کد مقاله | کد نشریه | سال انتشار | مقاله انگلیسی | نسخه تمام متن |
---|---|---|---|---|
233815 | 465365 | 2011 | 10 صفحه PDF | دانلود رایگان |
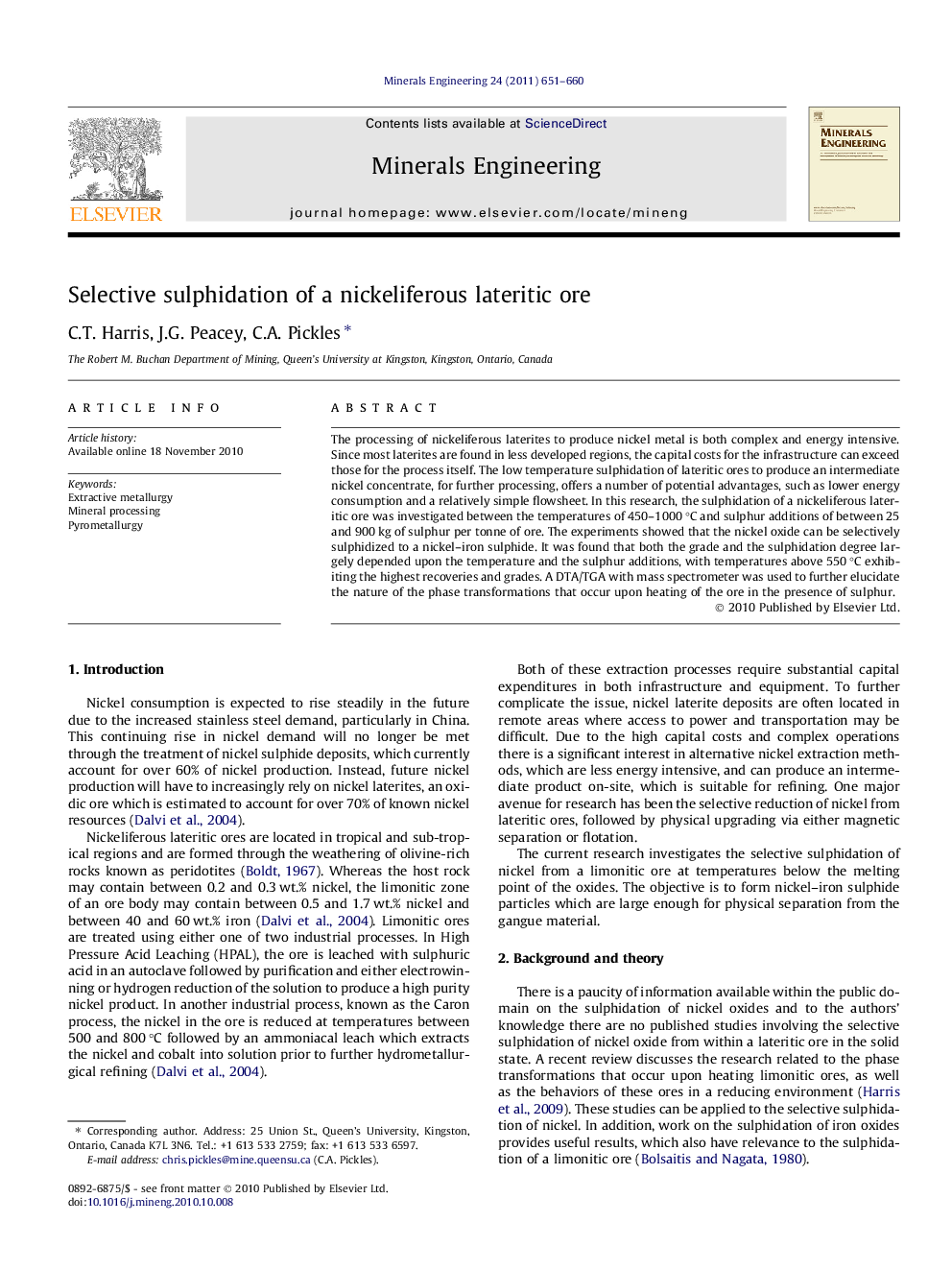
The processing of nickeliferous laterites to produce nickel metal is both complex and energy intensive. Since most laterites are found in less developed regions, the capital costs for the infrastructure can exceed those for the process itself. The low temperature sulphidation of lateritic ores to produce an intermediate nickel concentrate, for further processing, offers a number of potential advantages, such as lower energy consumption and a relatively simple flowsheet. In this research, the sulphidation of a nickeliferous lateritic ore was investigated between the temperatures of 450–1000 °C and sulphur additions of between 25 and 900 kg of sulphur per tonne of ore. The experiments showed that the nickel oxide can be selectively sulphidized to a nickel–iron sulphide. It was found that both the grade and the sulphidation degree largely depended upon the temperature and the sulphur additions, with temperatures above 550 °C exhibiting the highest recoveries and grades. A DTA/TGA with mass spectrometer was used to further elucidate the nature of the phase transformations that occur upon heating of the ore in the presence of sulphur.
Research highlights
► Selective nickel sulphidation from an iron-rich limonitic ore suggests that a nickel extraction of up to 90% is possible, while at the same time minimizing iron recoveries to below about 10 wt.%.
► At low sulphur additions (<300;kg S/tonne ore) a pyrrhotite phase is favored at all temperatures studied. At higher sulphur additions, below 550 °C, a pyrite-rich phase is favoured whereas at higher temperatures a pyrrhotite phase is also formed.
► Nickel extraction and selectivity increased with increasing temperature. A sharp increase coincided with the temperature at which the reduction of hematite to magnetite occurred.
► Overall the thermodynamic description of the Ni–Fe–S–O system adequately predicts the sulphidation and reduction reactions.
Journal: Minerals Engineering - Volume 24, Issue 7, June 2011, Pages 651–660