کد مقاله | کد نشریه | سال انتشار | مقاله انگلیسی | نسخه تمام متن |
---|---|---|---|---|
781060 | 1463790 | 2012 | 11 صفحه PDF | دانلود رایگان |
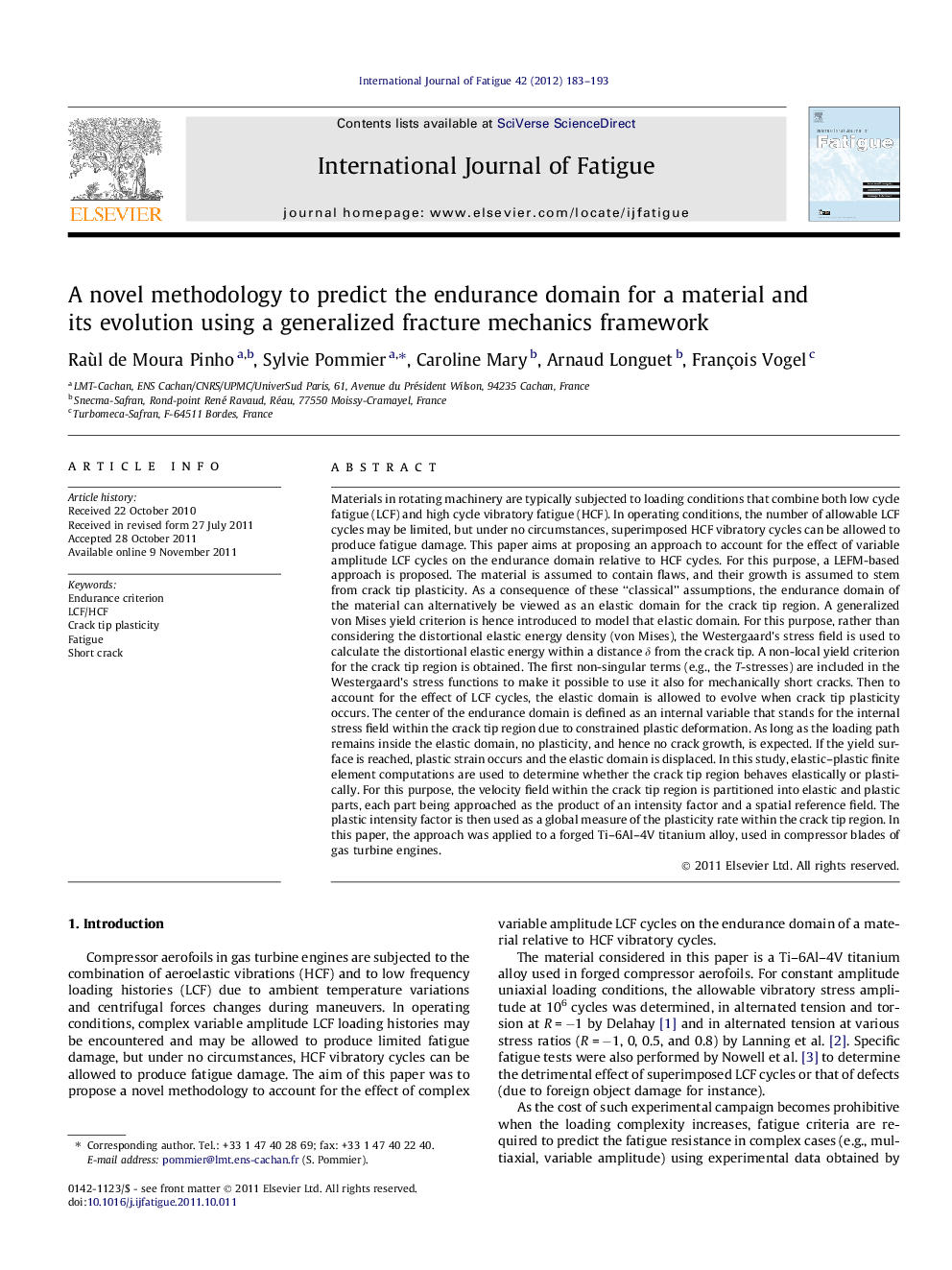
Materials in rotating machinery are typically subjected to loading conditions that combine both low cycle fatigue (LCF) and high cycle vibratory fatigue (HCF). In operating conditions, the number of allowable LCF cycles may be limited, but under no circumstances, superimposed HCF vibratory cycles can be allowed to produce fatigue damage. This paper aims at proposing an approach to account for the effect of variable amplitude LCF cycles on the endurance domain relative to HCF cycles. For this purpose, a LEFM-based approach is proposed. The material is assumed to contain flaws, and their growth is assumed to stem from crack tip plasticity. As a consequence of these “classical” assumptions, the endurance domain of the material can alternatively be viewed as an elastic domain for the crack tip region. A generalized von Mises yield criterion is hence introduced to model that elastic domain. For this purpose, rather than considering the distortional elastic energy density (von Mises), the Westergaard’s stress field is used to calculate the distortional elastic energy within a distance δ from the crack tip. A non-local yield criterion for the crack tip region is obtained. The first non-singular terms (e.g., the T-stresses) are included in the Westergaard’s stress functions to make it possible to use it also for mechanically short cracks. Then to account for the effect of LCF cycles, the elastic domain is allowed to evolve when crack tip plasticity occurs. The center of the endurance domain is defined as an internal variable that stands for the internal stress field within the crack tip region due to constrained plastic deformation. As long as the loading path remains inside the elastic domain, no plasticity, and hence no crack growth, is expected. If the yield surface is reached, plastic strain occurs and the elastic domain is displaced. In this study, elastic–plastic finite element computations are used to determine whether the crack tip region behaves elastically or plastically. For this purpose, the velocity field within the crack tip region is partitioned into elastic and plastic parts, each part being approached as the product of an intensity factor and a spatial reference field. The plastic intensity factor is then used as a global measure of the plasticity rate within the crack tip region. In this paper, the approach was applied to a forged Ti–6Al–4V titanium alloy, used in compressor blades of gas turbine engines.
Journal: International Journal of Fatigue - Volume 42, September 2012, Pages 183–193