کد مقاله | کد نشریه | سال انتشار | مقاله انگلیسی | نسخه تمام متن |
---|---|---|---|---|
236855 | 465686 | 2013 | 14 صفحه PDF | دانلود رایگان |
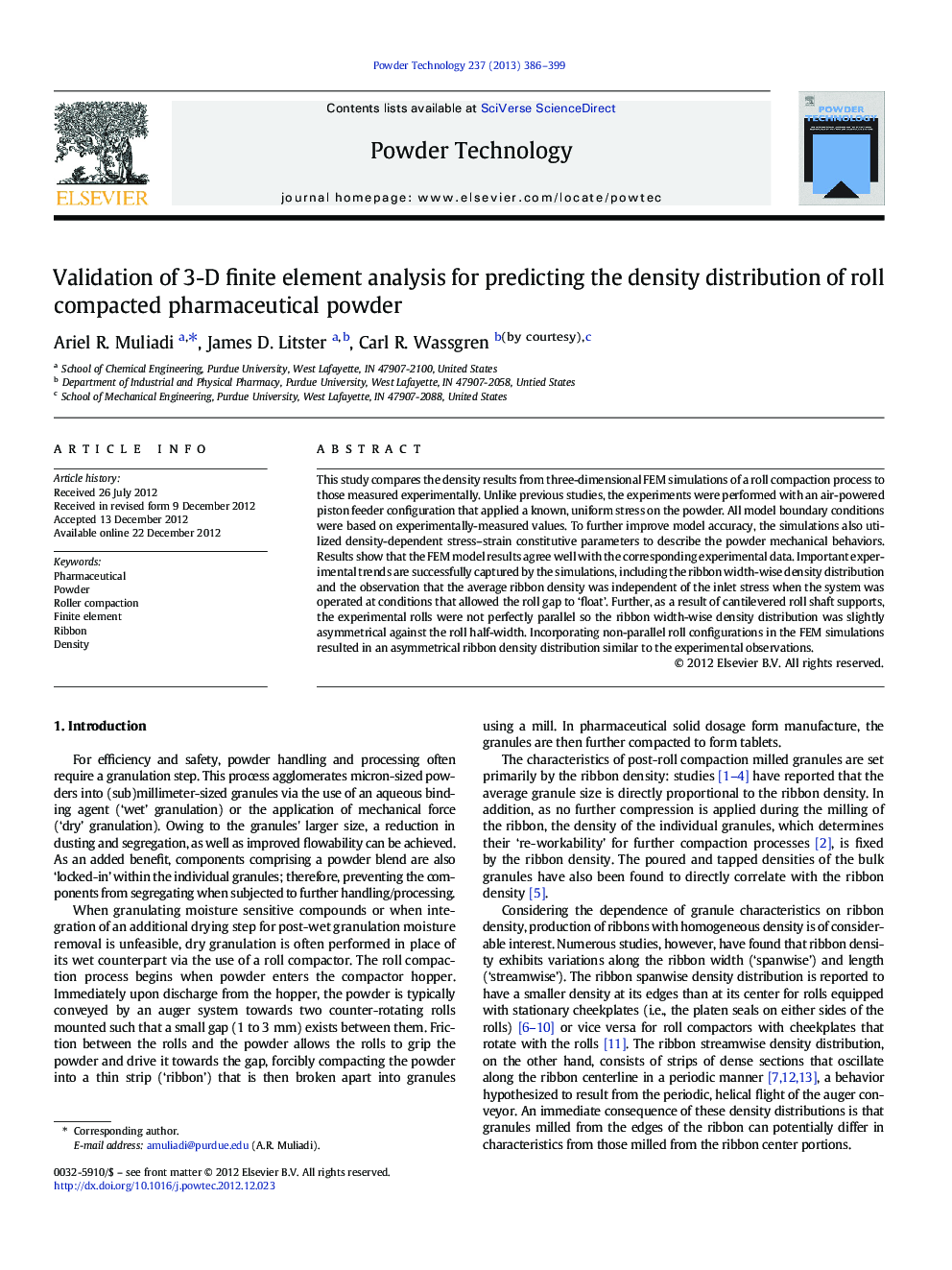
This study compares the density results from three-dimensional FEM simulations of a roll compaction process to those measured experimentally. Unlike previous studies, the experiments were performed with an air-powered piston feeder configuration that applied a known, uniform stress on the powder. All model boundary conditions were based on experimentally-measured values. To further improve model accuracy, the simulations also utilized density-dependent stress–strain constitutive parameters to describe the powder mechanical behaviors. Results show that the FEM model results agree well with the corresponding experimental data. Important experimental trends are successfully captured by the simulations, including the ribbon width-wise density distribution and the observation that the average ribbon density was independent of the inlet stress when the system was operated at conditions that allowed the roll gap to ‘float’. Further, as a result of cantilevered roll shaft supports, the experimental rolls were not perfectly parallel so the ribbon width-wise density distribution was slightly asymmetrical against the roll half-width. Incorporating non-parallel roll configurations in the FEM simulations resulted in an asymmetrical ribbon density distribution similar to the experimental observations.
Finite element method (FEM) simulations of a roll compaction process were performed using experimentally measured data as model inputs. The FEM-predicted density distribution results are compared to those measured experimentally at conditions that closely match the simulation boundary conditions. Excellent agreement between FEM and experimental data is observed.Figure optionsDownload as PowerPoint slideHighlights
► Density results from FEM simulations are validated against experimental measurements.
► An air-powered piston that applies a known, uniform stress on the powder is used.
► All model boundary conditions were based on experimentally-measured values.
► The simulations also utilized density-dependent stress–strain constitutive parameters.
► FEM model density results agree well with the corresponding experimental data.
Journal: Powder Technology - Volume 237, March 2013, Pages 386–399