کد مقاله | کد نشریه | سال انتشار | مقاله انگلیسی | نسخه تمام متن |
---|---|---|---|---|
84096 | 158860 | 2015 | 9 صفحه PDF | دانلود رایگان |
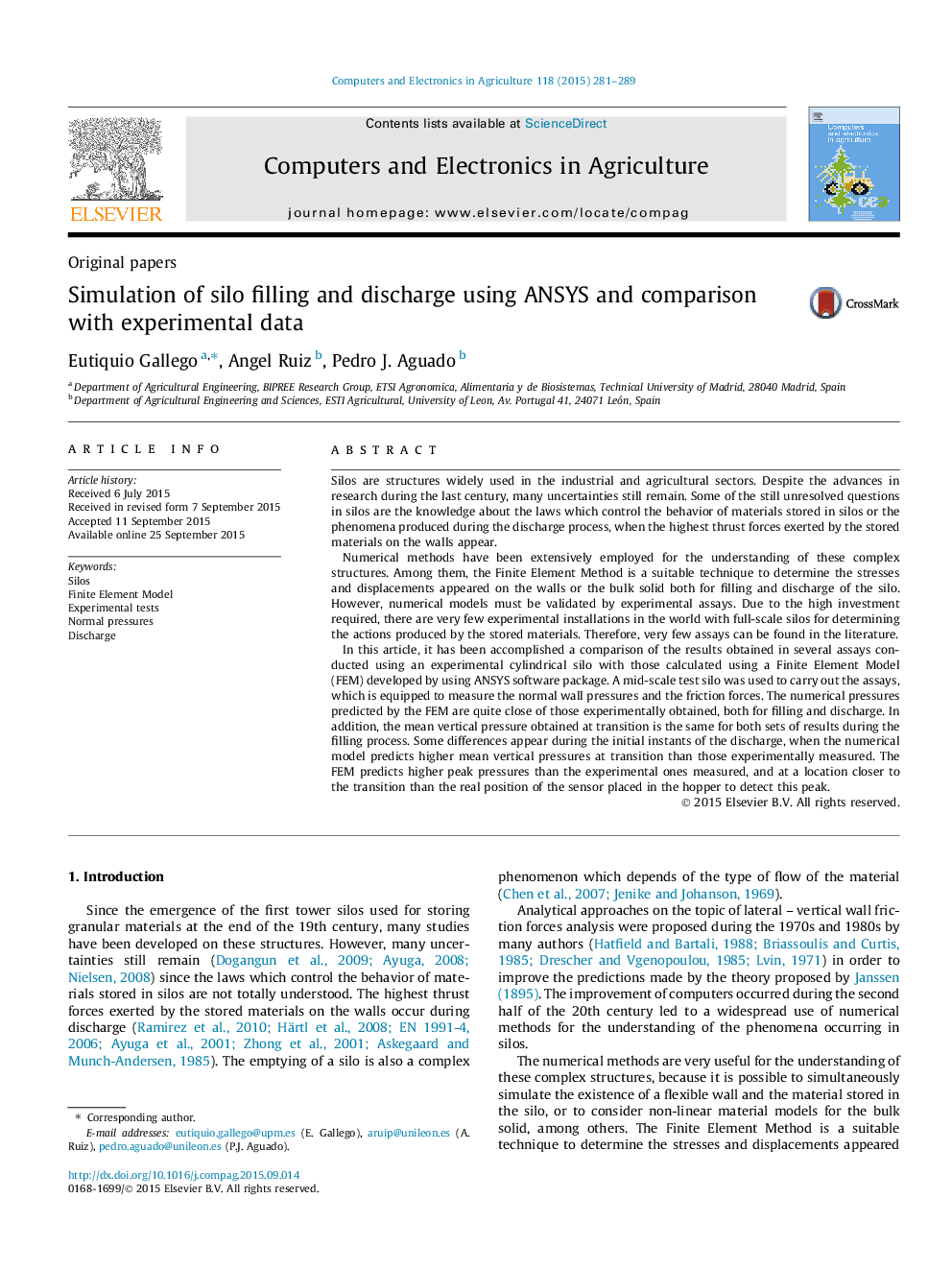
• Experimental tests have been conducted in bin–hopper silos.
• Results of Finite Element Models (FEMs) are close to the experimental values.
• The FEM predicts higher peak pressures than the experimental values.
• The FEM predicts that the peak pressure is located closer to the transition.
Silos are structures widely used in the industrial and agricultural sectors. Despite the advances in research during the last century, many uncertainties still remain. Some of the still unresolved questions in silos are the knowledge about the laws which control the behavior of materials stored in silos or the phenomena produced during the discharge process, when the highest thrust forces exerted by the stored materials on the walls appear.Numerical methods have been extensively employed for the understanding of these complex structures. Among them, the Finite Element Method is a suitable technique to determine the stresses and displacements appeared on the walls or the bulk solid both for filling and discharge of the silo. However, numerical models must be validated by experimental assays. Due to the high investment required, there are very few experimental installations in the world with full-scale silos for determining the actions produced by the stored materials. Therefore, very few assays can be found in the literature.In this article, it has been accomplished a comparison of the results obtained in several assays conducted using an experimental cylindrical silo with those calculated using a Finite Element Model (FEM) developed by using ANSYS software package. A mid-scale test silo was used to carry out the assays, which is equipped to measure the normal wall pressures and the friction forces. The numerical pressures predicted by the FEM are quite close of those experimentally obtained, both for filling and discharge. In addition, the mean vertical pressure obtained at transition is the same for both sets of results during the filling process. Some differences appear during the initial instants of the discharge, when the numerical model predicts higher mean vertical pressures at transition than those experimentally measured. The FEM predicts higher peak pressures than the experimental ones measured, and at a location closer to the transition than the real position of the sensor placed in the hopper to detect this peak.
Journal: Computers and Electronics in Agriculture - Volume 118, October 2015, Pages 281–289