کد مقاله | کد نشریه | سال انتشار | مقاله انگلیسی | نسخه تمام متن |
---|---|---|---|---|
765717 | 1462895 | 2013 | 9 صفحه PDF | دانلود رایگان |
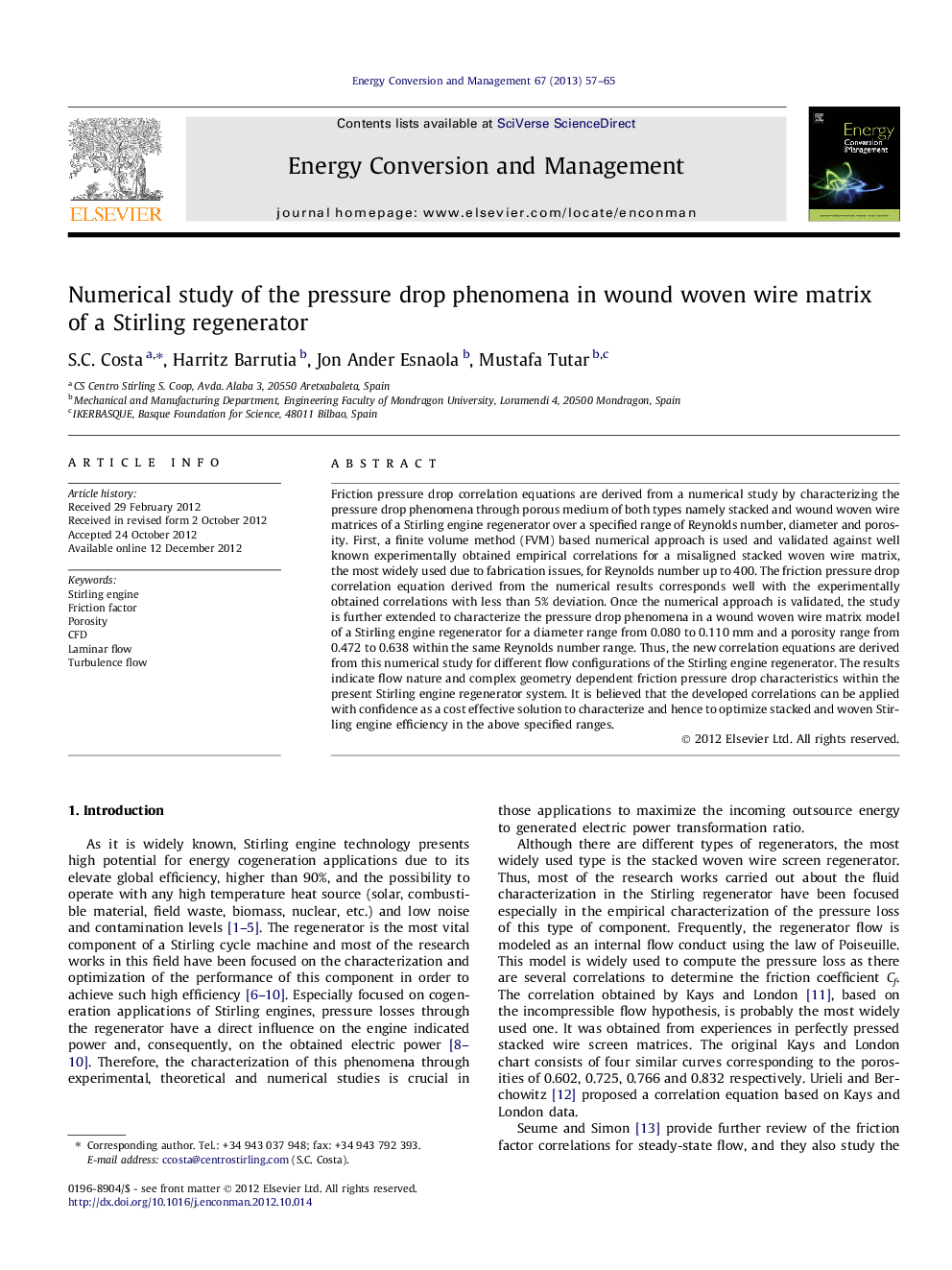
Friction pressure drop correlation equations are derived from a numerical study by characterizing the pressure drop phenomena through porous medium of both types namely stacked and wound woven wire matrices of a Stirling engine regenerator over a specified range of Reynolds number, diameter and porosity. First, a finite volume method (FVM) based numerical approach is used and validated against well known experimentally obtained empirical correlations for a misaligned stacked woven wire matrix, the most widely used due to fabrication issues, for Reynolds number up to 400. The friction pressure drop correlation equation derived from the numerical results corresponds well with the experimentally obtained correlations with less than 5% deviation. Once the numerical approach is validated, the study is further extended to characterize the pressure drop phenomena in a wound woven wire matrix model of a Stirling engine regenerator for a diameter range from 0.080 to 0.110 mm and a porosity range from 0.472 to 0.638 within the same Reynolds number range. Thus, the new correlation equations are derived from this numerical study for different flow configurations of the Stirling engine regenerator. The results indicate flow nature and complex geometry dependent friction pressure drop characteristics within the present Stirling engine regenerator system. It is believed that the developed correlations can be applied with confidence as a cost effective solution to characterize and hence to optimize stacked and woven Stirling engine efficiency in the above specified ranges.
► Numerically derived correlations for wound woven wire regenerator pressure drop are proposed.
► Correlations can be used as a cost effective tool to optimize the pressure losses through matrix.
► The wound woven matrices provide higher pressure drop compared to stacked woven matrix.
► The derived correlations can be used for Reynolds number range from 0 to 400.
Journal: Energy Conversion and Management - Volume 67, March 2013, Pages 57–65