کد مقاله | کد نشریه | سال انتشار | مقاله انگلیسی | نسخه تمام متن |
---|---|---|---|---|
700562 | 890880 | 2007 | 12 صفحه PDF | دانلود رایگان |
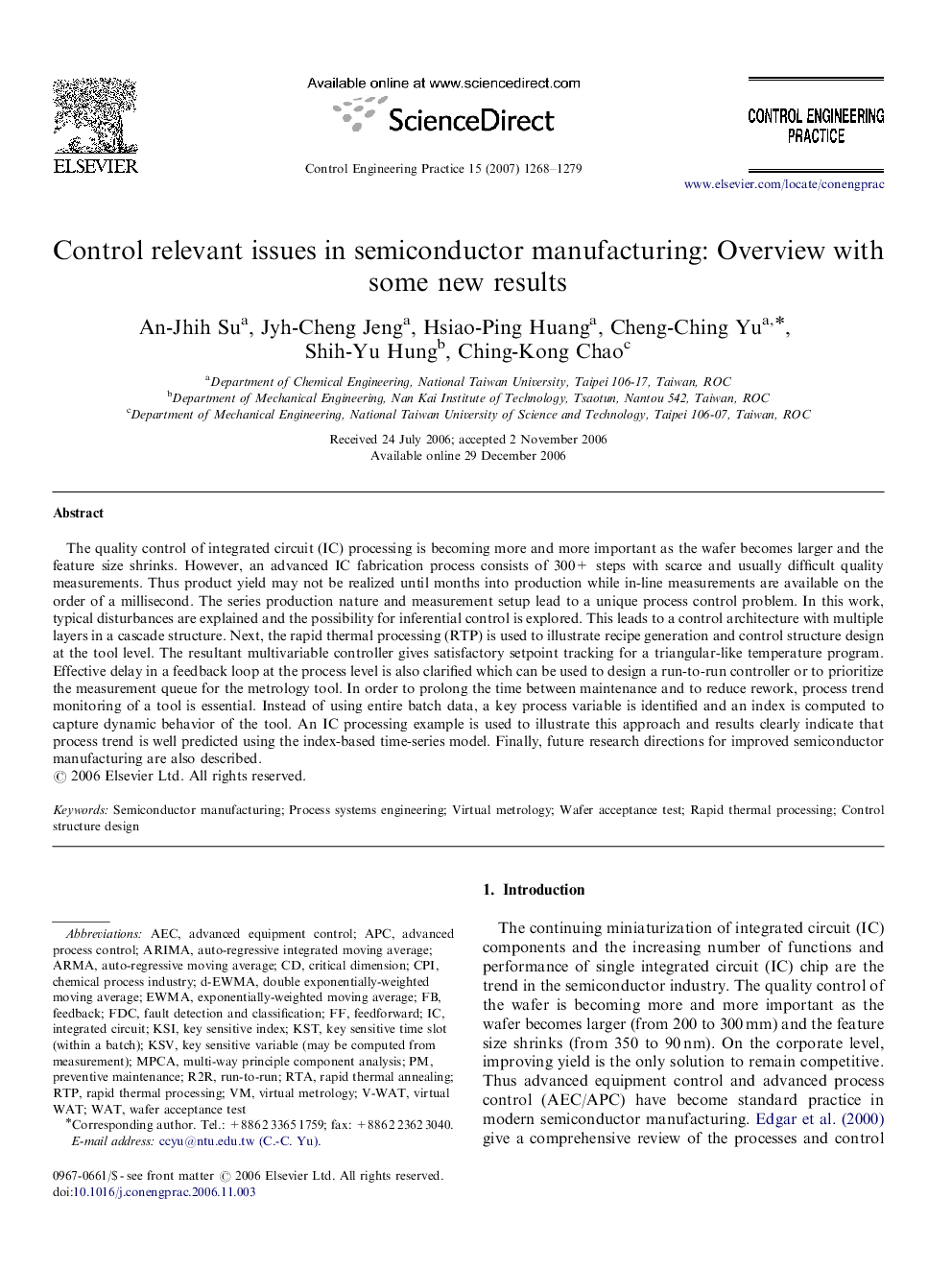
The quality control of integrated circuit (IC) processing is becoming more and more important as the wafer becomes larger and the feature size shrinks. However, an advanced IC fabrication process consists of 300+ steps with scarce and usually difficult quality measurements. Thus product yield may not be realized until months into production while in-line measurements are available on the order of a millisecond. The series production nature and measurement setup lead to a unique process control problem. In this work, typical disturbances are explained and the possibility for inferential control is explored. This leads to a control architecture with multiple layers in a cascade structure. Next, the rapid thermal processing (RTP) is used to illustrate recipe generation and control structure design at the tool level. The resultant multivariable controller gives satisfactory setpoint tracking for a triangular-like temperature program. Effective delay in a feedback loop at the process level is also clarified which can be used to design a run-to-run controller or to prioritize the measurement queue for the metrology tool. In order to prolong the time between maintenance and to reduce rework, process trend monitoring of a tool is essential. Instead of using entire batch data, a key process variable is identified and an index is computed to capture dynamic behavior of the tool. An IC processing example is used to illustrate this approach and results clearly indicate that process trend is well predicted using the index-based time-series model. Finally, future research directions for improved semiconductor manufacturing are also described.
Journal: Control Engineering Practice - Volume 15, Issue 10, October 2007, Pages 1268–1279