کد مقاله | کد نشریه | سال انتشار | مقاله انگلیسی | نسخه تمام متن |
---|---|---|---|---|
1577770 | 1514810 | 2012 | 7 صفحه PDF | دانلود رایگان |
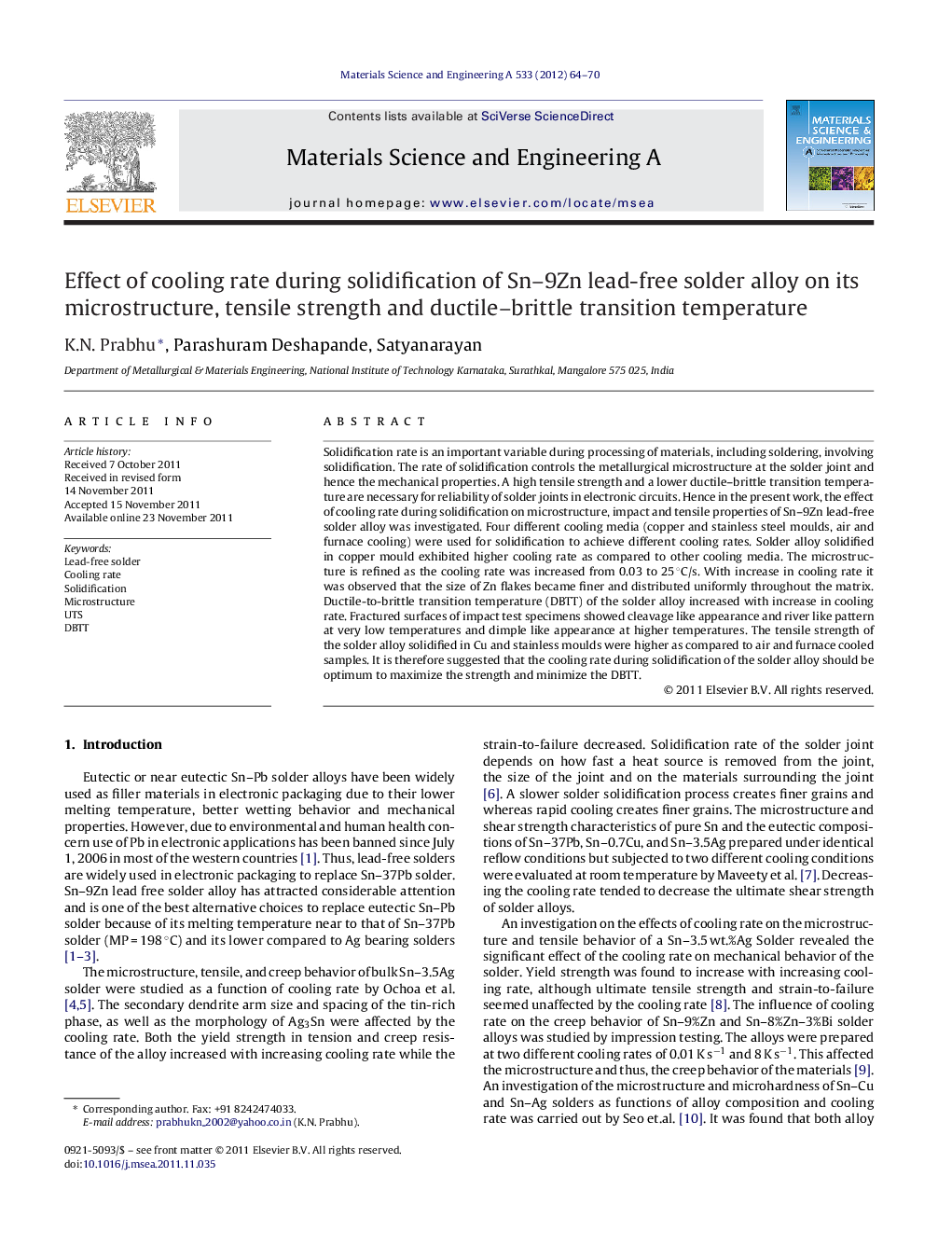
Solidification rate is an important variable during processing of materials, including soldering, involving solidification. The rate of solidification controls the metallurgical microstructure at the solder joint and hence the mechanical properties. A high tensile strength and a lower ductile–brittle transition temperature are necessary for reliability of solder joints in electronic circuits. Hence in the present work, the effect of cooling rate during solidification on microstructure, impact and tensile properties of Sn–9Zn lead-free solder alloy was investigated. Four different cooling media (copper and stainless steel moulds, air and furnace cooling) were used for solidification to achieve different cooling rates. Solder alloy solidified in copper mould exhibited higher cooling rate as compared to other cooling media. The microstructure is refined as the cooling rate was increased from 0.03 to 25 °C/s. With increase in cooling rate it was observed that the size of Zn flakes became finer and distributed uniformly throughout the matrix. Ductile-to-brittle transition temperature (DBTT) of the solder alloy increased with increase in cooling rate. Fractured surfaces of impact test specimens showed cleavage like appearance and river like pattern at very low temperatures and dimple like appearance at higher temperatures. The tensile strength of the solder alloy solidified in Cu and stainless moulds were higher as compared to air and furnace cooled samples. It is therefore suggested that the cooling rate during solidification of the solder alloy should be optimum to maximize the strength and minimize the DBTT.
.Figure optionsDownload as PowerPoint slideHighlights
► Effect of cooling rate on tensile and impact properties of Sn–9Zn alloy was assessed.
► Both DBTT and UTS of the solder alloy increased with increase in cooling rate.
► An optimum cooling rate during solidification would minimize DBTT and maximize UTS.
Journal: Materials Science and Engineering: A - Volume 533, 30 January 2012, Pages 64–70