کد مقاله | کد نشریه | سال انتشار | مقاله انگلیسی | نسخه تمام متن |
---|---|---|---|---|
4990401 | 1457103 | 2017 | 8 صفحه PDF | دانلود رایگان |
عنوان انگلیسی مقاله ISI
Electric motor thermal management system using L-shaped flat heat pipes
دانلود مقاله + سفارش ترجمه
دانلود مقاله ISI انگلیسی
رایگان برای ایرانیان
کلمات کلیدی
موضوعات مرتبط
مهندسی و علوم پایه
مهندسی شیمی
جریان سیال و فرایندهای انتقال
پیش نمایش صفحه اول مقاله
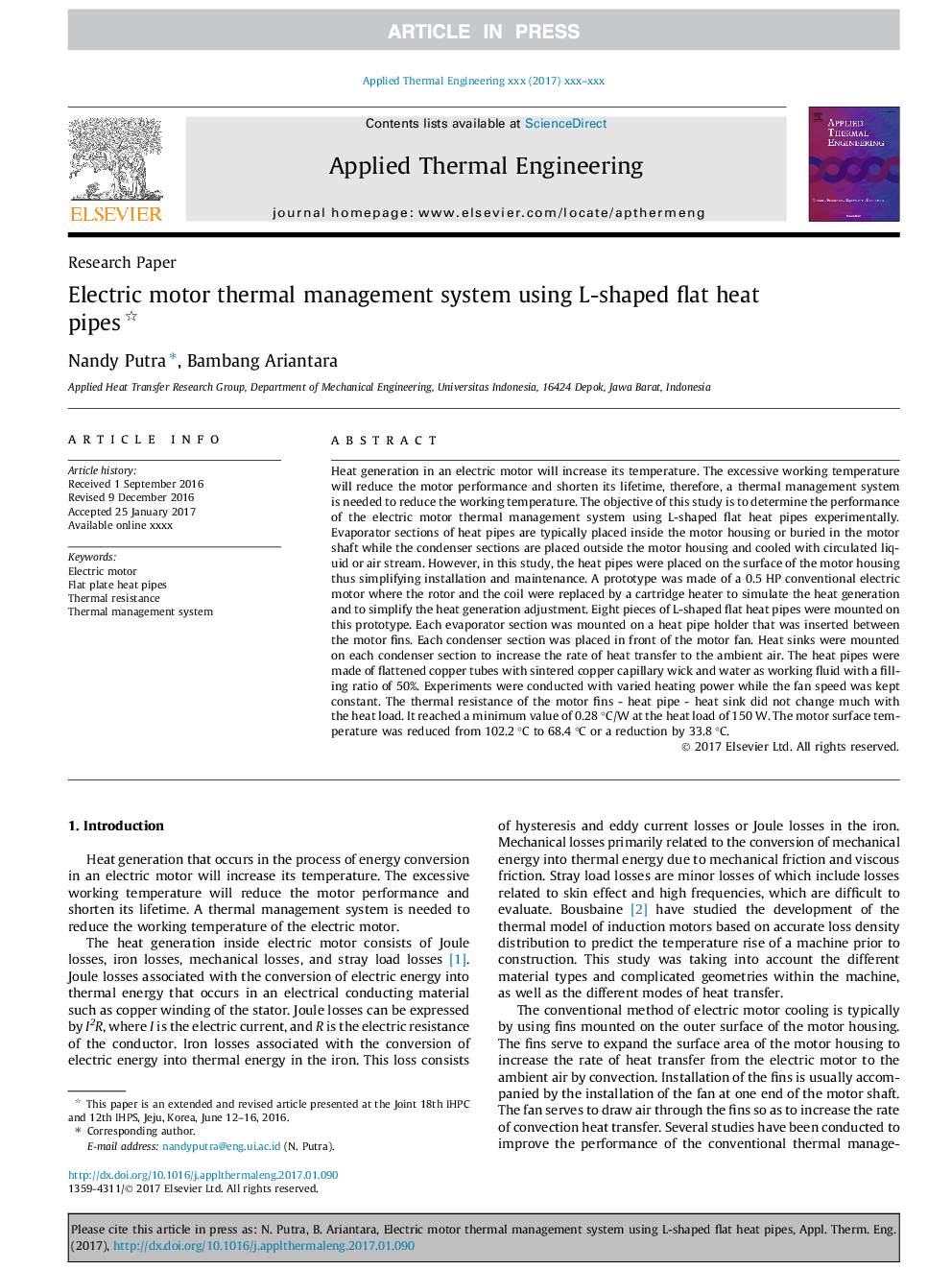
چکیده انگلیسی
Heat generation in an electric motor will increase its temperature. The excessive working temperature will reduce the motor performance and shorten its lifetime, therefore, a thermal management system is needed to reduce the working temperature. The objective of this study is to determine the performance of the electric motor thermal management system using L-shaped flat heat pipes experimentally. Evaporator sections of heat pipes are typically placed inside the motor housing or buried in the motor shaft while the condenser sections are placed outside the motor housing and cooled with circulated liquid or air stream. However, in this study, the heat pipes were placed on the surface of the motor housing thus simplifying installation and maintenance. A prototype was made of a 0.5 HP conventional electric motor where the rotor and the coil were replaced by a cartridge heater to simulate the heat generation and to simplify the heat generation adjustment. Eight pieces of L-shaped flat heat pipes were mounted on this prototype. Each evaporator section was mounted on a heat pipe holder that was inserted between the motor fins. Each condenser section was placed in front of the motor fan. Heat sinks were mounted on each condenser section to increase the rate of heat transfer to the ambient air. The heat pipes were made of flattened copper tubes with sintered copper capillary wick and water as working fluid with a filling ratio of 50%. Experiments were conducted with varied heating power while the fan speed was kept constant. The thermal resistance of the motor fins - heat pipe - heat sink did not change much with the heat load. It reached a minimum value of 0.28 °C/W at the heat load of 150 W. The motor surface temperature was reduced from 102.2 °C to 68.4 °C or a reduction by 33.8 °C.
ناشر
Database: Elsevier - ScienceDirect (ساینس دایرکت)
Journal: Applied Thermal Engineering - Volume 126, 5 November 2017, Pages 1156-1163
Journal: Applied Thermal Engineering - Volume 126, 5 November 2017, Pages 1156-1163
نویسندگان
Nandy Putra, Bambang Ariantara,