کد مقاله | کد نشریه | سال انتشار | مقاله انگلیسی | نسخه تمام متن |
---|---|---|---|---|
84795 | 158904 | 2013 | 14 صفحه PDF | دانلود رایگان |
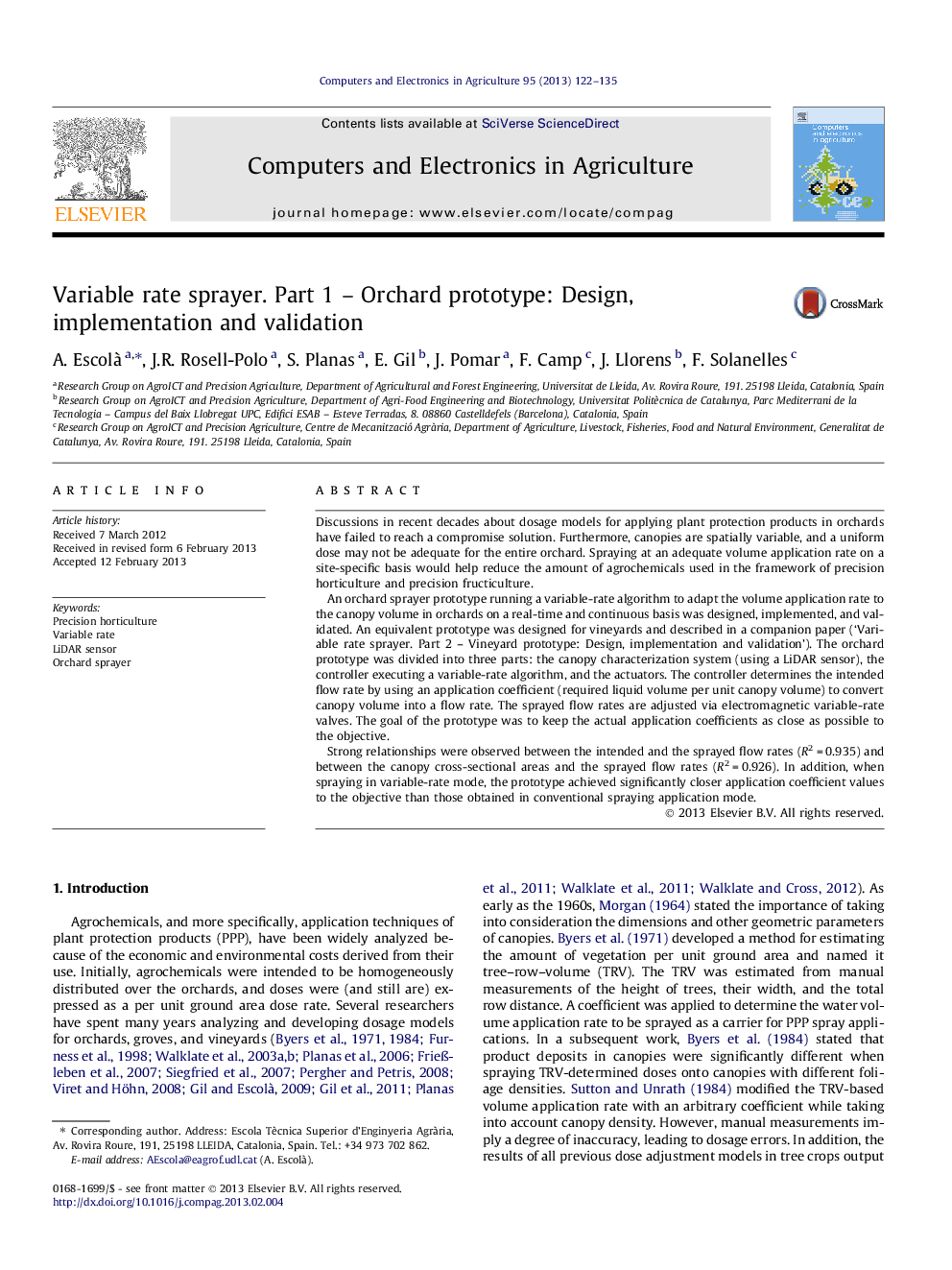
Discussions in recent decades about dosage models for applying plant protection products in orchards have failed to reach a compromise solution. Furthermore, canopies are spatially variable, and a uniform dose may not be adequate for the entire orchard. Spraying at an adequate volume application rate on a site-specific basis would help reduce the amount of agrochemicals used in the framework of precision horticulture and precision fructiculture.An orchard sprayer prototype running a variable-rate algorithm to adapt the volume application rate to the canopy volume in orchards on a real-time and continuous basis was designed, implemented, and validated. An equivalent prototype was designed for vineyards and described in a companion paper (‘Variable rate sprayer. Part 2 – Vineyard prototype: Design, implementation and validation’). The orchard prototype was divided into three parts: the canopy characterization system (using a LiDAR sensor), the controller executing a variable-rate algorithm, and the actuators. The controller determines the intended flow rate by using an application coefficient (required liquid volume per unit canopy volume) to convert canopy volume into a flow rate. The sprayed flow rates are adjusted via electromagnetic variable-rate valves. The goal of the prototype was to keep the actual application coefficients as close as possible to the objective.Strong relationships were observed between the intended and the sprayed flow rates (R2 = 0.935) and between the canopy cross-sectional areas and the sprayed flow rates (R2 = 0.926). In addition, when spraying in variable-rate mode, the prototype achieved significantly closer application coefficient values to the objective than those obtained in conventional spraying application mode.
Figure optionsDownload as PowerPoint slideHighlights
► An orchard sprayer was developed with the ability to vary the sprayed flow rate on a real-time basis.
► The controller runs a variable-rate algorithm that considers canopy variability.
► The detection system determines the cross-sectional area of the canopy.
► The actuators modify the sprayed flow rate respecting the spraying quality.
► Strong correlations are shown among canopy volume, intended flow rate, and sprayed flow rate.
Journal: Computers and Electronics in Agriculture - Volume 95, July 2013, Pages 122–135