کد مقاله | کد نشریه | سال انتشار | مقاله انگلیسی | نسخه تمام متن |
---|---|---|---|---|
148844 | 456423 | 2013 | 12 صفحه PDF | دانلود رایگان |
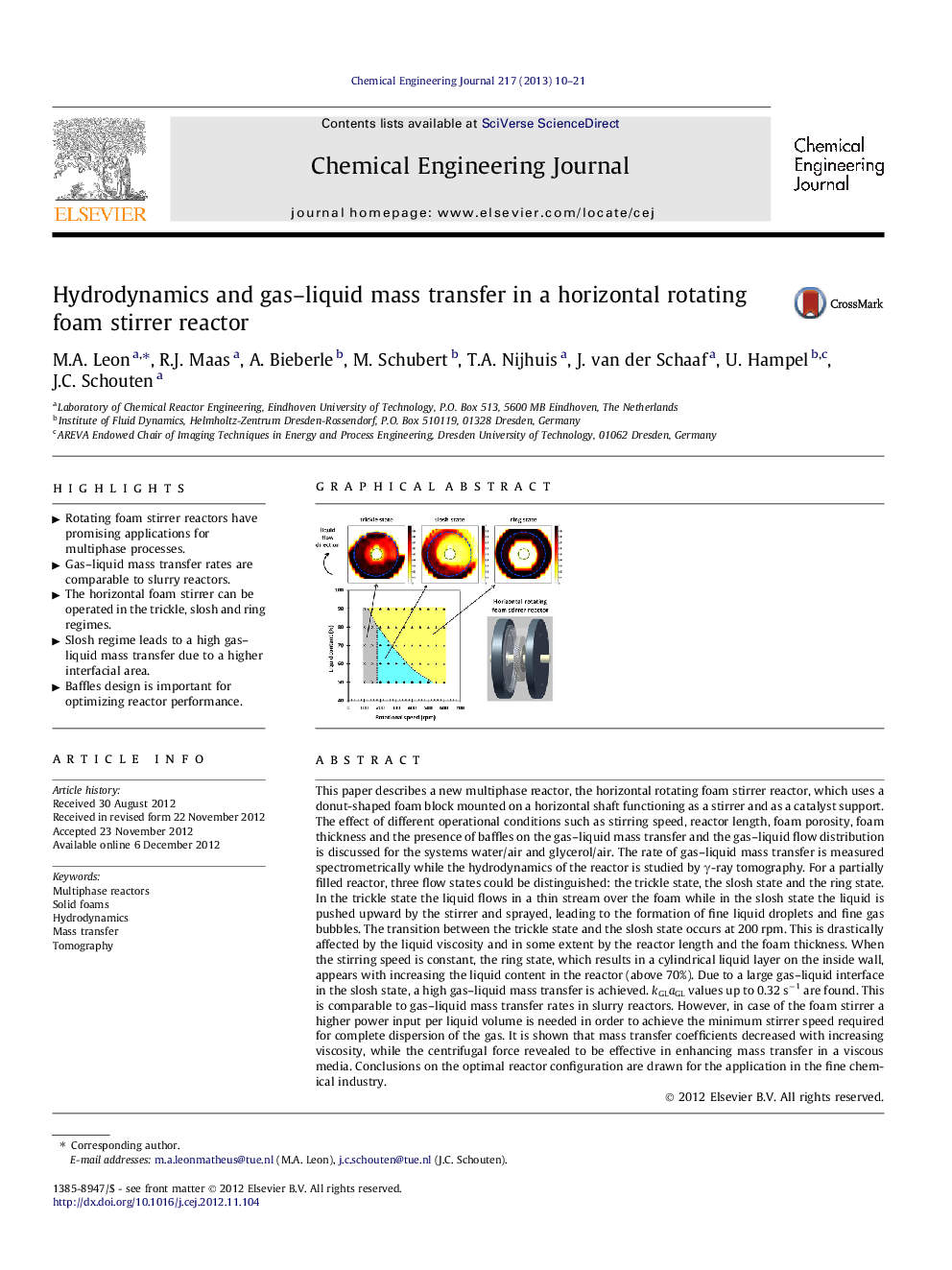
This paper describes a new multiphase reactor, the horizontal rotating foam stirrer reactor, which uses a donut-shaped foam block mounted on a horizontal shaft functioning as a stirrer and as a catalyst support. The effect of different operational conditions such as stirring speed, reactor length, foam porosity, foam thickness and the presence of baffles on the gas–liquid mass transfer and the gas–liquid flow distribution is discussed for the systems water/air and glycerol/air. The rate of gas–liquid mass transfer is measured spectrometrically while the hydrodynamics of the reactor is studied by γ-ray tomography. For a partially filled reactor, three flow states could be distinguished: the trickle state, the slosh state and the ring state. In the trickle state the liquid flows in a thin stream over the foam while in the slosh state the liquid is pushed upward by the stirrer and sprayed, leading to the formation of fine liquid droplets and fine gas bubbles. The transition between the trickle state and the slosh state occurs at 200 rpm. This is drastically affected by the liquid viscosity and in some extent by the reactor length and the foam thickness. When the stirring speed is constant, the ring state, which results in a cylindrical liquid layer on the inside wall, appears with increasing the liquid content in the reactor (above 70%). Due to a large gas–liquid interface in the slosh state, a high gas–liquid mass transfer is achieved. kGLaGL values up to 0.32 s−1 are found. This is comparable to gas–liquid mass transfer rates in slurry reactors. However, in case of the foam stirrer a higher power input per liquid volume is needed in order to achieve the minimum stirrer speed required for complete dispersion of the gas. It is shown that mass transfer coefficients decreased with increasing viscosity, while the centrifugal force revealed to be effective in enhancing mass transfer in a viscous media. Conclusions on the optimal reactor configuration are drawn for the application in the fine chemical industry.
Figure optionsDownload as PowerPoint slideHighlights
► Rotating foam stirrer reactors have promising applications for multiphase processes.
► Gas–liquid mass transfer rates are comparable to slurry reactors.
► The horizontal foam stirrer can be operated in the trickle, slosh and ring regimes.
► Slosh regime leads to a high gas–liquid mass transfer due to a higher interfacial area.
► Baffles design is important for optimizing reactor performance.
Journal: Chemical Engineering Journal - Volume 217, 1 February 2013, Pages 10–21