کد مقاله | کد نشریه | سال انتشار | مقاله انگلیسی | نسخه تمام متن |
---|---|---|---|---|
688790 | 1460372 | 2015 | 16 صفحه PDF | دانلود رایگان |
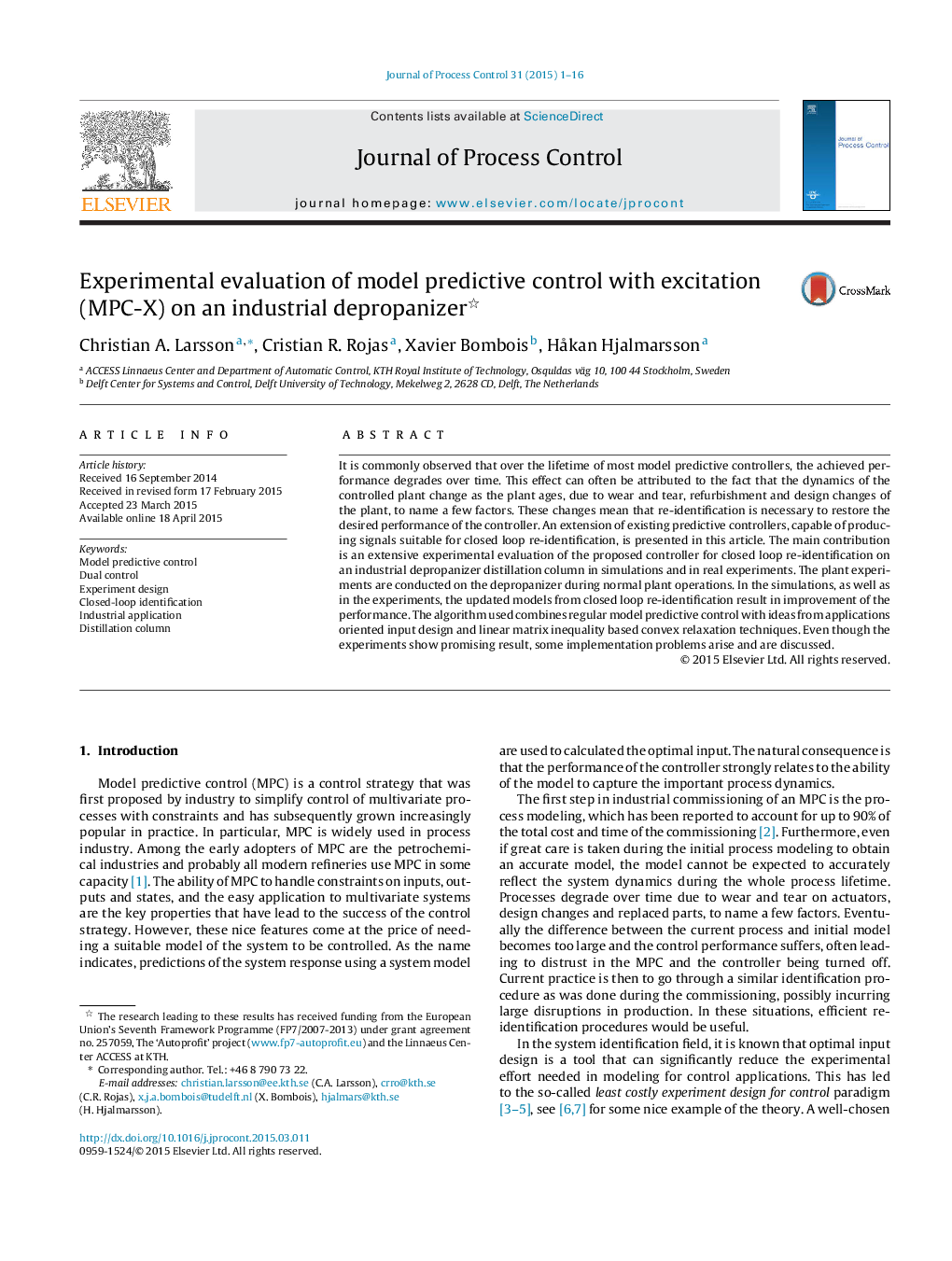
• We present a dual MPC for closed-loop identification.
• An application-oriented approach gives cheap identification and high-quality models.
• The method is implemented and extensively tested on a real industrial process.
• The updated models from reidentification improve performance in all experiments.
It is commonly observed that over the lifetime of most model predictive controllers, the achieved performance degrades over time. This effect can often be attributed to the fact that the dynamics of the controlled plant change as the plant ages, due to wear and tear, refurbishment and design changes of the plant, to name a few factors. These changes mean that re-identification is necessary to restore the desired performance of the controller. An extension of existing predictive controllers, capable of producing signals suitable for closed loop re-identification, is presented in this article. The main contribution is an extensive experimental evaluation of the proposed controller for closed loop re-identification on an industrial depropanizer distillation column in simulations and in real experiments. The plant experiments are conducted on the depropanizer during normal plant operations. In the simulations, as well as in the experiments, the updated models from closed loop re-identification result in improvement of the performance. The algorithm used combines regular model predictive control with ideas from applications oriented input design and linear matrix inequality based convex relaxation techniques. Even though the experiments show promising result, some implementation problems arise and are discussed.
Journal: Journal of Process Control - Volume 31, July 2015, Pages 1–16