کد مقاله | کد نشریه | سال انتشار | مقاله انگلیسی | نسخه تمام متن |
---|---|---|---|---|
1757065 | 1523008 | 2016 | 14 صفحه PDF | دانلود رایگان |
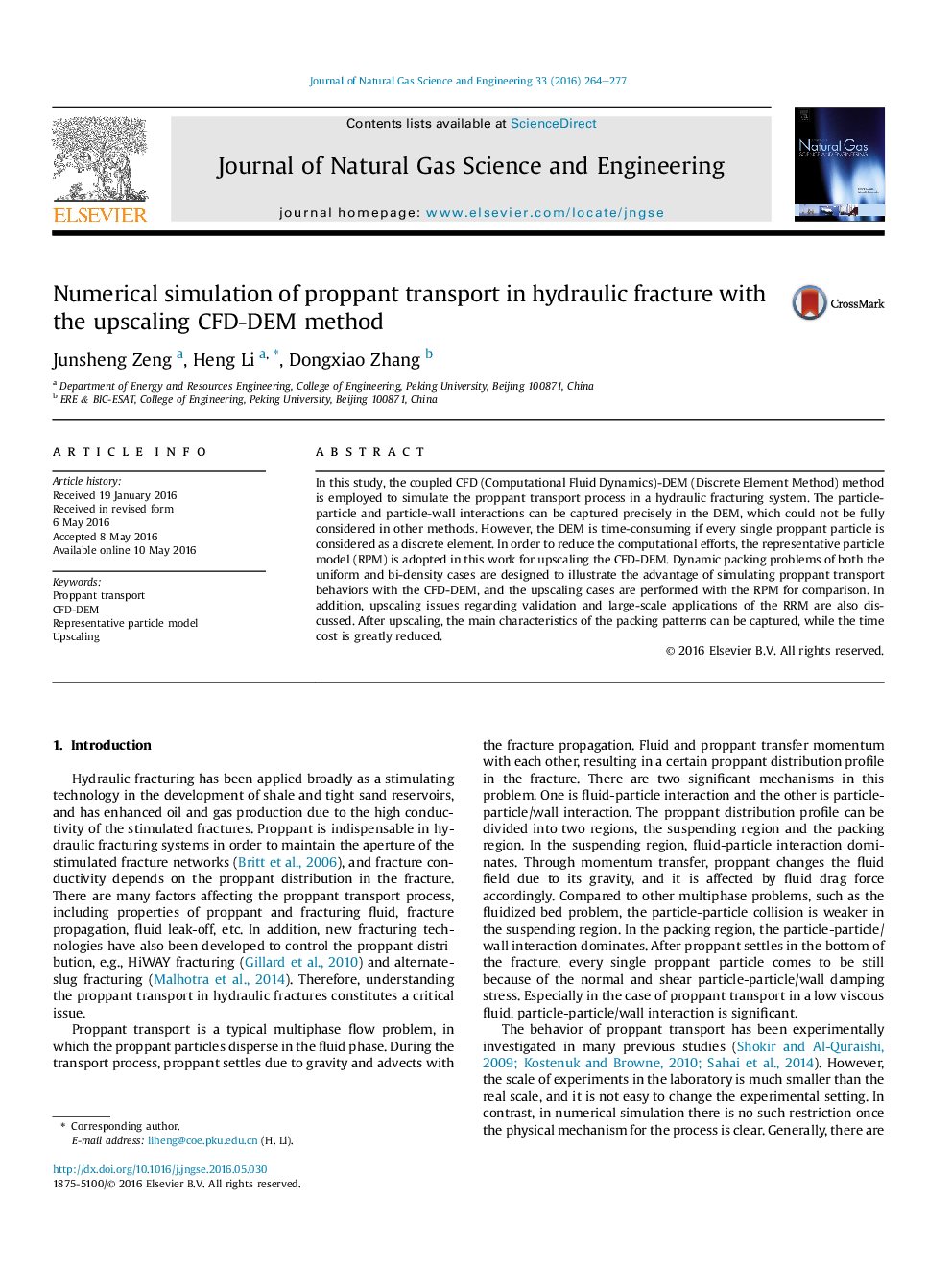
• The coupled CFD-DEM method is applied for proppant transport simulation, where detailed particle information can be obtained.
• The representative particle model is introduced for upscaling the CFD-DEM and reducing computational cost.
• Main characteristics of proppant distribution are captured while computational cost is greatly reduced after upscaling.
In this study, the coupled CFD (Computational Fluid Dynamics)-DEM (Discrete Element Method) method is employed to simulate the proppant transport process in a hydraulic fracturing system. The particle-particle and particle-wall interactions can be captured precisely in the DEM, which could not be fully considered in other methods. However, the DEM is time-consuming if every single proppant particle is considered as a discrete element. In order to reduce the computational efforts, the representative particle model (RPM) is adopted in this work for upscaling the CFD-DEM. Dynamic packing problems of both the uniform and bi-density cases are designed to illustrate the advantage of simulating proppant transport behaviors with the CFD-DEM, and the upscaling cases are performed with the RPM for comparison. In addition, upscaling issues regarding validation and large-scale applications of the RRM are also discussed. After upscaling, the main characteristics of the packing patterns can be captured, while the time cost is greatly reduced.
Journal: Journal of Natural Gas Science and Engineering - Volume 33, July 2016, Pages 264–277