used to correlate cyclic plastic slip to the probability of forming and propagating a crack from grain scale to a transition crack length at which LEFM is applicable. Probabilistic strain-life and cumulative distribution function (CDF) plots show that larger notch sizes display a larger notch size effect and fatigue knock-down effect. The proposed CDF can be determined for any failure probability and number of cycles, which has implications for minimum fatigue life design of aircraft gas turbine engine components.
► Computational model mimics strain-life smooth specimen data in LCF and HCF regimes.
► Polycrystal plasticity is used to correlate cyclic plastic slip to fatigue scatter.
► Notch size effects and knock-down effects shown for various notch sizes.
► CDF proposed for formation of crack on order of transition crack length.
► Equivalent Weibull distribution links applied stress to transition crack length CDF.
Journal: International Journal of Fatigue - Volume 37, April 2012, Pages 41–53