کد مقاله | کد نشریه | سال انتشار | مقاله انگلیسی | نسخه تمام متن |
---|---|---|---|---|
1659155 | 1517681 | 2010 | 6 صفحه PDF | دانلود رایگان |
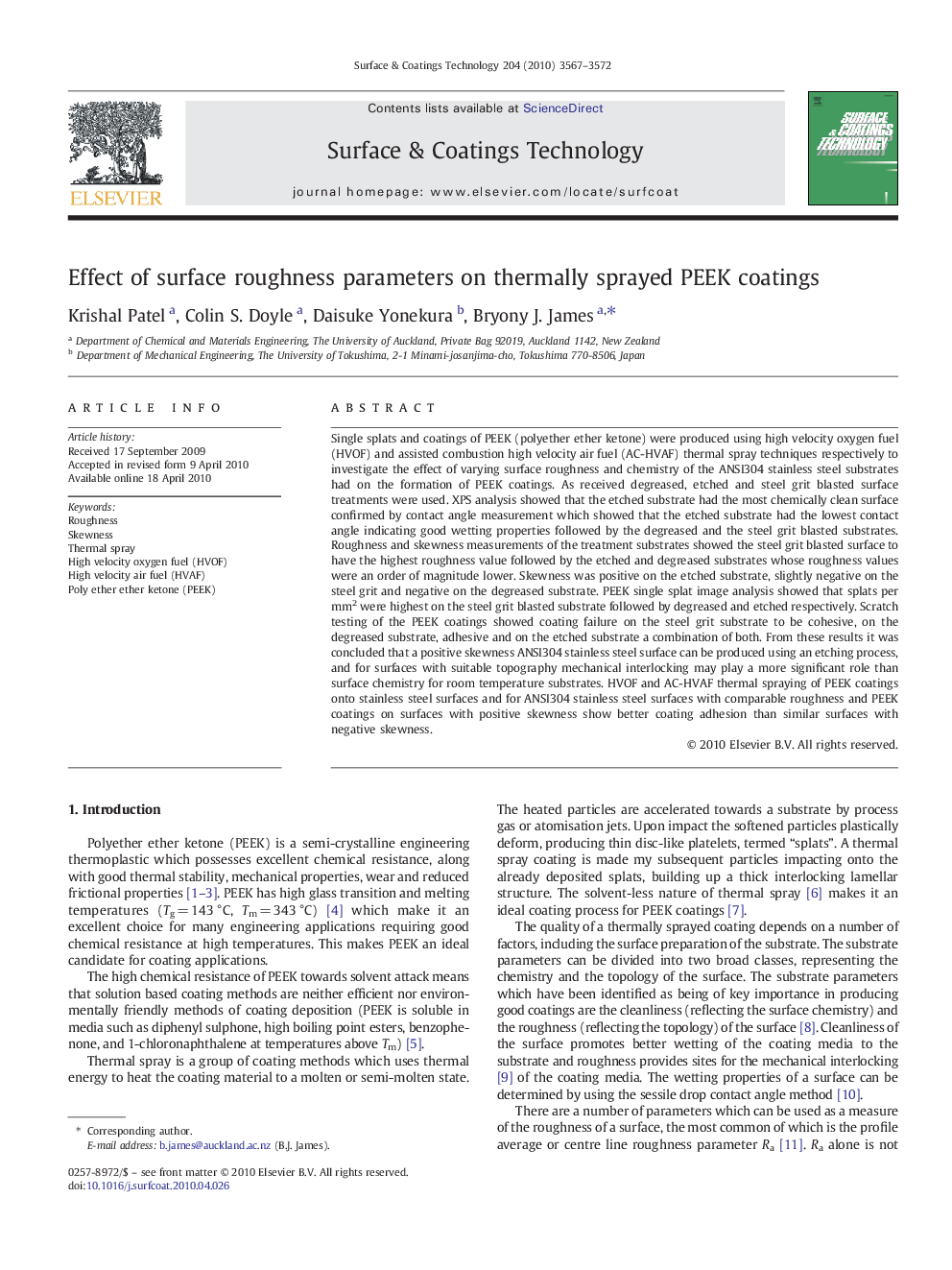
Single splats and coatings of PEEK (polyether ether ketone) were produced using high velocity oxygen fuel (HVOF) and assisted combustion high velocity air fuel (AC-HVAF) thermal spray techniques respectively to investigate the effect of varying surface roughness and chemistry of the ANSI304 stainless steel substrates had on the formation of PEEK coatings. As received degreased, etched and steel grit blasted surface treatments were used. XPS analysis showed that the etched substrate had the most chemically clean surface confirmed by contact angle measurement which showed that the etched substrate had the lowest contact angle indicating good wetting properties followed by the degreased and the steel grit blasted substrates. Roughness and skewness measurements of the treatment substrates showed the steel grit blasted surface to have the highest roughness value followed by the etched and degreased substrates whose roughness values were an order of magnitude lower. Skewness was positive on the etched substrate, slightly negative on the steel grit and negative on the degreased substrate. PEEK single splat image analysis showed that splats per mm2 were highest on the steel grit blasted substrate followed by degreased and etched respectively. Scratch testing of the PEEK coatings showed coating failure on the steel grit substrate to be cohesive, on the degreased substrate, adhesive and on the etched substrate a combination of both. From these results it was concluded that a positive skewness ANSI304 stainless steel surface can be produced using an etching process, and for surfaces with suitable topography mechanical interlocking may play a more significant role than surface chemistry for room temperature substrates. HVOF and AC-HVAF thermal spraying of PEEK coatings onto stainless steel surfaces and for ANSI304 stainless steel surfaces with comparable roughness and PEEK coatings on surfaces with positive skewness show better coating adhesion than similar surfaces with negative skewness.
Journal: Surface and Coatings Technology - Volume 204, Issues 21–22, 15 August 2010, Pages 3567–3572