کد مقاله | کد نشریه | سال انتشار | مقاله انگلیسی | نسخه تمام متن |
---|---|---|---|---|
64723 | 48368 | 2016 | 10 صفحه PDF | دانلود رایگان |
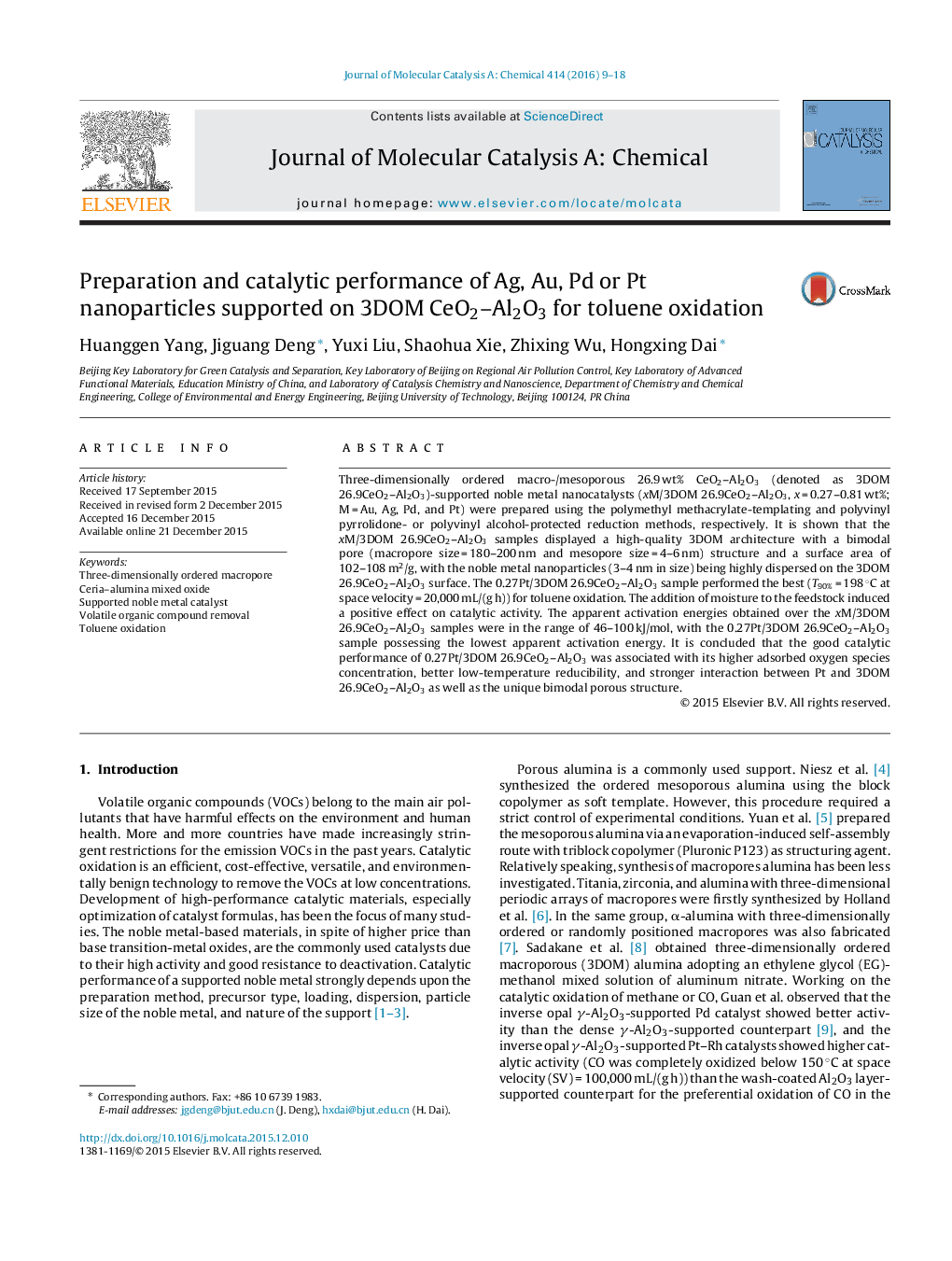
• 3DOM CeO2–Al2O3 with ordered mesopore walls is fabricated via the PMMA-templating route.
• 3DOM 26.9CeO2–Al2O3 displays a bimodal macro/mesoporous architecture.
• 3DOM 26.9CeO2–Al2O3 supported noble metal is prepared via the polymer-protective reduction.
• 0.27Pt/3DOM 26.9CeO2–Al2O3 performs the best in toluene oxidation.
• Oads content, reducibility, and noble metal—support interaction govern the catalytic activity.
Three-dimensionally ordered macro-/mesoporous 26.9 wt% CeO2–Al2O3 (denoted as 3DOM 26.9CeO2–Al2O3)-supported noble metal nanocatalysts (xM/3DOM 26.9CeO2–Al2O3, x = 0.27–0.81 wt%; M = Au, Ag, Pd, and Pt) were prepared using the polymethyl methacrylate-templating and polyvinyl pyrrolidone- or polyvinyl alcohol-protected reduction methods, respectively. It is shown that the xM/3DOM 26.9CeO2–Al2O3 samples displayed a high-quality 3DOM architecture with a bimodal pore (macropore size = 180–200 nm and mesopore size = 4–6 nm) structure and a surface area of 102–108 m2/g, with the noble metal nanoparticles (3–4 nm in size) being highly dispersed on the 3DOM 26.9CeO2–Al2O3 surface. The 0.27Pt/3DOM 26.9CeO2–Al2O3 sample performed the best (T90% = 198 °C at space velocity = 20,000 mL/(g h)) for toluene oxidation. The addition of moisture to the feedstock induced a positive effect on catalytic activity. The apparent activation energies obtained over the xM/3DOM 26.9CeO2–Al2O3 samples were in the range of 46–100 kJ/mol, with the 0.27Pt/3DOM 26.9CeO2–Al2O3 sample possessing the lowest apparent activation energy. It is concluded that the good catalytic performance of 0.27Pt/3DOM 26.9CeO2–Al2O3 was associated with its higher adsorbed oxygen species concentration, better low-temperature reducibility, and stronger interaction between Pt and 3DOM 26.9CeO2–Al2O3 as well as the unique bimodal porous structure.
Figure optionsDownload high-quality image (175 K)Download as PowerPoint slide
Journal: Journal of Molecular Catalysis A: Chemical - Volume 414, April 2016, Pages 9–18