کد مقاله | کد نشریه | سال انتشار | مقاله انگلیسی | نسخه تمام متن |
---|---|---|---|---|
777879 | 1463835 | 2008 | 17 صفحه PDF | دانلود رایگان |
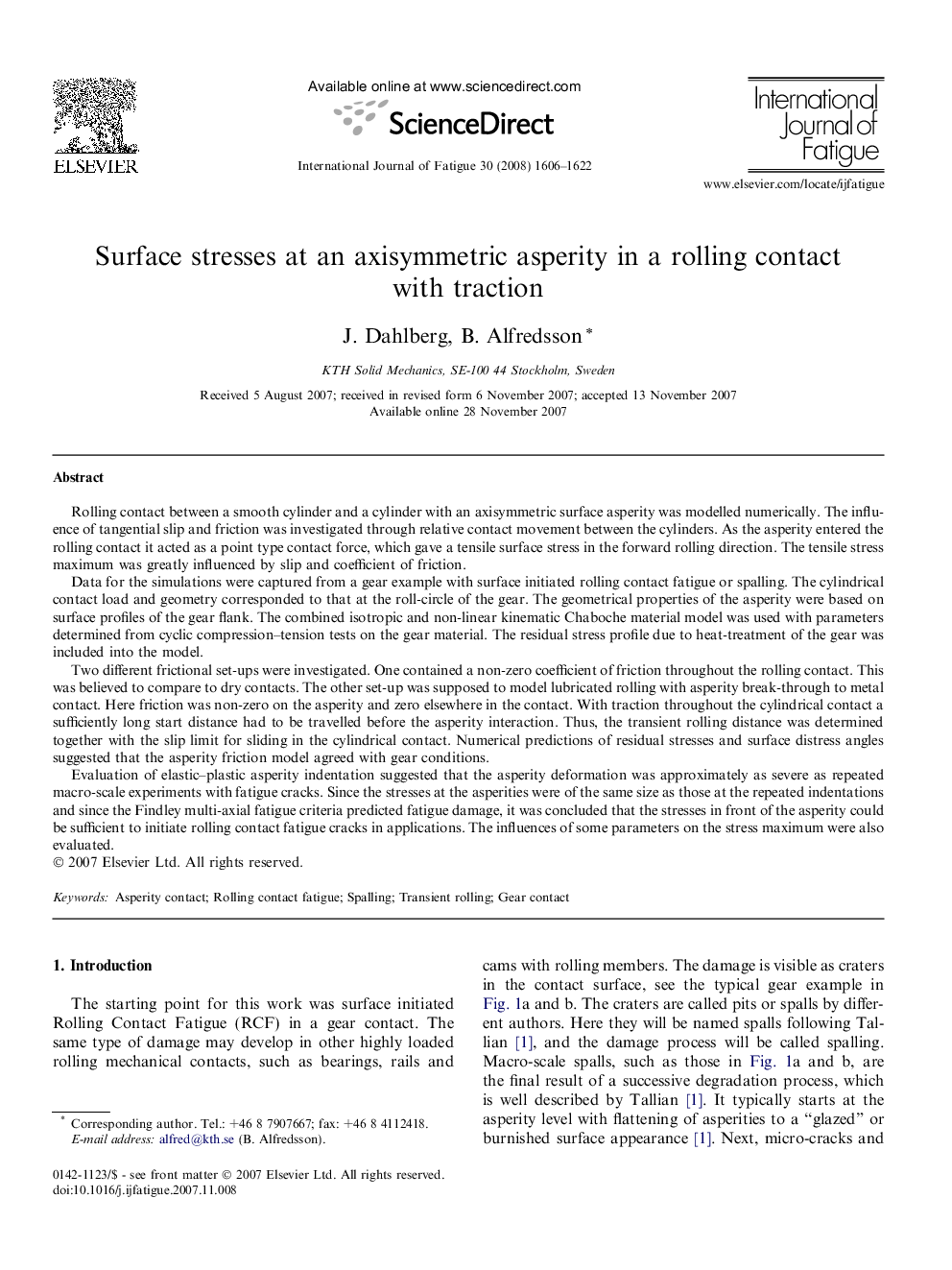
Rolling contact between a smooth cylinder and a cylinder with an axisymmetric surface asperity was modelled numerically. The influence of tangential slip and friction was investigated through relative contact movement between the cylinders. As the asperity entered the rolling contact it acted as a point type contact force, which gave a tensile surface stress in the forward rolling direction. The tensile stress maximum was greatly influenced by slip and coefficient of friction.Data for the simulations were captured from a gear example with surface initiated rolling contact fatigue or spalling. The cylindrical contact load and geometry corresponded to that at the roll-circle of the gear. The geometrical properties of the asperity were based on surface profiles of the gear flank. The combined isotropic and non-linear kinematic Chaboche material model was used with parameters determined from cyclic compression–tension tests on the gear material. The residual stress profile due to heat-treatment of the gear was included into the model.Two different frictional set-ups were investigated. One contained a non-zero coefficient of friction throughout the rolling contact. This was believed to compare to dry contacts. The other set-up was supposed to model lubricated rolling with asperity break-through to metal contact. Here friction was non-zero on the asperity and zero elsewhere in the contact. With traction throughout the cylindrical contact a sufficiently long start distance had to be travelled before the asperity interaction. Thus, the transient rolling distance was determined together with the slip limit for sliding in the cylindrical contact. Numerical predictions of residual stresses and surface distress angles suggested that the asperity friction model agreed with gear conditions.Evaluation of elastic–plastic asperity indentation suggested that the asperity deformation was approximately as severe as repeated macro-scale experiments with fatigue cracks. Since the stresses at the asperities were of the same size as those at the repeated indentations and since the Findley multi-axial fatigue criteria predicted fatigue damage, it was concluded that the stresses in front of the asperity could be sufficient to initiate rolling contact fatigue cracks in applications. The influences of some parameters on the stress maximum were also evaluated.
Journal: International Journal of Fatigue - Volume 30, Issue 9, September 2008, Pages 1606–1622